High-temperature sintering is a process used to enhance the properties of materials by heating them to temperatures just below their melting points, allowing particles to bond through atomic diffusion. This method significantly improves mechanical properties such as tensile strength, bending fatigue strength, and impact energy. However, it requires specialized equipment, such as high-temperature furnaces, and careful planning to manage potential shrinkage and costs. The process can be performed using various techniques, including hot pressing sintering, which offers advantages like reduced deformation resistance, shorter sintering times, and the ability to produce complex shapes with high precision. Continuous high-temperature sintering furnaces ensure consistent conditions and prevent oxidation, making them ideal for high-throughput production. Overall, high-temperature sintering is a versatile and effective method for producing high-performance materials, though it demands significant investment and expertise.
Key Points Explained:
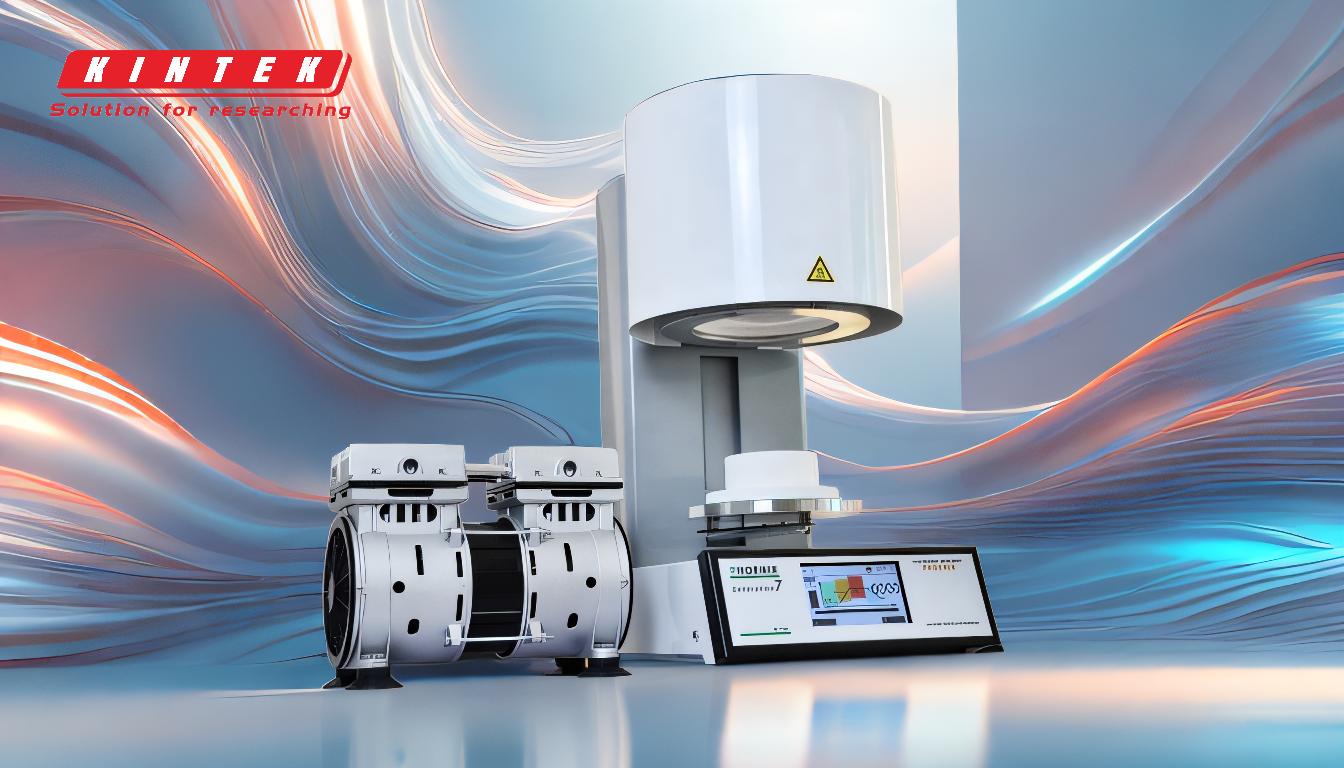
-
Definition and Purpose of High-Temperature Sintering:
- High-temperature sintering involves heating powdered materials to just below their melting points, enabling particles to bond through atomic diffusion.
