Hot press sintering is a specialized manufacturing process that combines heat and pressure to compact and form solid materials, particularly those with high melting points, without reaching their liquefaction temperature. This technique is widely used in powder metallurgy and ceramic manufacturing to produce dense, strong, and durable components. The process involves blending fine powdered materials, pressing them into a desired shape, and then applying heat and unidirectional pressure to bond the particles. While it offers advantages such as improved material properties and energy efficiency, it also has limitations, including shape constraints and potential uneven pressure distribution, which can lead to anisotropic properties in the final product.
Key Points Explained:
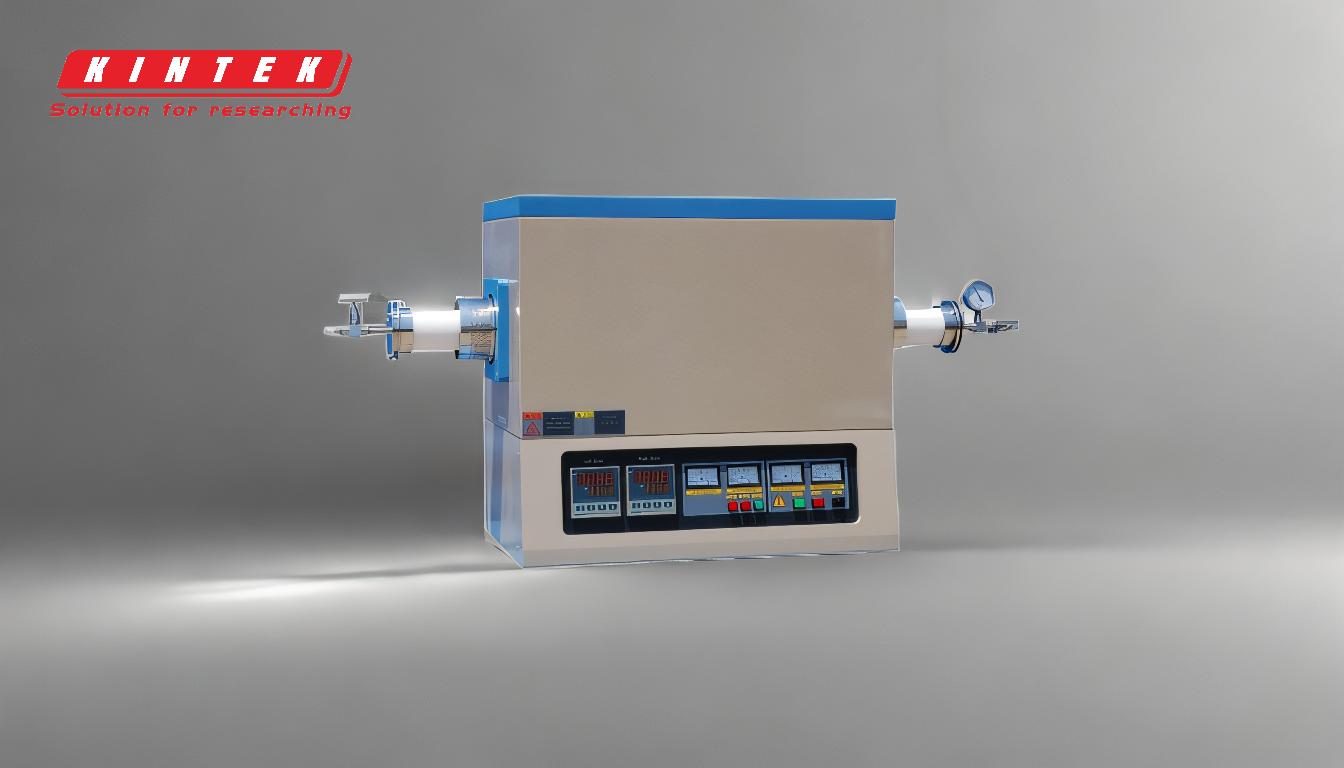
-
Definition and Purpose of Hot Press Sintering:
- Hot press sintering is a process that applies both heat and pressure to compact powdered materials into a solid mass. Unlike traditional sintering, which primarily relies on heat, this method uses unidirectional pressure to enhance particle bonding and material density.
- It is particularly useful for materials with high melting points, such as tungsten and molybdenum, which are difficult to process using conventional melting techniques. This method allows for the creation of strong, durable, and high-performance components.
-
Steps Involved in Hot Press Sintering:
- Blending: Fine powdered materials are mixed to ensure a uniform composition.
- Compaction: The blended powder is pressed into a desired shape using a mold. This step is crucial for achieving the initial density and shape of the product.
- Sintering: The compacted material is subjected to high heat and pressure in a controlled environment. The heat allows atoms to diffuse across particle boundaries, while the pressure ensures tighter bonding and reduced porosity.
-
Advantages of Hot Press Sintering:
- Improved Material Properties: The combination of heat and pressure results in a denser, stronger, and more durable final product.
- Energy Efficiency: Since the material does not need to reach its melting point, the process consumes less energy compared to traditional melting techniques.
- Precision and Control: The process allows for greater consistency and control over the final product's properties, making it ideal for high-performance applications.
-
Limitations of Hot Press Sintering:
- Shape and Size Constraints: The process is typically limited to producing cylindrical or ring-shaped products due to the unidirectional nature of the pressure applied.
- Uneven Pressure Distribution: The unidirectional pressure can lead to uneven distribution within the billet, causing anisotropy in the microstructure and mechanical properties of the final product. This is particularly problematic for materials with non-equiaxial crystal structures.
-
Applications of Hot Press Sintering:
- Powder Metallurgy: Used to create complex metal parts with high strength and durability, such as gears, bearings, and cutting tools.
- Ceramic Manufacturing: Ideal for producing high-performance ceramics used in industries like aerospace, electronics, and medical devices.
- Additive Manufacturing: Can be integrated with 3D printing technologies to create custom metal shapes with precise properties.
-
Role of the Hot Press Machine:
- The hot press machine is a critical component in this process, providing the necessary heat and pressure to achieve sintering. It consists of a heating element, a press mechanism, and a mold to shape the material. The machine's design and capabilities directly influence the quality and properties of the sintered product.
In summary, hot press sintering is a versatile and efficient manufacturing process that leverages heat and pressure to create high-performance materials. While it has some limitations, its advantages make it a valuable technique in industries requiring strong, durable, and precisely engineered components.
Summary Table:
Aspect | Details |
---|---|
Definition | Combines heat and pressure to compact powdered materials into solid forms. |
Key Steps | Blending, Compaction, Sintering |
Advantages | Improved material properties, energy efficiency, precision, and control. |
Limitations | Shape constraints, uneven pressure distribution, anisotropic properties. |
Applications | Powder metallurgy, ceramic manufacturing, additive manufacturing. |
Role of Hot Press Machine | Provides heat and pressure for sintering, influencing product quality. |
Learn how hot press sintering can enhance your manufacturing process—contact our experts today!