Sintering is a process where particles are fused together using heat, but without reaching the material's melting point. High-temperature sintering, specifically, involves heating materials to very high temperatures, typically ranging from 1200°C to 1400°C, to achieve the desired properties such as reduced porosity, increased density, and improved strength. This process is widely used in industries like dentistry, 3D printing, and metal fabrication. Temperature control is critical in sintering, as it influences diffusion mechanisms and ultimately affects the quality of the final product. A high temperature furnace is essential for achieving the precise temperatures required for effective sintering.
Key Points Explained:
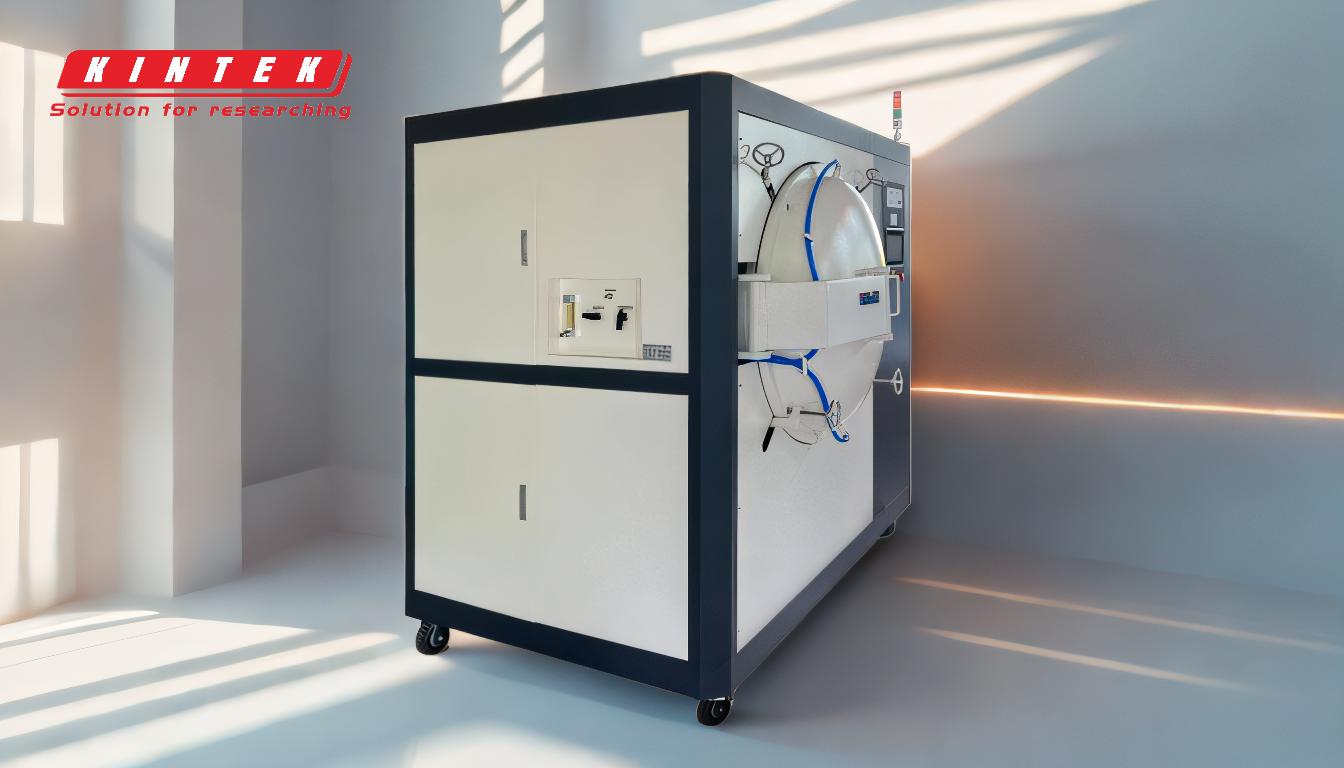
-
Definition of High-Temperature Sintering:
- High-temperature sintering is a process where materials are heated to extremely high temperatures, typically between 1200°C and 1400°C, to fuse particles together without melting them. This process is essential for creating strong, dense, and durable materials.
-
Role of Temperature in Sintering:
- Temperature is crucial in sintering because it must be high enough to allow atoms to diffuse across particle boundaries and fuse particles together. However, it must remain below the material's melting point to avoid liquefaction. This balance ensures the material retains its structural integrity while achieving the desired properties.
-
Applications of High-Temperature Sintering:
- Dental Applications: In dentistry, sintering is used to create strong and durable dental prosthetics. The process typically requires temperatures between 1200°C and 1400°C.
- 3D Printing: Sintering is used in 3D printing to form custom metal shapes. This method saves energy and allows for greater consistency and control.
- Metal Fabrication: Sintering is particularly useful for joining metal particles, especially those with high melting points, as it does not require reaching melting temperatures.
-
Effects of Temperature and Time on Sintering:
- High Temperatures and Long Heating Times: These can reduce product properties and even lead to defects like scorching.
- Low Temperatures or Inadequate Heating Times: These may result in degraded properties due to incomplete sintering.
- Proper control of temperature and time is essential to achieve the desired porosity, density, strength, and hardness of the sintered body.
-
Importance of Temperature Control:
- Temperature control is critical because grain boundary diffusion and bulk diffusion are heavily dependent on temperature. Factors such as particle size, material distribution, composition, and the sintering environment also play significant roles in the sintering process. Precise temperature control ensures the material achieves the desired properties without defects.
-
Use of High-Temperature Furnaces:
- A high temperature furnace is essential for achieving the precise temperatures required for high-temperature sintering. These furnaces are designed to maintain consistent temperatures and provide the necessary environment for effective sintering.
In summary, high-temperature sintering is a critical process in various industries, requiring precise temperature control to achieve the desired material properties. The use of a high temperature furnace is indispensable for ensuring the success of this process.
Summary Table:
Key Aspect | Details |
---|---|
Definition | Heating materials to 1200°C–1400°C to fuse particles without melting them. |
Key Benefits | Reduced porosity, increased density, and improved strength. |
Applications | Dentistry, 3D printing, and metal fabrication. |
Temperature Control | Critical for avoiding defects and achieving desired properties. |
Equipment Needed | High-temperature furnace for precise and consistent heating. |
Learn how high-temperature sintering can enhance your materials—contact us today for expert guidance!