A furnace atmosphere refers to the gaseous environment inside a furnace during heating processes. It plays a critical role in material processing, as it can influence the chemical and physical properties of the materials being treated. A controlled atmosphere furnace is designed to maintain precise temperature and atmospheric conditions, ensuring optimal results for specific applications. These furnaces are widely used in laboratories, universities, and industrial settings for processes like sintering, heat treatment, and chemical analysis. The tightly sealed environment prevents external air infiltration, allowing for the creation of protective or reactive atmospheres, which are essential for achieving desired material properties.
Key Points Explained:
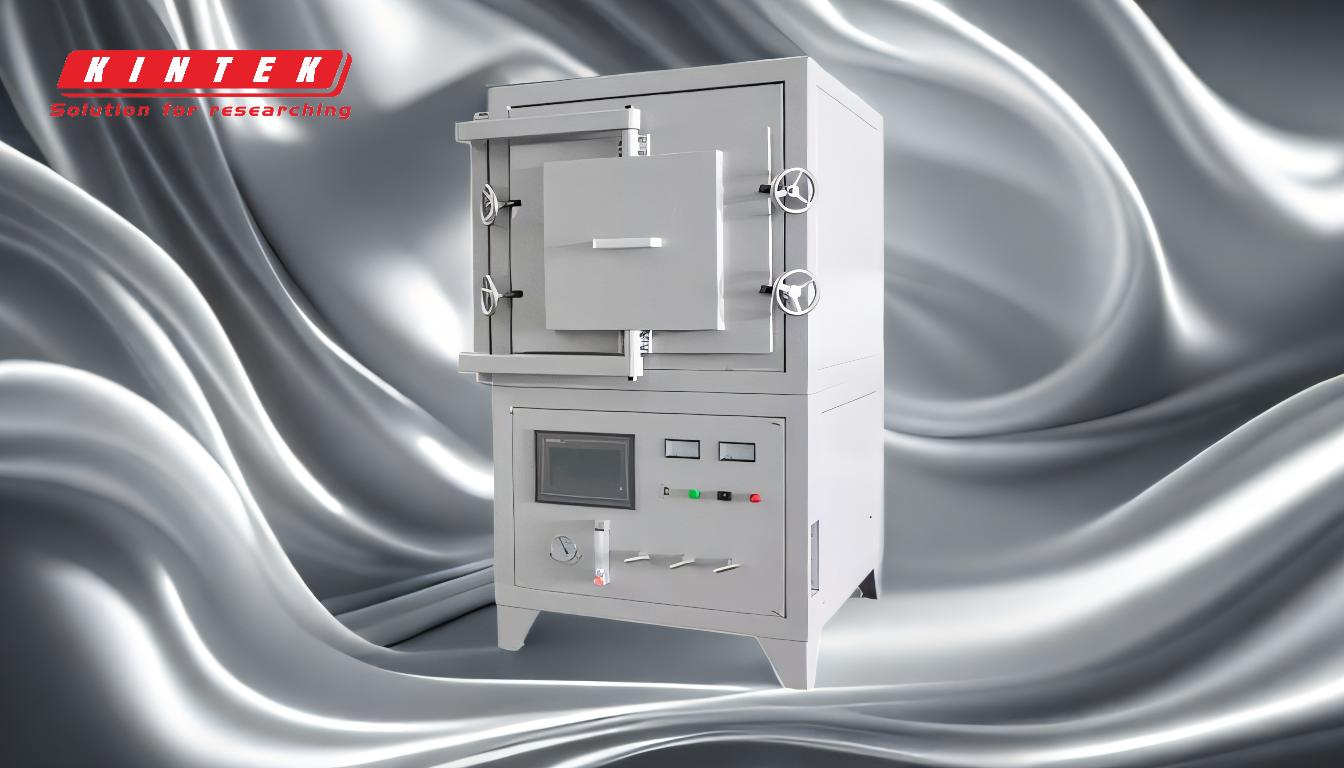
-
Definition of Furnace Atmosphere:
- The furnace atmosphere is the gaseous environment inside the furnace during heating. It can be inert, reactive, or protective, depending on the application.
- A controlled atmosphere furnace ensures precise control over this environment, which is critical for processes like sintering, heat treatment, and chemical analysis.
-
Importance of Controlled Atmosphere:
- A tightly sealed environment prevents external air from infiltrating the furnace, which could otherwise alter the chemical composition of the materials being processed.
- Controlled atmospheres are essential for achieving specific material properties, such as hardness, ductility, or corrosion resistance.
-
Applications of Controlled Atmosphere Furnaces:
- These furnaces are used in various settings, including laboratories, universities, and industrial facilities.
- Common applications include sintering of metals and ceramics, heat treatment of small steel parts, and chemical analysis.
-
Key Characteristics of Controlled Atmosphere Furnaces:
- Good Sealing: Ensures no external air enters the furnace, maintaining the desired atmosphere.
- Uniform Flow of Atmosphere: Provides consistent conditions throughout the furnace chamber.
- Suitable Heating Elements: Designed to withstand high temperatures and specific atmospheres.
- Safety Devices: Includes explosion protection and other safety features to handle reactive or explosive gases.
-
Advantages of Controlled Atmosphere Furnaces:
- Energy Efficiency: High efficiency and low energy consumption reduce operating costs.
- Versatility: Applicable to parts of all shapes and sizes.
- Precision: Accurate temperature controls and thermal homogeneity ensure consistent results.
- Safety: Equipped with safety devices to handle potentially hazardous atmospheres.
-
Types of Atmospheres:
- Protective Atmospheres: Prevent oxidation or other unwanted reactions during heating.
- Reactive Atmospheres: Facilitate specific chemical reactions to achieve desired material properties.
-
Safety Considerations:
- Handling and introducing gaseous atmospheres require careful attention, especially when dealing with explosive mixtures.
- Safety devices and explosion protection mechanisms are critical components of these furnaces.
-
Differentiated Finish:
- Controlled atmosphere furnaces can produce high-quality finishes on materials, which is essential for applications requiring precise surface properties.
By understanding the role of furnace atmospheres and the capabilities of a controlled atmosphere furnace, users can select the right equipment for their specific needs, ensuring optimal results in material processing and research.
Summary Table:
Aspect | Details |
---|---|
Definition | Gaseous environment inside a furnace during heating processes. |
Importance | Influences chemical and physical properties of materials. |
Applications | Sintering, heat treatment, chemical analysis in labs and industries. |
Key Characteristics | Good sealing, uniform atmosphere flow, suitable heating elements, safety. |
Advantages | Energy efficiency, versatility, precision, and safety. |
Types of Atmospheres | Protective (prevents oxidation) and reactive (facilitates reactions). |
Safety Considerations | Explosion protection and handling of hazardous gases. |
Discover how a controlled atmosphere furnace can enhance your material processing—contact us today!