Electric Field Assisted Sintering Technology (FAST), also known as Spark Plasma Sintering (SPS), is an advanced sintering technique that utilizes a direct electric current to heat the mold and/or sample through Joule heating. This method enables rapid heating rates and short processing cycles, making it highly efficient. It enhances material properties such as oxidation resistance and wear resistance, particularly in tungsten carbide composites, and facilitates the creation of functionally graded materials. The technology leverages mechanisms like surface oxide removal, electromigration, and electroplasticity to improve particle bonding and densification. Over the past century, it has evolved significantly, with over 640 patents filed, and is now widely used for sintering refractory metals, conductive nitrides, and carbides. FAST/SPS is part of a broader category of electric current-assisted sintering technologies that have revolutionized powder sintering by reducing production times and achieving near-theoretical densities without the need for binders.
Key Points Explained:
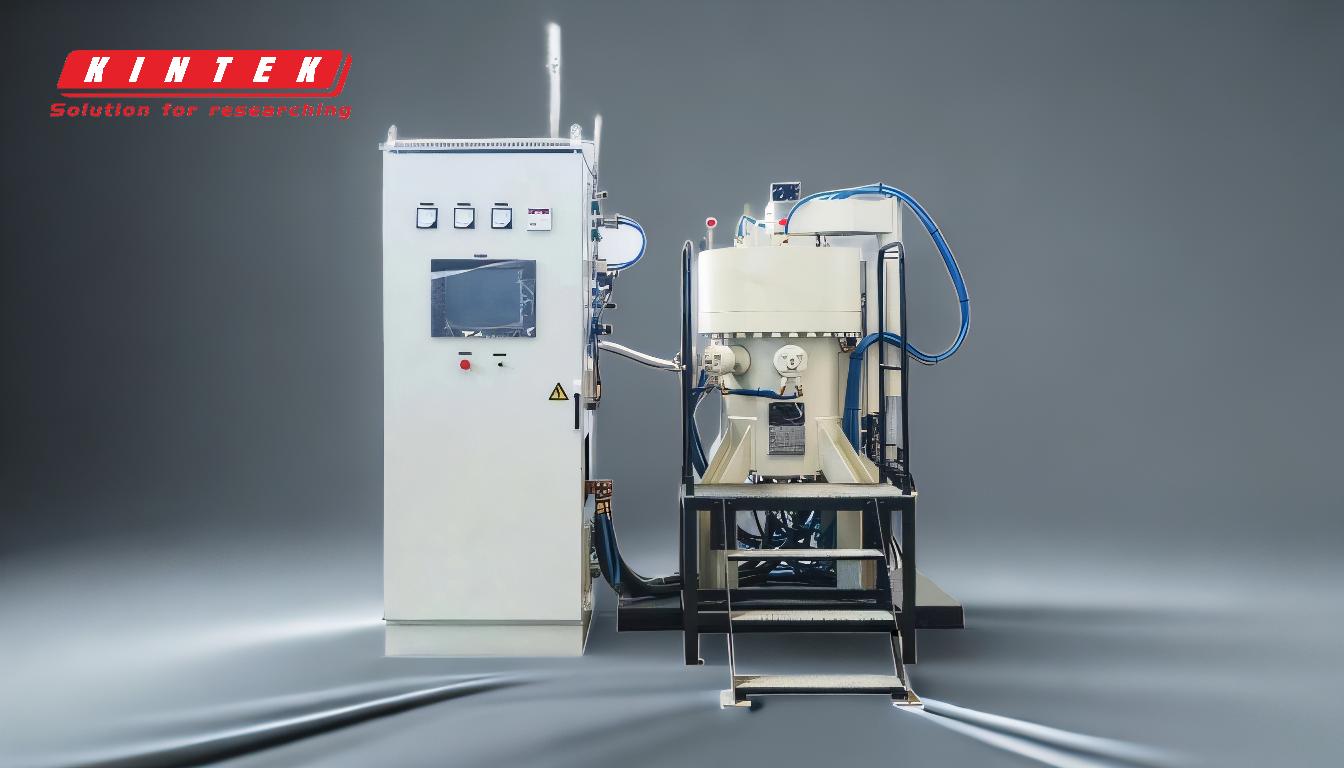
-
Definition and Mechanism of FAST/SPS:
- FAST/SPS uses a direct electric current to generate Joule heating, directly heating the mold and/or sample.
- This method allows for high heating rates and short processing cycles, making it more efficient than conventional sintering techniques.
-
Material Property Enhancements:
- FAST/SPS improves material properties such as oxidation resistance and wear resistance, particularly in tungsten carbide composites.
- It also enables the creation of functionally graded materials, which are materials with varying properties across their volume, useful in applications like soft-magnetic materials.
-
Historical Development and Patents:
- Electric current-assisted sintering was first patented in 1906 and has since evolved significantly.
- Over 640 related patents have been filed, indicating the technology's widespread adoption and continuous development.
-
Mechanisms of Electric Current in Sintering:
- Electric currents enhance sintering through mechanisms like surface oxide removal, electromigration, and electroplasticity.
- These mechanisms improve particle bonding and densification, making the sintering process more efficient and effective.
-
Comparison with Other Sintering Technologies:
- FAST/SPS is part of a broader category of electric current-assisted sintering technologies, which also include hot pressing, spark plasma sintering, and electro sinter forging.
- These technologies significantly reduce production times (from 15 minutes to microseconds) and achieve near-theoretical densities without the need for binders.
-
Advantages and Limitations:
- Advantages: Rapid heating rates, short processing times, enhanced material properties, and the ability to create functionally graded materials.
- Limitations: Primarily suitable for simple shapes and limited by the need for conductive materials.
-
Applications:
- FAST/SPS is particularly beneficial for sintering refractory metals, conductive nitrides, and carbides.
- It is also used in the development of advanced magnetic materials and other specialized applications where enhanced material properties are required.
-
Future Prospects:
- The continuous development of FAST/SPS and related technologies is expected to further enrich ceramic material sintering theory and improve sintering conditions.
- The technology's ability to achieve near-theoretical densities and rapid production times positions it as a key player in the future of material science and manufacturing.
By understanding these key points, equipment and consumable purchasers can better appreciate the value and potential applications of Electric Field Assisted Sintering Technology, making informed decisions about its adoption in their processes.
Summary Table:
Key Aspect | Details |
---|---|
Definition | Uses direct electric current for Joule heating, enabling rapid sintering. |
Material Enhancements | Improves oxidation/wear resistance, enables functionally graded materials. |
Historical Development | Over 640 patents filed since 1906, showcasing widespread adoption. |
Mechanisms | Surface oxide removal, electromigration, and electroplasticity. |
Advantages | Rapid heating, short cycles, enhanced properties, no binders needed. |
Limitations | Limited to simple shapes and conductive materials. |
Applications | Refractory metals, conductive nitrides, carbides, and advanced materials. |
Future Prospects | Expected to further advance ceramic sintering theory and applications. |
Ready to transform your material sintering process? Contact us today to learn more about FAST/SPS technology!