Induction brazing is a specialized joining process that utilizes electromagnetic induction to heat and join metal components. It is widely used across various industries due to its precision, efficiency, and ability to produce high-quality, clean, and strong joints. This method is particularly advantageous for applications requiring localized heating, minimal distortion, and high repeatability. Induction brazing is commonly employed in industries such as automotive, aerospace, electronics, and medical devices, where the integrity of the joint is critical.
Key Points Explained:
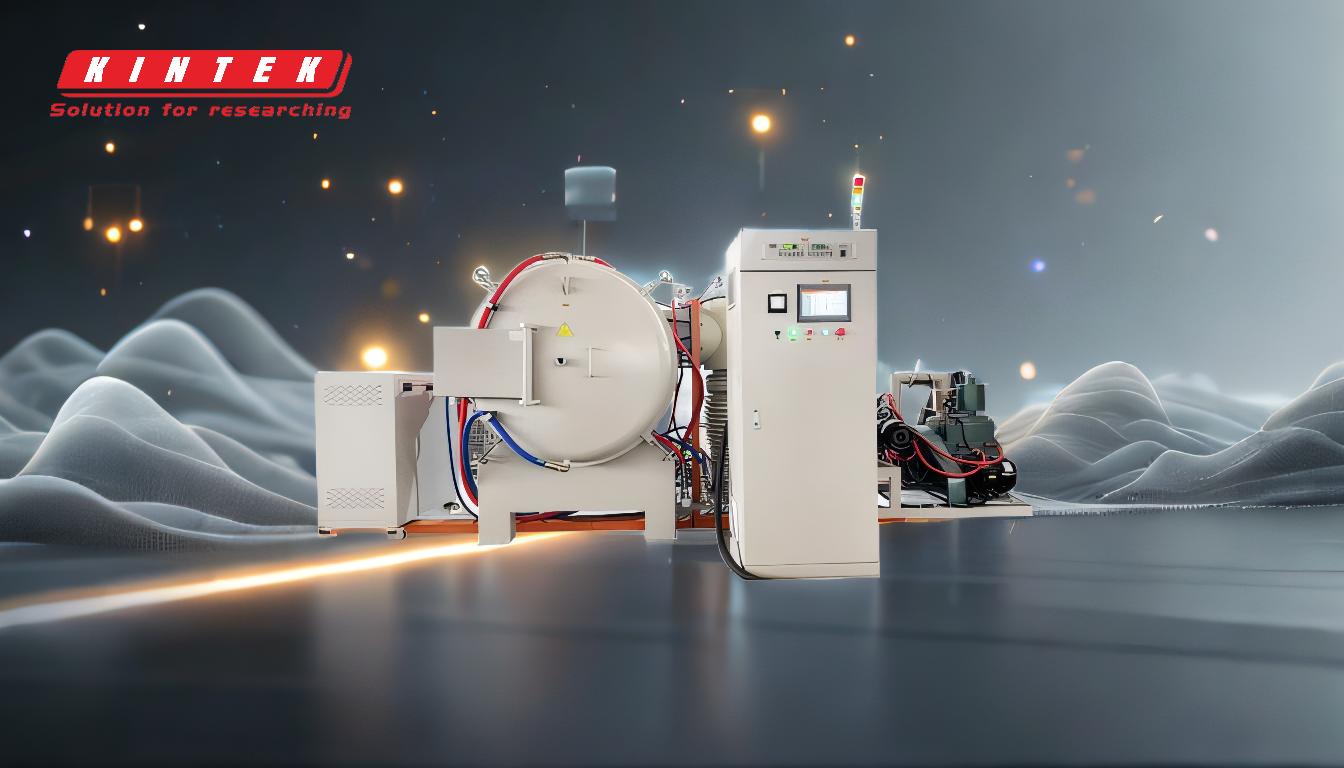
-
Definition and Process of Induction Brazing:
- Induction brazing uses electromagnetic induction to generate heat directly within the workpiece, eliminating the need for external heat sources like flames or furnaces.
- A filler metal with a lower melting point than the base materials is used to create a strong bond between the components.
- The process is highly controllable, allowing for precise temperature management and localized heating.
-
Advantages of Induction Brazing:
- Precision and Control: The ability to focus heat on specific areas reduces the risk of damaging surrounding materials.
- Efficiency: Rapid heating and cooling cycles make the process faster compared to traditional brazing methods.
- Cleanliness: Induction brazing produces minimal oxidation and contamination, resulting in high-quality, clean joints.
- Repeatability: The process is highly consistent, making it ideal for mass production.
-
Applications of Induction Brazering:
- Automotive Industry: Used for joining components such as heat exchangers, fuel injectors, and sensors, where durability and precision are essential.
- Aerospace Industry: Ideal for assembling lightweight, high-strength components like turbine blades and structural parts.
- Electronics Industry: Employed for creating reliable electrical connections in devices such as circuit boards and connectors.
- Medical Devices: Used for assembling precision instruments and implants, ensuring biocompatibility and high performance.
-
Comparison with Other Brazing Methods:
- Vacuum Brazing: While vacuum brazing is excellent for high-temperature applications and producing clean joints, induction brazing offers faster processing times and localized heating.
- Aluminum Brazing: Induction brazing is often preferred for aluminum components due to its ability to prevent overheating and distortion.
- Hydrogen Brazing: Although hydrogen brazing is suitable for high-cleanliness assemblies, induction brazing provides better control over the heating process and is more versatile.
-
Equipment and Consumables:
- Induction brazing requires specialized equipment, including induction heating systems, power supplies, and cooling systems.
- Filler metals, such as silver-based alloys, are commonly used due to their excellent flow properties and strength.
- Fluxes or protective atmospheres may be used to prevent oxidation and ensure a clean joint.
-
Future Trends and Innovations:
- Advancements in induction brazing technology are focused on improving energy efficiency, reducing cycle times, and enhancing automation.
- The integration of robotics and AI is expected to further streamline the process, making it more accessible for complex and high-volume applications.
In summary, induction brazing is a versatile and efficient joining method that plays a critical role in modern manufacturing. Its ability to deliver high-quality, precise, and repeatable results makes it indispensable in industries where performance and reliability are paramount.
Summary Table:
Key Aspect | Details |
---|---|
Definition | Uses electromagnetic induction to heat and join metal components. |
Advantages | Precision, efficiency, cleanliness, and repeatability. |
Applications | Automotive, aerospace, electronics, and medical devices. |
Comparison with Other Methods | Faster and more controlled than vacuum, aluminum, and hydrogen brazing. |
Equipment | Induction heating systems, power supplies, cooling systems, and filler metals. |
Future Trends | Enhanced energy efficiency, automation, and integration of robotics/AI. |
Unlock the potential of induction brazing for your industry—contact our experts today!