Hot Isostatic Pressing (HIP) and Cold Isostatic Pressing (CIP) are advanced manufacturing techniques used to consolidate materials, improve their density, and enhance their mechanical properties. HIP involves applying high temperature and pressure simultaneously, while CIP operates at room temperature or slightly above, using liquid as the pressure medium. Both methods are widely used in industries requiring high-performance materials, such as aerospace, medical, and energy sectors. HIP is ideal for densification, diffusion bonding, and powder metallurgy, whereas CIP is suitable for forming large, complex parts and consolidating ceramic powders or refractory materials.
Key Points Explained:
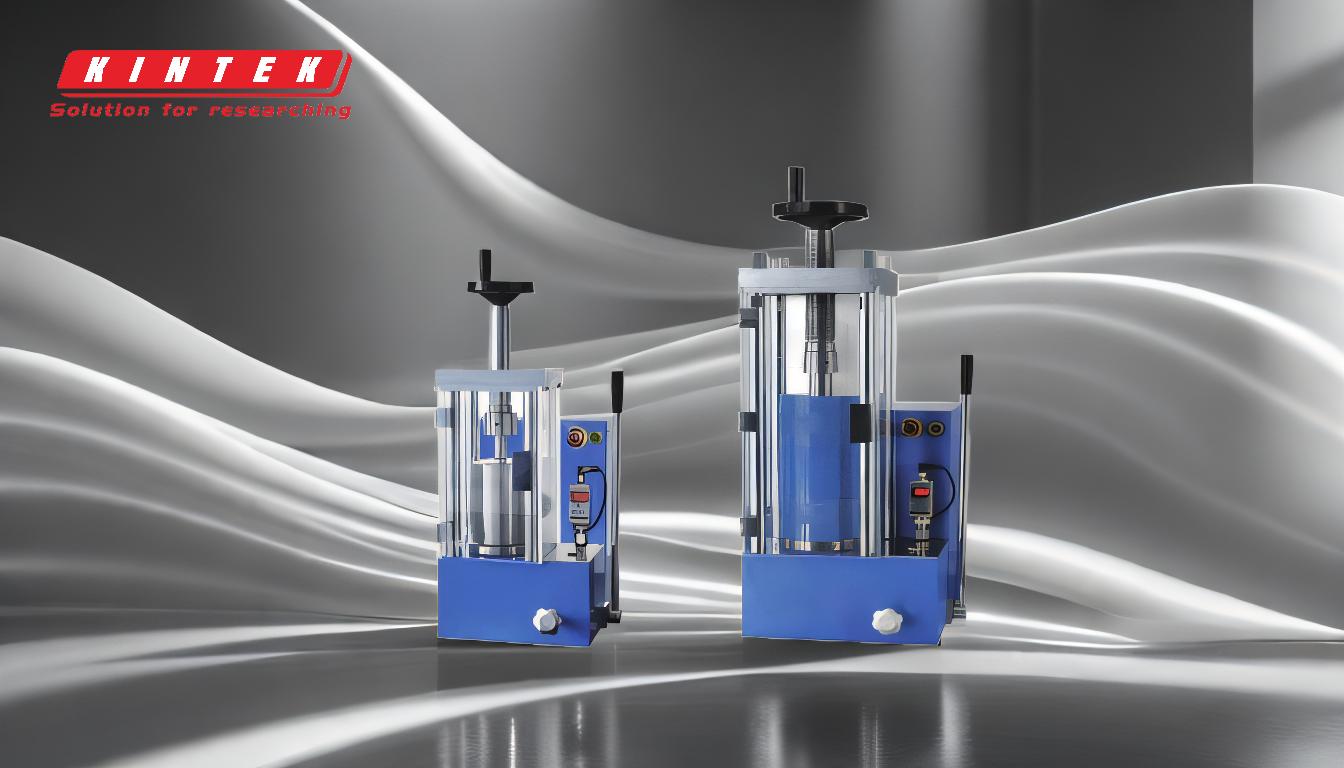
-
Cold Isostatic Pressing (CIP):
- Process Overview: CIP applies uniform pressure to powder materials at room temperature or slightly higher (<93°C) using a liquid medium like water, oil, or glycol mixtures. The pressure typically ranges from 100 to 630 MPa.
