HIP (Hot Isostatic Pressing) treatment for metals is a specialized process that enhances material properties by subjecting them to high temperatures and uniform isostatic pressure. This process eliminates internal defects such as voids and porosity, achieving near-theoretical density and improving mechanical properties like strength, durability, and fatigue life. HIP is particularly effective in homogenizing castings, enhancing weldability, and producing materials with consistent microstructures. It is widely used as a high-performance alternative to traditional methods like forging, casting, and machining, making it suitable for demanding applications in industries such as aerospace, automotive, and medical devices.
Key Points Explained:
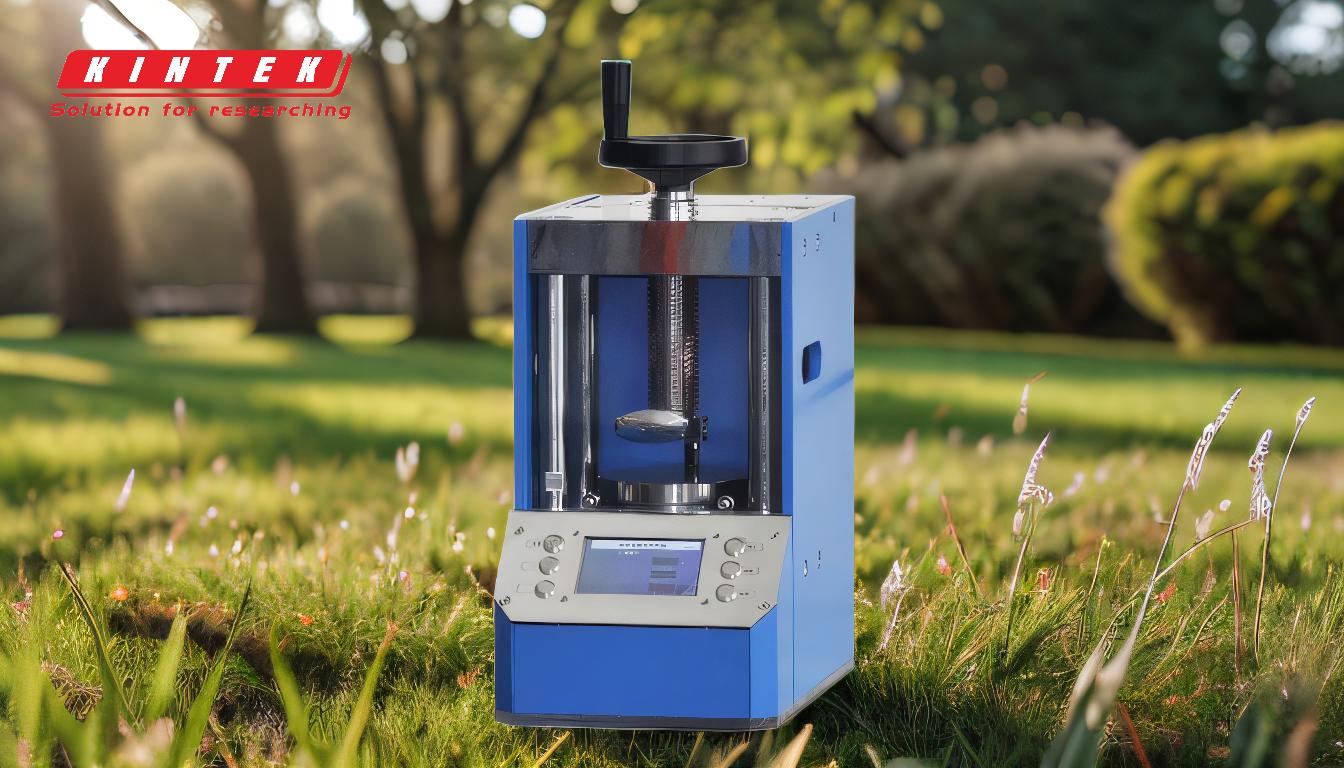
-
What is HIP Treatment?
- HIP (Hot Isostatic Pressing) is a process that applies uniform isostatic pressure and high temperature to metal components. This combination causes voids and porosity to collapse, while surfaces diffusion bond, resulting in a denser and more homogeneous material structure.
-
How HIP Works
- The process involves placing the metal in a high-pressure vessel filled with inert gas (usually argon). The material is then heated to temperatures typically between 900°C and 1200°C, while pressures of up to 200 MPa are applied. This environment allows for the elimination of internal defects and the creation of a uniform microstructure.
-
Benefits of HIP Treatment
- Improved Mechanical Properties: HIP enhances strength, durability, and fatigue life by eliminating defects and achieving near-theoretical density.
- Enhanced Reliability: The process produces materials with consistent properties, reducing the risk of failure in critical applications.
- Better Weldability: HIP-treated materials often exhibit improved weldability, making them easier to join in complex assemblies.
- Homogenization: It eliminates segregation in castings, resulting in a more uniform material structure.
-
Applications of HIP
- HIP is widely used in industries requiring high-performance materials, such as aerospace, automotive, and medical devices. It is particularly beneficial for components subjected to extreme stress or harsh environments, such as turbine blades, engine parts, and surgical implants.
-
Comparison to Traditional Methods
- HIP offers advantages over conventional processes like forging, casting, and machining. It provides better material properties, reduces the need for secondary processing, and can produce complex geometries with minimal waste.
-
Role in Powder Metallurgy
- In powder metallurgy, HIP compresses metal powders at high temperatures and pressures, creating a solid product with minimal impurities. This process is ideal for producing materials with high strength, conductivity, and translucency.
-
Long-Term Impact
- HIP-treated materials exhibit enhanced resistance to corrosion, improved fatigue life (1.5–8 times longer), and greater overall reliability. These improvements make HIP an essential process for advanced manufacturing and high-performance applications.
In summary, HIP treatment is a transformative process that significantly enhances the properties of metals, making them stronger, more durable, and better suited for demanding applications. Its ability to eliminate defects and produce consistent, high-quality materials has made it a preferred choice in various industries.
Summary Table:
Aspect | Details |
---|---|
Process | Applies uniform isostatic pressure and high temperature (900°C–1200°C). |
Key Benefits | Eliminates voids, improves strength, enhances weldability, homogenizes castings. |
Applications | Aerospace, automotive, medical devices (e.g., turbine blades, implants). |
Advantages Over Traditional Methods | Better material properties, reduced secondary processing, minimal waste. |
Long-Term Impact | Improved fatigue life (1.5–8x), corrosion resistance, and overall reliability. |
Unlock the full potential of your metal components with HIP treatment—contact our experts today!