- The primary goal is to enhance material properties, such as increasing tensile strength by 30%, bending fatigue strength by 15%, and impact energy by 50%.
-
Benefits of High-Temperature Sintering:
- Improved Mechanical Properties: The process significantly boosts the mechanical strength and durability of materials.
- Enhanced Material Density: High-temperature sintering produces materials with near-theoretical density, fine grain structures, and excellent mechanical and electrical properties.
- Complex Shape Production: It allows for the creation of complex shapes and accurate sizes, which are difficult to achieve with other methods.
-
Challenges and Considerations:
- Cost: The process is more expensive due to the need for specialized furnaces and equipment.
- Shrinkage: Parts may shrink more than expected, requiring careful planning and design adjustments by manufacturers.
- Expertise Required: High-temperature sintering demands a high level of expertise to manage the process effectively and avoid defects.
-
Types of Sintering Methods:
- Hot Pressing Sintering: Combines heating and pressurization to reduce deformation resistance, lower sintering temperatures, and shorten sintering times. It produces high-density materials with excellent properties.
- Continuous High-Temperature Sintering: Ensures consistent conditions for every part, preventing oxidation and guaranteeing repeatability and throughput.
- Other Methods: Includes hydrogen protection, vacuum sintering, hot isostatic pressing, and more, each with specific advantages depending on the material and desired outcome.
-
Advantages of Specific Sintering Techniques:
- Hot Pressing Sintering: Offers lower deformation resistance, simultaneous heating and pressurization, and the ability to produce complex shapes with high precision.
- Continuous High-Temperature Sintering: Provides guaranteed throughput, repeatability, and protection against oxidation, making it ideal for high-volume production.
- Hot Isostatic Pressing: Applies high pressure and temperature to form and fuse powder particles, resulting in materials with superior density and mechanical properties.
-
Applications and Material Types:
- Ceramics: High-temperature sintering is particularly effective for producing ceramic materials with complex and porous structures, enhancing their strength and performance.
- Metals and Alloys: The process is also used for metals and alloys to improve their mechanical properties and durability.
- Advanced Materials: High-temperature sintering is crucial for manufacturing advanced materials used in aerospace, automotive, and electronics industries.
-
Technological Advancements:
- IT Integration: Modern sintering processes often incorporate IT technology to control the densification process and material quality more effectively.
- Energy Efficiency: Advances in sintering technology have led to improved temperature field uniformity and reduced energy consumption.
- Large-Scale Production: High-temperature sintering can now be used to prepare large-diameter materials, expanding its applicability in various industries.
-
Comparison with Other Sintering Methods:
- Solid-State Sintering: Involves heating powdered material below its melting point to bond particles through atomic diffusion.
- Liquid Phase Sintering: Uses a solvent liquid to induce low porosity and bonding, which is then driven off by heating.
- Reactive Sintering: Involves a chemical reaction of powder particles during heating.
- Microwave Sintering: Utilizes microwaves for faster integration in ceramics.
- Spark Plasma Sintering: Uses electric current and physical compression to achieve rapid sintering.
In summary, high-temperature sintering is a powerful method for enhancing material properties, offering significant benefits in terms of strength, density, and complex shape production. However, it requires careful management of costs, shrinkage, and expertise to achieve optimal results. The process is versatile, with various techniques available to suit different materials and applications, making it a cornerstone of modern materials science and manufacturing.
Summary Table:
Key Aspect | Details |
---|---|
Purpose | Enhances material properties through atomic diffusion at high temperatures. |
Benefits | - Increased tensile strength (30%) |
- Enhanced bending fatigue strength (15%)
- Improved impact energy (50%) | | Challenges | - High costs
- Potential shrinkage
- Requires expertise and specialized equipment | | Sintering Methods | - Hot pressing sintering
- Continuous high-temperature sintering
- Hot isostatic pressing | | Applications | Ceramics, metals, alloys, aerospace, automotive, and electronics industries |
Unlock the potential of high-temperature sintering for your materials—contact our experts today!