Deposition methods refer to the techniques used to apply thin layers of material onto a substrate. These methods are essential in various industries, including electronics, automotive, medical devices, and more. The primary goal is to create high-quality, uniform thin films with specific properties. Deposition techniques are broadly categorized into two main types: Physical Vapor Deposition (PVD) and Chemical Vapor Deposition (CVD). PVD methods, such as evaporation and sputtering, rely on physical processes like thermal energy or mechanical impact to deposit materials. CVD methods involve chemical reactions to form the thin film. Each method has its advantages and is chosen based on the desired film properties, substrate material, and application requirements.
Key Points Explained:
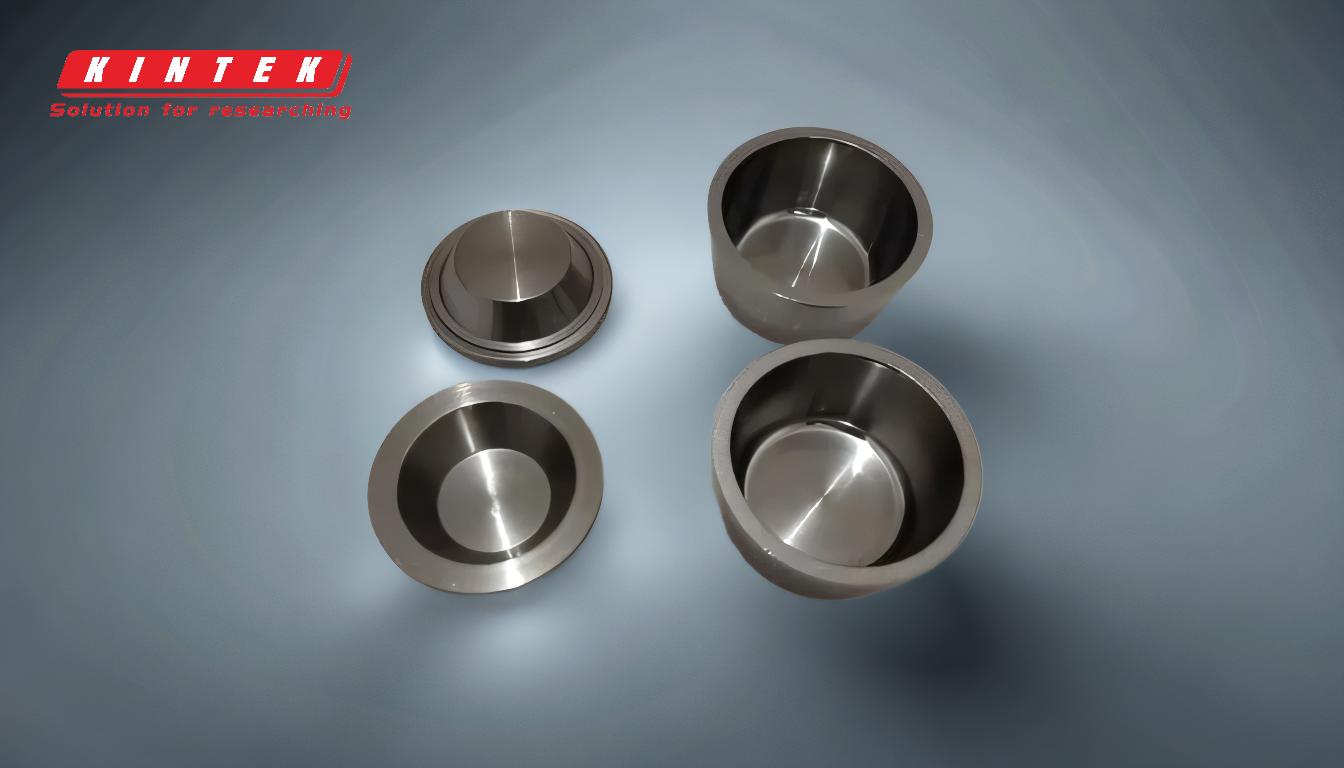
-
Definition of Deposition Methods:
- Deposition methods are techniques used to apply thin layers of material onto a substrate. These layers, known as thin films, are crucial in various applications, including electronics, optics, and coatings.
