Floating catalyst chemical vapor deposition (FCCVD) is a specialized variant of the chemical vapor deposition (CVD) process, where a catalyst is introduced into the reaction chamber in a gaseous or vaporized form. Unlike traditional CVD methods that use solid or liquid catalysts, FCCVD relies on a floating catalyst that remains suspended in the gas phase during the deposition process. This technique is particularly useful for synthesizing high-quality nanomaterials, such as carbon nanotubes (CNTs) or graphene, with precise control over their structure and properties. The floating catalyst enables uniform distribution and efficient reaction kinetics, making FCCVD a preferred method for producing advanced materials with tailored characteristics.
Key Points Explained:
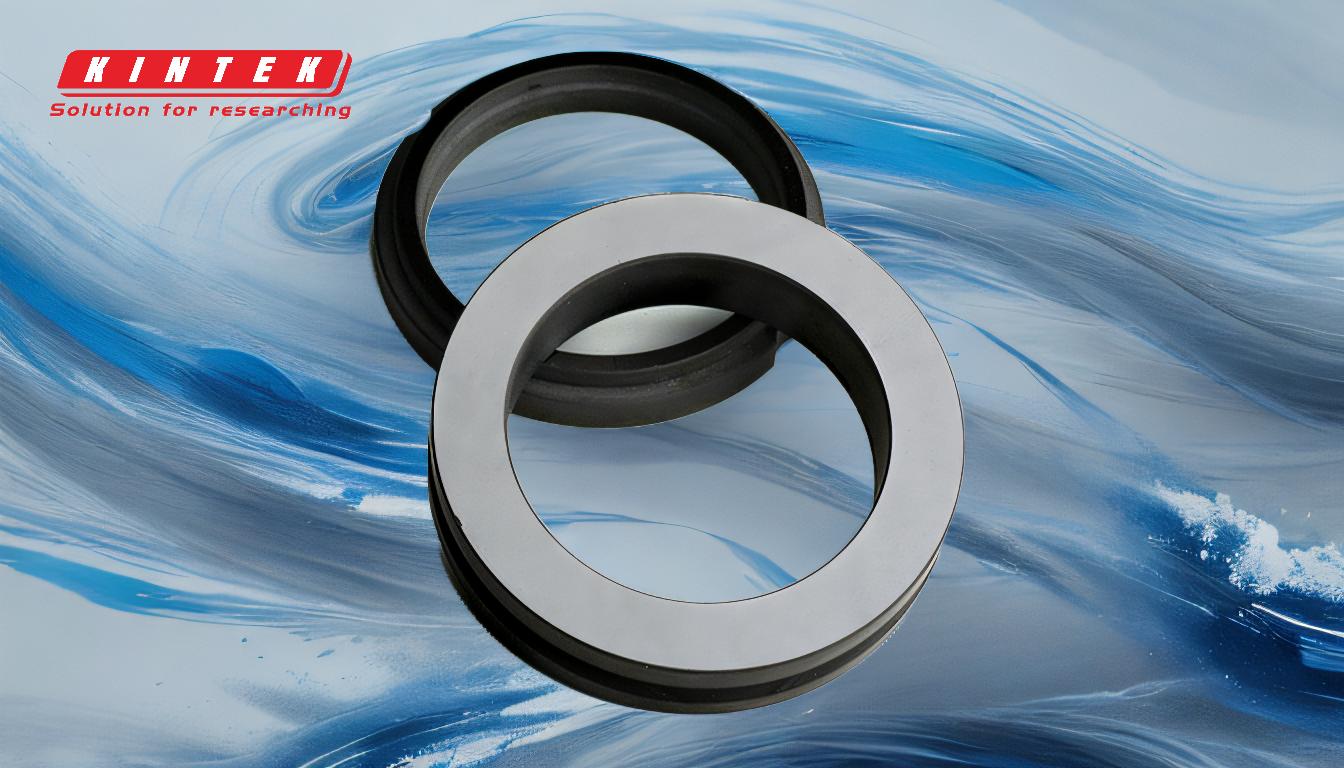
-
Definition of Floating Catalyst Chemical Vapor Deposition (FCCVD):
- FCCVD is a thin-film deposition technique where a catalyst is introduced in a gaseous or vaporized form, allowing it to remain suspended in the reaction chamber.
- This method is distinct from traditional CVD, which typically uses solid or liquid catalysts. The floating nature of the catalyst ensures better dispersion and interaction with the reacting species.
-
Mechanism of FCCVD:
- The process begins with the introduction of precursor gases and the catalyst into the reaction chamber.
- The catalyst, often in the form of a metal-organic compound, vaporizes and floats in the gas phase.
- The precursor gases decompose in the presence of heat, and the floating catalyst facilitates the formation of the desired material (e.g., carbon nanotubes or graphene) on the substrate.
-
Advantages of FCCVD:
- Uniform Deposition: The floating catalyst ensures even distribution, leading to uniform thin-film growth.
- High-Quality Materials: FCCVD is known for producing nanomaterials with exceptional purity and structural integrity.
- Scalability: This method is suitable for large-scale production due to its efficient reaction kinetics and continuous process flow.
-
Applications of FCCVD:
- Carbon Nanotubes (CNTs): FCCVD is widely used to synthesize CNTs with controlled diameter, length, and chirality.
- Graphene Production: The method is effective for growing high-quality graphene layers with minimal defects.
- Other Nanomaterials: FCCVD can also be applied to produce nanowires, nanorods, and other advanced materials.
-
Comparison with Other Deposition Techniques:
- Unlike physical vapor deposition (PVD), which relies on physical processes like sputtering, FCCVD involves chemical reactions facilitated by the floating catalyst.
- Compared to aerosol deposition, FCCVD does not require high-speed particle collisions, making it more suitable for delicate substrates.
- FCCVD offers better control over material properties than thermal vapor deposition, which is limited by the vapor pressure of the source material.
-
Challenges and Considerations:
- Catalyst Selection: Choosing the right catalyst is critical for achieving the desired material properties.
- Process Optimization: Parameters such as temperature, pressure, and gas flow rates must be carefully controlled to ensure consistent results.
- Cost: The use of metal-organic catalysts and specialized equipment can make FCCVD more expensive than some alternative methods.
In summary, floating catalyst chemical vapor deposition is a versatile and efficient technique for synthesizing high-quality nanomaterials. Its unique use of a floating catalyst enables precise control over material properties, making it a valuable tool in advanced material science and nanotechnology applications.
Summary Table:
Aspect | Details |
---|---|
Definition | Thin-film deposition using a gaseous or vaporized floating catalyst. |
Mechanism | Catalyst vaporizes, floats in gas phase, and facilitates material formation. |
Advantages | Uniform deposition, high-quality materials, scalability. |
Applications | Carbon nanotubes, graphene, nanowires, and other nanomaterials. |
Comparison | Superior to PVD, aerosol, and thermal vapor deposition methods. |
Challenges | Catalyst selection, process optimization, and cost considerations. |
Discover how FCCVD can revolutionize your nanomaterial synthesis—contact our experts today!