Direct current (DC) magnetron sputtering is a physical vapor deposition (PVD) technique used to deposit thin films of materials onto substrates. It involves using a DC power source to generate a plasma in a vacuum or low-pressure environment. The plasma ions are accelerated toward a target material (cathode) by a magnetic field, causing the ejection of atoms from the target. These atoms then deposit onto a substrate, forming a thin film. This method is commonly used for metallic coatings and offers advantages such as high deposition rates, uniformity, and the ability to work with pure metals like Iron (Fe), Copper (Cu), and Nickel (Ni). The process is widely applied in industries requiring optical, electrical, or protective coatings.
Key Points Explained:
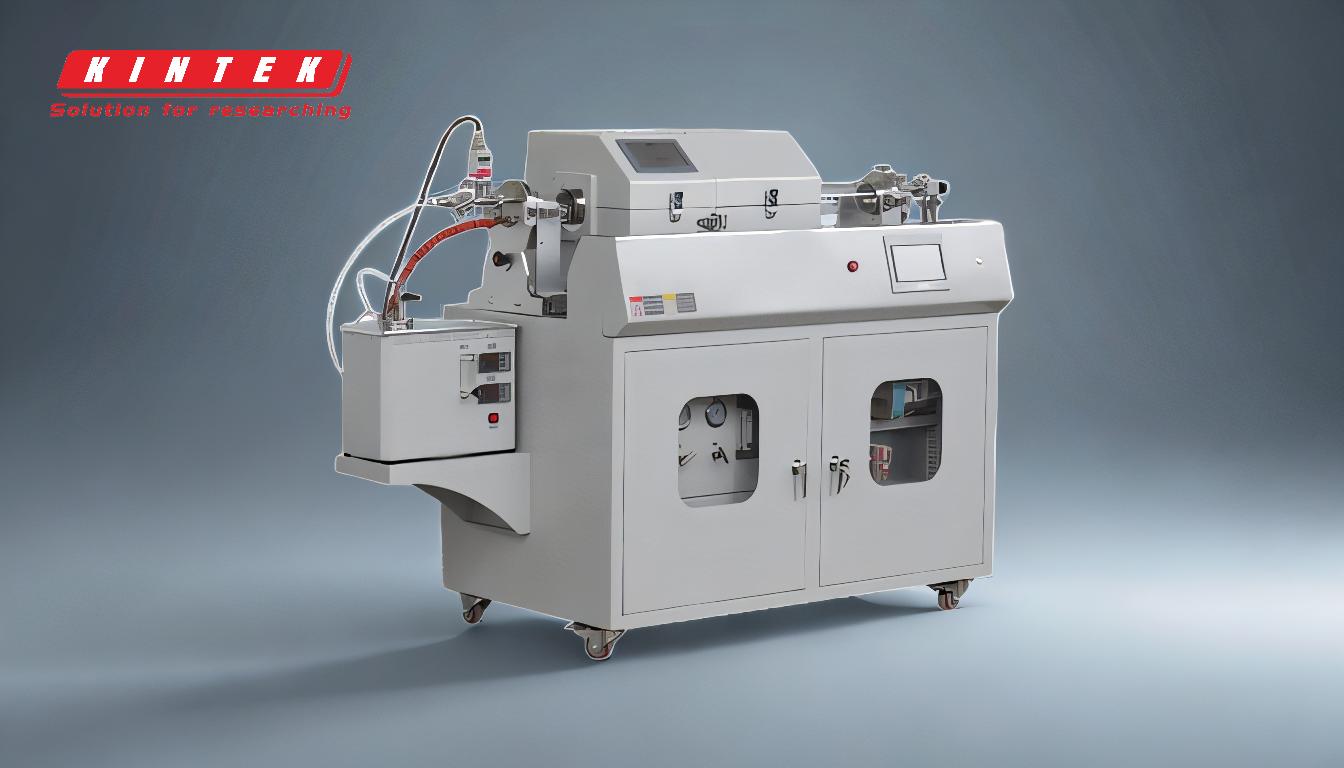
-
Basic Principle of DC Magnetron Sputtering:
- DC magnetron sputtering is a type of physical vapor deposition (PVD) where a DC power source is used to create a plasma in a vacuum or low-pressure environment.
- The plasma consists of positively charged ions that are accelerated toward a target material (cathode) due to the negative voltage applied to the target.
- The bombardment of ions on the target ejects atoms, which then travel to the substrate and form a thin film.
-
Role of the Magnetic Field:
- A magnetron generates a magnetic field that confines the plasma near the target surface, increasing the ion density and enhancing the sputtering process.
- The magnetic field traps secondary electrons near the target, increasing their collision frequency with gas ions and maintaining the plasma.
- This confinement leads to higher sputtering rates and improved uniformity in the deposited film.
-
Process Conditions:
- The process typically operates at chamber pressures ranging from 1 to 100 mTorr.
- The target material is usually a pure metal (e.g., Iron, Copper, Nickel) or a ceramic.
- The low-pressure environment ensures minimal contamination and allows for precise control over the deposition process.
-
Advantages of DC Magnetron Sputtering:
- High Deposition Rates: The magnetic field increases the efficiency of the sputtering process, leading to faster deposition.
- Uniform and Dense Films: The process produces films with excellent uniformity and density, making it suitable for high-quality coatings.
- Low Deposition Temperature: The technique can be performed at relatively low temperatures, making it compatible with temperature-sensitive substrates.
- Versatility: It can be used with a wide range of materials, including metals, ceramics, and insulators.
-
Applications:
- Optical Coatings: Used for anti-reflective, reflective, or protective coatings on lenses and mirrors.
- Electrical Coatings: Applied in the production of conductive layers for electronic devices and circuits.
- Protective Coatings: Used to enhance the durability and corrosion resistance of industrial components.
-
Comparison with Other Sputtering Techniques:
- Unlike RF (radio frequency) sputtering, which is used for insulating materials, DC magnetron sputtering is primarily used for conductive materials.
- It offers higher deposition rates compared to other PVD methods, such as thermal evaporation.
- The magnetic field in DC magnetron sputtering provides better control over the plasma, resulting in more efficient and uniform deposition.
-
Challenges and Limitations:
- Target Material Limitations: DC magnetron sputtering is less effective for insulating materials due to charge buildup on the target.
- Complexity of Equipment: The need for a vacuum environment and precise magnetic field control increases the complexity and cost of the equipment.
- Substrate Compatibility: While the process operates at low temperatures, some substrates may still require additional considerations to avoid damage.
By understanding these key points, a purchaser can evaluate whether DC magnetron sputtering is the right technique for their specific application, considering factors such as material compatibility, desired film properties, and production requirements.
Summary Table:
Aspect | Details |
---|---|
Basic Principle | Uses DC power to create plasma, ejecting target atoms for thin film deposition. |
Magnetic Field Role | Enhances plasma confinement, increasing sputtering rates and film uniformity. |
Process Conditions | Operates at 1–100 mTorr, uses pure metals or ceramics, and ensures low contamination. |
Advantages | High deposition rates, uniform films, low temperature, and material versatility. |
Applications | Optical coatings, electrical layers, and protective coatings for industries. |
Challenges | Limited for insulators, complex equipment, and substrate compatibility issues. |
Need a reliable DC magnetron sputtering solution for your project? Contact us today to learn more!