Magnetron sputtering is a highly efficient and versatile physical vapor deposition (PVD) technique used to deposit thin films on substrates. It involves the use of plasma ions to sputter material from a target, which then forms a thin, uniform layer on a substrate. This method is widely used in industries such as electronics, optics, and energy due to its ability to produce high-quality, durable, and functional coatings. Applications range from thin-film solar cells and semiconductor chips to wear-resistant coatings and optical layers. Magnetron sputtering offers advantages like high deposition rates, excellent material coverage, and the ability to operate at low temperatures, making it a cost-effective solution for large-scale production.
Key Points Explained:
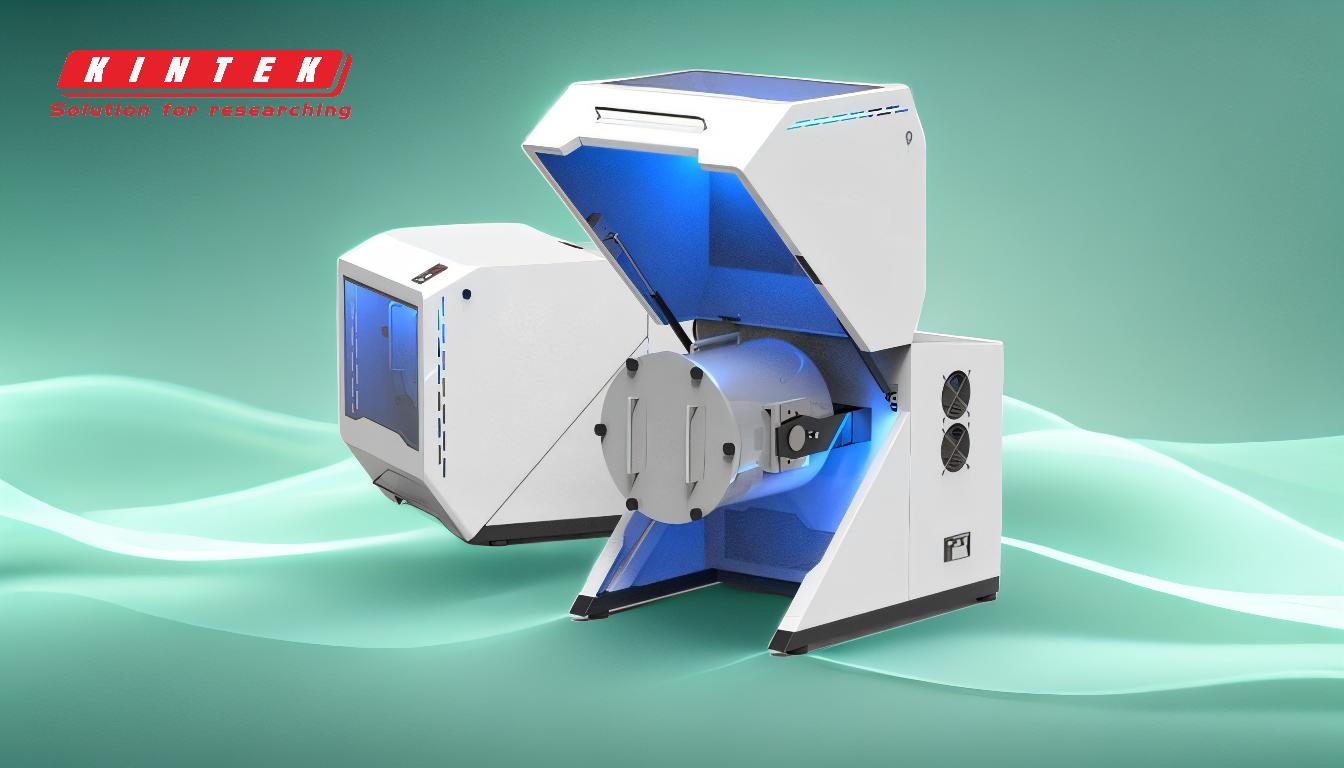
-
Definition and Process of Magnetron Sputtering:
- Magnetron sputtering is a plasma-based PVD method where plasma ions interact with a target material, causing atoms to sputter and form a thin film on a substrate.
- The process involves a high magnetic and electric field to confine plasma electrons close to the target, enhancing the sputtering efficiency.
- This technique is particularly effective for depositing alloys, metals, and other materials onto substrates.
-
Applications of Magnetron Sputtering:
- Electronics: Used for gate dielectrics, passive thin-film components, interlayer dielectrics, sensors, and printed circuit boards.
- Optics: Applied in anti-reflective layers on displays, solar control coatings on glass, and barrier layers for OLEDs and solar cells.
- Energy: Utilized in thin-film solar cells, thin-film batteries, and LED lighting.
- Industrial Coatings: Used for wear-resistant or low-friction coatings on machine parts.
-
Advantages of Magnetron Sputtering:
- High Deposition Rate: Enables rapid production of thin films.
- Uniformity: Ensures consistent film thickness over large-area substrates.
- Material Versatility: Suitable for a wide range of materials, including non-conductive ones (e.g., RF magnetron sputtering).
- High Purity and Adhesion: Produces films with excellent purity and strong adhesion to substrates.
- Low-Temperature Operation: Allows deposition on temperature-sensitive substrates.
-
RF Magnetron Sputtering:
- A specialized form of magnetron sputtering that does not require the target material to be conductive.
- Ideal for depositing dielectric materials, making it suitable for advanced applications in microelectronics and semiconductors.
-
Industrial and Research Relevance:
- Magnetron sputtering is a cornerstone in modern manufacturing and research, particularly in fields requiring precise and high-quality thin films.
- Ongoing advancements in the technique continue to expand its applications and improve its efficiency, making it a critical tool in industries like renewable energy, electronics, and materials science.
By leveraging these key points, equipment and consumable purchasers can better understand the capabilities and benefits of magnetron sputtering systems, enabling them to make informed decisions for their specific applications.
Summary Table:
Aspect | Details |
---|---|
Definition | Plasma-based PVD method for depositing thin films on substrates. |
Applications | Electronics, optics, energy, and industrial coatings. |
Advantages | High deposition rate, uniformity, material versatility, and low-temperature operation. |
RF Magnetron Sputtering | Specialized for non-conductive materials, ideal for microelectronics. |
Relevance | Critical in renewable energy, electronics, and materials science research. |
Ready to enhance your production with magnetron sputtering? Contact us today to learn more!