Induction annealing is a specialized heat treatment process that uses induction heating to selectively soften specific areas of a metal part. This process increases the material's ductility and reduces its hardness by reducing dislocations in its crystal structure. Induction annealing is particularly useful in industries requiring complex shaping or reforming of metals, such as automotive, medical, and electrical applications. It is also effective in reversing work hardening and removing internal stresses caused by welding or cold forming. The process involves heating a localized area using induced electric currents, followed by controlled cooling, to achieve the desired material properties.
Key Points Explained:
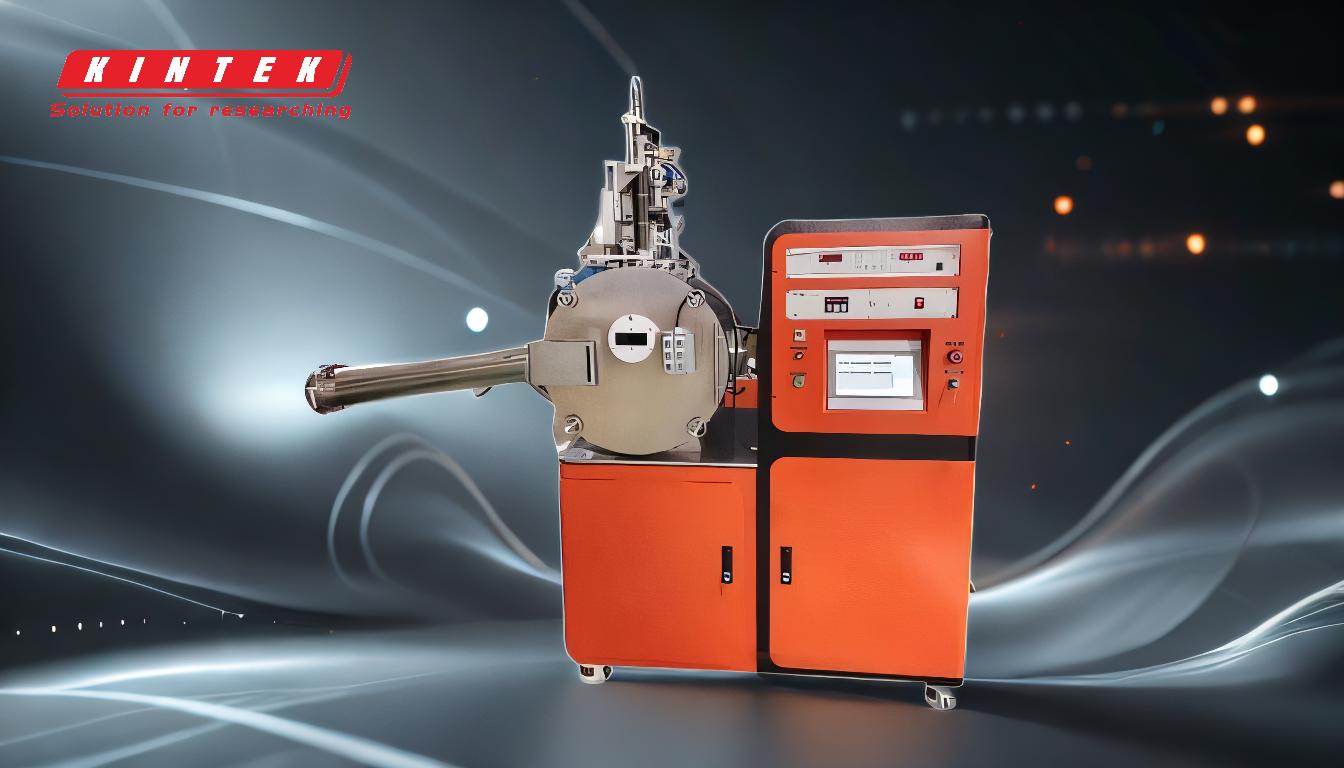
-
Definition of Induction Annealing:
- Induction annealing is a heat treatment process that uses electromagnetic induction to heat a specific area of a metal part. This localized heating allows for precise control over the annealing process, making it ideal for applications requiring selective softening.
-
Purpose of Induction Annealing:
- The primary goal of induction annealing is to increase the ductility and reduce the hardness of a material. This is achieved by reducing dislocations in the material's crystal structure, making it more workable and less brittle.
-
Applications of Induction Annealing:
- Reversing Work Hardening: Induction annealing is used to reverse the effects of work hardening, which occurs during processes like cold forming, drawing, or bending. This makes the material more ductile and suitable for further forming.
- Stress Relief: It is also used to remove internal stresses that develop during welding or other manufacturing processes, ensuring the material's structural integrity.
- Industry-Specific Uses: Induction annealing is widely used in industries such as automotive, medical, forging, ferrous castings, and electrical applications (e.g., transformers and motors).
-
How Induction Annealing Works:
- Induction Heating: The process involves generating heat within the material using induced electric currents. This allows for precise and localized heating of the target area.
- Controlled Cooling: After heating, the material is cooled in a controlled manner to achieve the desired mechanical properties. Unlike hardening processes, annealing does not require rapid quenching.
-
Advantages of Induction Annealing:
- Precision: Induction annealing allows for selective heating, enabling precise control over the treated area.
- Efficiency: The process is energy-efficient and can be completed quickly, reducing production time.
- Versatility: It can be applied to a wide range of materials and geometries, making it suitable for various industrial applications.
-
Technological Advancements and Future Prospects:
- Induction heating technology is continuously evolving, with ongoing research aimed at optimizing process parameters for emerging applications. This includes heating low-resistivity materials and biological tissues for medical purposes. The range of induction heating applications is expected to expand further as technology advances.
By understanding these key points, equipment and consumable purchasers can make informed decisions about incorporating induction annealing into their manufacturing processes, ensuring improved material properties and operational efficiency.
Summary Table:
Key Aspect | Details |
---|---|
Definition | Heat treatment using electromagnetic induction for localized metal softening. |
Purpose | Increases ductility, reduces hardness, and removes internal stresses. |
Applications | Reverses work hardening, stress relief, and industry-specific uses. |
Process | Induction heating followed by controlled cooling. |
Advantages | Precision, efficiency, and versatility in material treatment. |
Future Prospects | Expanding applications in low-resistivity materials and medical fields. |
Optimize your metal heat treatment process with induction annealing—contact us today for expert guidance!