-
Categories of Deposition Methods:
-
Physical Vapor Deposition (PVD):
- PVD methods rely on physical processes to deposit materials. Common techniques include:
- Evaporation: This involves heating the target material until it evaporates, then allowing the vapor to condense on the substrate.
- Sputtering: This technique uses plasma or gaseous atoms to dislodge atoms from a target material, which then deposit onto the substrate.
- PVD methods rely on physical processes to deposit materials. Common techniques include:
-
Chemical Vapor Deposition (CVD):
- CVD methods involve chemical reactions to form the thin film. Common techniques include:
- Chemical Bath Deposition: This involves immersing the substrate in a chemical solution that reacts to form a thin film.
- Electroplating: This uses an electric current to reduce dissolved metal cations, forming a coherent metal coating on the substrate.
- Molecular Beam Epitaxy (MBE): This is a highly controlled process where atomic or molecular beams are directed at the substrate to grow thin films layer by layer.
- Thermal Oxidation: This involves heating the substrate in an oxygen-rich environment to form an oxide layer.
- CVD methods involve chemical reactions to form the thin film. Common techniques include:
-
Physical Vapor Deposition (PVD):
-
Applications of Deposition Methods:
- Deposition methods are used in a wide range of applications, including:
- Electronic Packaging: Thin films are used to create conductive paths and insulating layers in electronic devices.
- Automotive Parts: Thin films can improve the durability and performance of automotive components.
- Medical Devices: Thin films are used to create biocompatible coatings and sensors.
- Holographic Displays: Thin films are essential for creating the optical layers needed for holographic displays.
- Deposition methods are used in a wide range of applications, including:
-
Advantages of Different Deposition Methods:
-
PVD:
- High Purity: PVD methods can produce very pure thin films with minimal contamination.
- Low Defects: The physical nature of PVD reduces the likelihood of defects in the thin film.
- Versatility: PVD can be used with a wide range of materials, including metals, ceramics, and polymers.
-
CVD:
- Uniformity: CVD can produce very uniform thin films, even on complex geometries.
- High-Quality Films: The chemical reactions in CVD can produce high-quality films with excellent adhesion and density.
- Scalability: CVD is suitable for large-scale production, making it ideal for industrial applications.
-
PVD:
-
Considerations for Choosing a Deposition Method:
- Material Properties: The choice of deposition method depends on the material properties required for the thin film, such as conductivity, transparency, or hardness.
- Substrate Compatibility: The substrate material and its properties (e.g., thermal stability, surface roughness) influence the choice of deposition method.
- Application Requirements: The specific application (e.g., electronic devices, medical implants) will dictate the necessary film properties and thus the appropriate deposition method.
- Cost and Scalability: The cost of the deposition method and its scalability for production are also important considerations.
-
Future Trends in Deposition Methods:
- Nanotechnology: As nanotechnology advances, deposition methods are being refined to create thinner, more precise films at the nanoscale.
- Hybrid Techniques: Combining PVD and CVD methods to leverage the advantages of both is an emerging trend.
- Sustainability: There is a growing focus on developing more environmentally friendly deposition methods that reduce waste and energy consumption.
In summary, deposition methods are critical for creating thin films with specific properties for various applications. The choice of method depends on the material, substrate, and application requirements, with PVD and CVD being the two primary categories. Each method has its advantages, and ongoing advancements in technology are driving the development of more efficient and sustainable deposition techniques.
Summary Table:
Category | Key Methods | Advantages | Applications |
---|---|---|---|
Physical Vapor Deposition (PVD) | Evaporation, Sputtering | High purity, low defects, versatile | Electronics, automotive, medical devices |
Chemical Vapor Deposition (CVD) | Chemical Bath Deposition, Electroplating, Molecular Beam Epitaxy, Thermal Oxidation | Uniformity, high-quality films, scalable | Electronic packaging, holographic displays, industrial coatings |
Need help selecting the right deposition method for your application? Contact our experts today!