A furnace retort is a specialized type of furnace used in various industrial and laboratory applications for processes that require controlled atmospheric conditions. It is designed to handle materials that need to be heated in environments where the atmosphere can be precisely regulated, such as in the absence of oxygen or in the presence of specific gases. Retort furnaces are commonly used in fields like metallurgy, ceramics, electronics, and chemical processing. They are versatile, offering features like low atmosphere usage, precise temperature control, and the ability to alter atmospheric conditions during a single firing cycle. The furnace can be electrically heated or use gas burners, and it can be constructed in horizontal or vertical configurations depending on the application. Its applications include powder roasting, ceramic sintering, high-temperature experiments, material treatment, and more.
Key Points Explained:
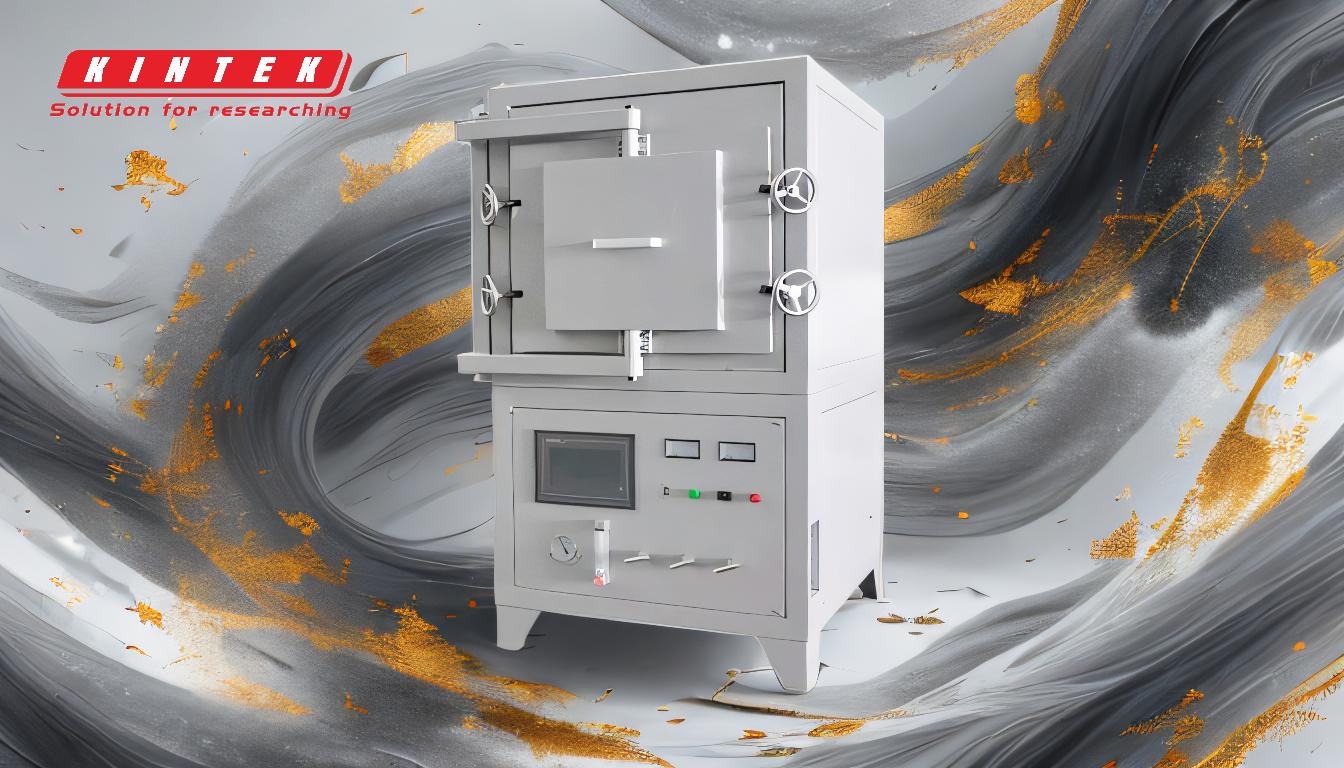
-
Definition and Purpose of a Retort Furnace:
- A retort furnace is a type of furnace designed for processes that require controlled atmospheric conditions. It is used to heat materials in environments where the atmosphere can be precisely regulated, such as in the absence of oxygen or in the presence of specific gases. This capability makes it ideal for applications like sintering, annealing, and chemical reactions.
-
Applications Across Industries:
- Retort furnaces are widely used in various industries, including:
- Ceramics: For sintering and glazing processes.
- Metallurgy: For heat treatment and brazing of metal components.
- Electronics: For the production of semiconductors and other electronic components.
- Chemical Industry: For high-temperature chemical reactions and material synthesis.
- Scientific Research: For experiments requiring precise temperature and atmospheric control.
- Retort furnaces are widely used in various industries, including:
-
Atmospheric Control:
- One of the key features of a retort furnace is its ability to control the atmosphere within the heating chamber. This is crucial for processes that require specific gas environments or the absence of oxygen to prevent oxidation or contamination. The furnace can be evacuated of air and filled with inert gases like nitrogen or argon.
-
Heating Mechanisms:
- Retort furnaces can be heated using:
- Electric Resistance Heaters: These provide precise temperature control and are commonly used in laboratory settings.
- Gas Burners: These are often used in industrial applications for their efficiency and ability to reach high temperatures quickly.
- Retort furnaces can be heated using:
-
Design Configurations:
- Retort furnaces can be built in two main configurations:
- Horizontal: Suitable for processes that require easy loading and unloading of materials.
- Vertical: Ideal for applications where space is limited or where gravity-assisted processes are needed.
- Retort furnaces can be built in two main configurations:
-
Advantages in Industrial Applications:
- Retort furnaces offer several benefits in industrial settings:
- Quicker Heating Times: Due to efficient heating mechanisms, these furnaces can reach desired temperatures faster.
- Improved Operating Conditions: The controlled atmosphere reduces the risk of contamination and improves the quality of the final product.
- Decreased Fuel Consumption: The efficient design and heating mechanisms lead to lower energy usage, making the process more cost-effective.
- Retort furnaces offer several benefits in industrial settings:
-
Specific Use Cases:
- Furnace Brazing: A semi-automated process where metal components are joined using a lower melting filler metal. The retort furnace is used to heat the assembly to the brazing temperature in a controlled atmosphere, ensuring a strong and clean joint.
- High-Temperature Experiments: Retort furnaces are used in scientific research for experiments that require precise temperature and atmospheric control, such as material synthesis and chemical reactions.
In summary, a retort furnace is a versatile and essential tool in many industrial and laboratory settings, offering precise control over both temperature and atmospheric conditions. Its ability to handle a wide range of materials and processes makes it a valuable asset in fields ranging from metallurgy to scientific research.
Summary Table:
Feature | Details |
---|---|
Definition | A furnace designed for controlled atmospheric heating processes. |
Applications | Ceramics, metallurgy, electronics, chemical processing, scientific research. |
Atmospheric Control | Precise regulation of gases like nitrogen or argon, or absence of oxygen. |
Heating Mechanisms | Electric resistance heaters or gas burners. |
Design Configurations | Horizontal or vertical, depending on application needs. |
Advantages | Quick heating, improved product quality, reduced fuel consumption. |
Specific Use Cases | Furnace brazing, high-temperature experiments, material synthesis. |
Discover how a retort furnace can optimize your processes—contact our experts today!