Hot press molding is a manufacturing process that combines compaction and sintering of materials, typically powders, into a single step. This method is widely used in powder metallurgy and composite material production. It involves applying both high pressure and elevated temperatures to a material within a mold or die, allowing the particles to bond and form a solid, dense structure without fully melting. The process is efficient and produces high-quality parts with excellent mechanical properties. A hot press machine is the key equipment used in this process, enabling precise control over temperature and pressure.
Key Points Explained:
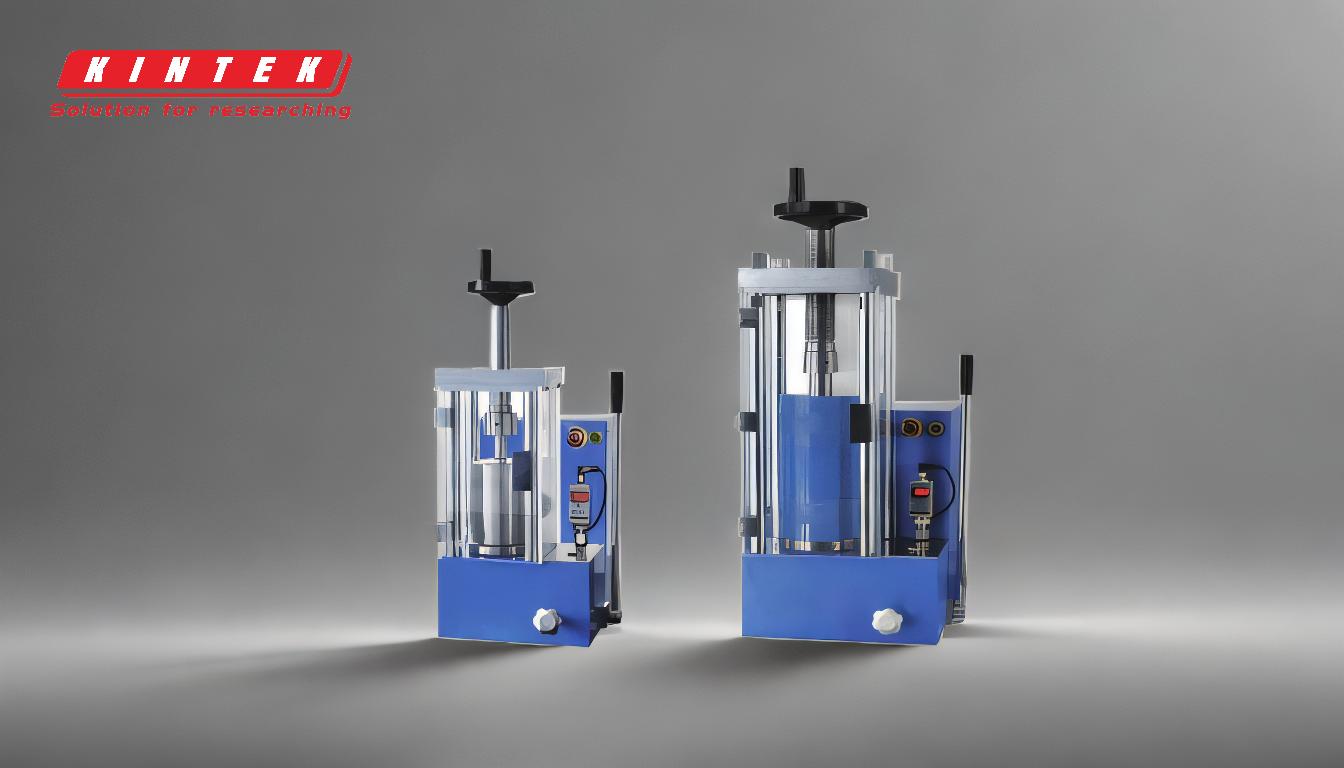
-
Combination of Compaction and Sintering:
- Hot press molding integrates the compaction and sintering stages into a single process. Compaction involves pressing powdered materials into a specific shape, while sintering uses heat to bond the particles together. By combining these steps, the process becomes more efficient and reduces the risk of defects.
-
Formation of the Green Part:
- The initial step involves creating a "green part," which is a loosely compacted mass of individual metal or composite particles. This part is formed within a die or mold under pressure, giving it the desired shape before sintering.
-
Application of Heat and Pressure:
- The green part is subjected to elevated temperatures, just below the material's melting point, and high pressure simultaneously. This dual application ensures that the particles bond effectively without melting, resulting in a dense and strong final product.
-
Necking and Sintering:
- At high temperatures, the particles undergo a process called "necking," where they begin to fuse at contact points. This is followed by sintering, where the particles fully bond, creating a solid structure with minimal porosity.
-
Advantages of Hot Press Molding:
- Efficiency: Combining compaction and sintering reduces production time and energy consumption.
- High Density: The process produces parts with high density and excellent mechanical properties.
- Versatility: Suitable for a wide range of materials, including metals, ceramics, and composites.
-
Role of the Hot Press Machine:
- A hot press machine is essential for this process. It provides precise control over temperature and pressure, ensuring consistent and high-quality results. The machine typically consists of a heated platen, a hydraulic or mechanical press, and a mold or die.
-
Applications:
- Hot press molding is used in various industries, including aerospace, automotive, and electronics, to produce components such as gears, bearings, and structural parts. It is also employed in the manufacturing of advanced materials like carbon fiber composites.
By understanding these key points, purchasers of equipment and consumables can better evaluate the suitability of hot press molding for their specific needs and ensure they invest in the right hot press machine for their applications.
Summary Table:
Key Aspect | Description |
---|---|
Process | Combines compaction and sintering into a single step. |
Green Part Formation | Loosely compacted mass of particles shaped under pressure. |
Heat and Pressure | Applied simultaneously to bond particles without melting. |
Necking and Sintering | Particles fuse at contact points, creating a solid, dense structure. |
Advantages | High efficiency, high-density parts, and material versatility. |
Hot Press Machine Role | Ensures precise temperature and pressure control for consistent results. |
Applications | Aerospace, automotive, electronics, and advanced materials like carbon fiber. |
Ready to enhance your production with hot press molding? Contact us today to find the perfect solution!