Chemical Vapor Deposition (CVD) is a widely used technique for creating thin films with specific properties, such as high purity, uniformity, and density. It overcomes limitations of other deposition methods like physical vapor deposition (PVD) by enabling non-line-of-sight deposition, which allows uniform coating of complex and irregular surfaces. CVD is versatile, capable of depositing metallic, ceramic, and semiconducting materials, and offers advantages like selective deposition, lower processing temperatures, and autocatalytic properties for certain metals. It is highly scalable, economical for large-scale production, and produces films with excellent optical, thermal, and electrical properties, making it ideal for applications in electronics, wear-resistant coatings, and more.
Key Points Explained:
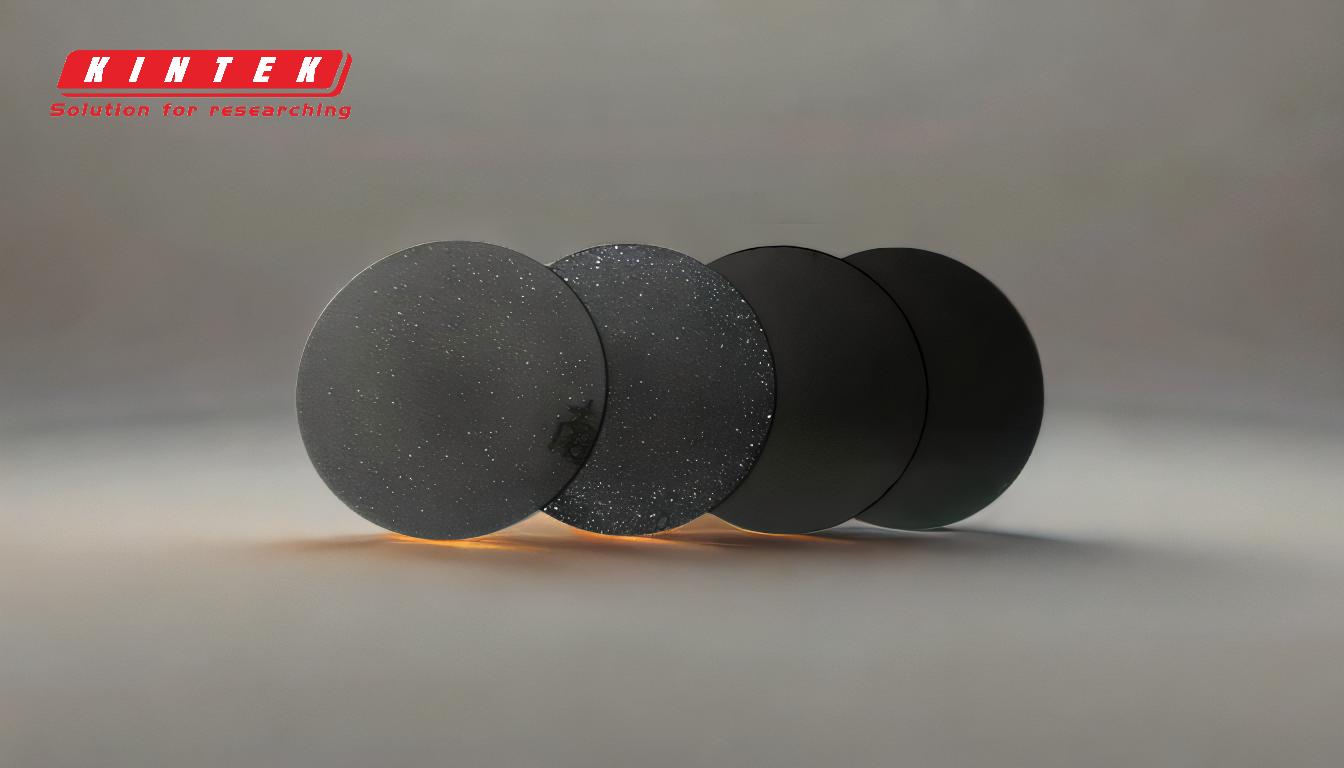
-
Definition of CVD:
- CVD is a process where thin films are deposited onto a substrate through chemical reactions of precursor gases in a controlled environment. The process involves the decomposition or reaction of gaseous compounds to form a solid film on the substrate.
-
Non-Line-of-Sight Deposition:
- Unlike physical vapor deposition (PVD), CVD does not require a direct line of sight between the source and the substrate. This allows for uniform coating of complex, irregular, or restricted-access surfaces, making it highly versatile for various applications.
-
Advantages of CVD:
- High Purity and Uniformity: Precursor gases can be purified to remove impurities, and the deposition process can be tightly controlled to ensure uniform thickness and composition.
- Versatility: CVD can deposit a wide range of materials, including metals, ceramics, and semiconductors, with specific properties like hardness, wear resistance, or electrical conductivity.
- Scalability: The deposition rate can be easily controlled by adjusting the flow rate of precursor gases, making CVD suitable for large-scale manufacturing.
- Economical: CVD allows for batch processing, where many parts can be coated simultaneously, reducing production costs.
-
Flexibility in Deposition:
- CVD offers flexibility in terms of deposition timing and conditions. It can operate at atmospheric pressure or in a vacuum, and additional elements like plasma or initiators can be introduced to enhance reactivity and film properties.
-
Autocatalytic Properties:
- Many metal CVD processes are autocatalytic, meaning the deposited material can catalyze further deposition. This self-sustaining process improves efficiency and reduces the need for external catalysts.
-
Applications of CVD:
- Electronics: CVD is ideal for creating extremely thin layers of materials, such as those required in electrical circuits.
- Wear-Resistant Coatings: CVD can deposit very hard, durable films that are resistant to wear and corrosion.
- Optical and Thermal Properties: Films produced by CVD often have excellent optical and thermal properties, making them suitable for applications in optics and thermal management.
-
Comparison with Other Deposition Techniques:
- CVD is often preferred over PVD for its ability to coat complex shapes uniformly and its capacity for selective deposition. It also operates at lower temperatures compared to some other techniques, reducing thermal stress on the substrate.
-
Economic and Production Advantages:
- CVD is cost-effective for mass production due to its ability to coat multiple parts simultaneously and its high deposition rates. The process is also stable, producing consistent film quality across large batches.
In summary, CVD is a highly versatile and efficient method for depositing thin films with precise properties. Its ability to uniformly coat complex surfaces, combined with its scalability and economic advantages, makes it a preferred choice in industries ranging from electronics to wear-resistant coatings.
Summary Table:
Key Aspect | Description |
---|---|
Definition | CVD deposits thin films via chemical reactions of precursor gases. |
Non-Line-of-Sight Deposition | Uniformly coats complex, irregular surfaces without direct line of sight. |
Advantages | High purity, versatility, scalability, and cost-effectiveness. |
Applications | Electronics, wear-resistant coatings, optics, and thermal management. |
Comparison with PVD | Preferred for uniform coating of complex shapes and lower processing temperatures. |
Economic Benefits | Cost-effective for mass production with stable, consistent film quality. |
Unlock the potential of CVD for your applications—contact our experts today to learn more!