-
Applications:
- Used for forming large and complex parts that are difficult to press in uniaxial presses.
- Commonly employed in consolidating ceramic powders, graphite, refractory materials, and advanced ceramics like silicon nitride and silicon carbide.
- Essential in producing wear-resistant tools, metal-forming tools, and electrical insulators.
- Applied in solid-state battery production, such as preparing garnet-based composite solid electrolyte membranes and all-solid-state batteries.
-
Advantages:
- No heating devices are required, making it cost-effective.
- Suitable for materials that do not require high precision in the sintered state.
- Can produce "raw" parts with sufficient strength for handling and further processing.
-
Hot Isostatic Pressing (HIP):
- Process Overview: HIP combines high temperature and pressure to densify materials, improve their mechanical properties, and eliminate internal defects. It is typically used for castings, powder metallurgy products, and diffusion bonding.
-
Applications:
- Densification of castings to eliminate porosity and improve strength.
- Diffusion bonding for joining dissimilar materials or complex geometries.
- Powder metallurgy for producing high-performance alloys and ceramic products.
- Used in industries like aerospace, medical implants, and energy for manufacturing components with superior mechanical properties.
-
Advantages:
- Enhances material density and mechanical properties.
- Reduces internal defects like porosity, improving fatigue resistance.
- Enables the production of complex shapes and high-performance materials.
-
Key Differences Between CIP and HIP:
- Temperature: CIP operates at room temperature or slightly above, while HIP requires high temperatures.
- Pressure Medium: CIP uses liquid media like water or oil, whereas HIP often uses inert gases like argon.
- Applications: CIP is ideal for forming raw parts and consolidating powders, while HIP is used for densification, diffusion bonding, and producing high-performance alloys.
- Material Suitability: CIP is suitable for ceramics, graphite, and refractory materials, while HIP is used for metals, alloys, and advanced ceramics.
-
Industrial Significance:
- Both CIP and HIP are critical in producing materials with enhanced properties, such as high strength, wear resistance, and thermal stability.
- They enable the manufacturing of components that are difficult or impossible to produce using traditional methods like casting.
- Applications span across industries, including aerospace (turbine blades), medical (implants), and energy (solid-state batteries).
-
Future Trends:
- Increasing use of CIP in solid-state battery production, particularly for preparing ultra-thin electrolyte membranes.
- Growing adoption of HIP for additive manufacturing (3D printing) to improve the density and mechanical properties of printed parts.
- Development of hybrid processes combining CIP and HIP for advanced material manufacturing.
In summary, CIP and HIP are complementary technologies that address different manufacturing challenges. CIP is ideal for forming large, complex parts at lower costs, while HIP excels in producing high-density, defect-free materials for demanding applications. Together, they play a pivotal role in advancing material science and industrial manufacturing.
Summary Table:
Aspect | Cold Isostatic Pressing (CIP) | Hot Isostatic Pressing (HIP) |
---|---|---|
Temperature | Room temperature or slightly above (<93°C) | High temperature |
Pressure Medium | Liquid (water, oil, glycol mixtures) | Inert gas (argon) |
Applications | Forming large, complex parts; consolidating ceramic powders, refractory materials, solid-state batteries | Densification, diffusion bonding, powder metallurgy, high-performance alloys, aerospace, medical |
Material Suitability | Ceramics, graphite, refractory materials | Metals, alloys, advanced ceramics |
Advantages | Cost-effective, no heating required, suitable for raw parts | Enhances density, reduces defects, produces high-performance materials |
Discover how CIP and HIP can revolutionize your material manufacturing process—contact our experts today!