Metal evaporation is a process used in various industrial and scientific applications to deposit thin films of metal onto a substrate. This technique is particularly important in the fields of electronics, optics, and materials science, where precise and uniform metal coatings are required. The process typically involves heating a metal source to its evaporation point in a vacuum environment, allowing the metal atoms to travel and deposit onto a target substrate. This method is favored for its ability to produce high-purity and uniform thin films, which are essential for applications such as semiconductor fabrication, optical coatings, and protective layers.
Key Points Explained:
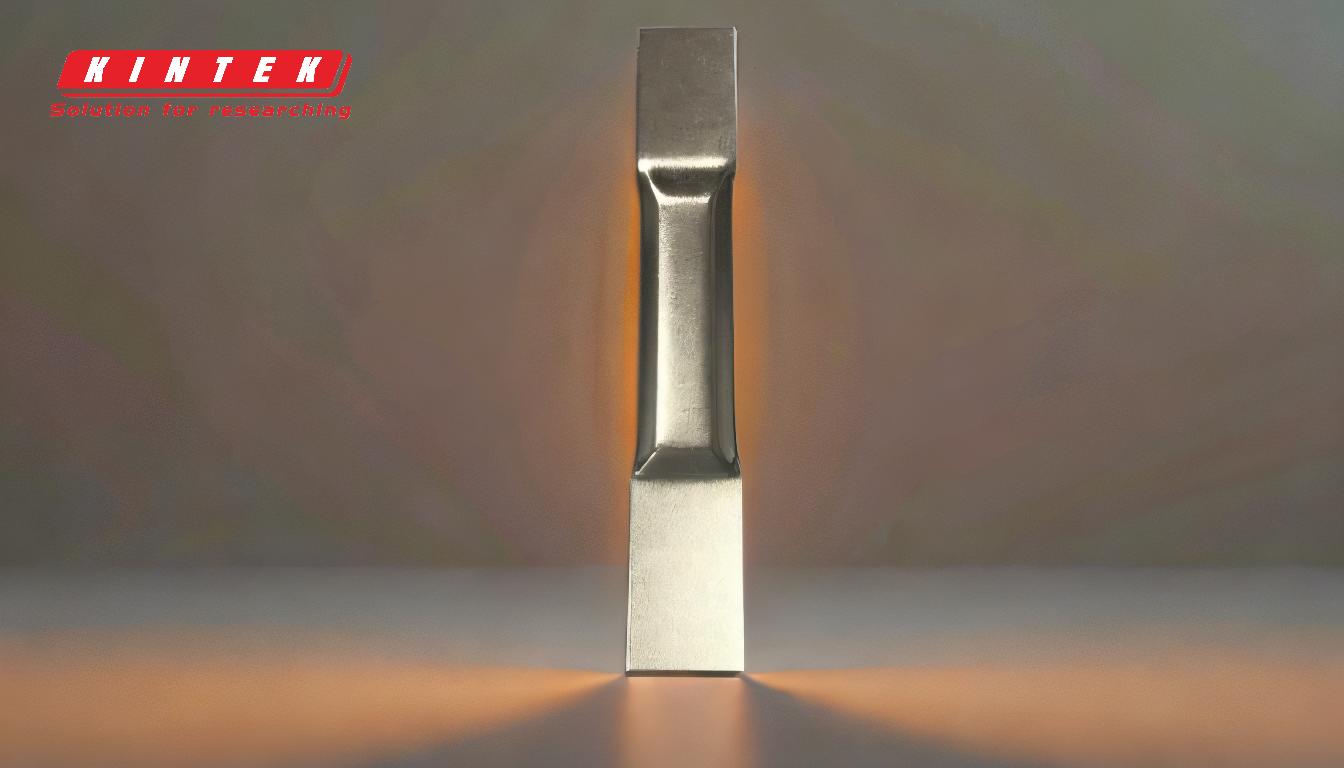
-
Definition and Basic Process:
- Metal evaporation is a physical vapor deposition (PVD) technique where a metal is heated to its evaporation point in a vacuum, causing it to vaporize and then condense onto a substrate to form a thin film.
- The process is conducted in a high-vacuum environment to minimize interactions with other gas molecules, ensuring a clean and efficient deposition.
-
Types of Metal Evaporation Techniques:
- Thermal Evaporation: Involves heating the metal source using resistive heating until it evaporates. This is one of the simplest forms of metal evaporation.
- Electron Beam (E-Beam) Evaporation: Utilizes a focused electron beam to heat the metal source. This method allows for the evaporation of high-melting-point metals and provides precise control over the deposition process.
- Multi-Source Evaporation: Employs multiple evaporation sources to simultaneously deposit different materials, enabling the creation of complex film compositions.
-
Applications of Metal Evaporation:
- Optical Coatings: Used to create reflective and anti-reflective coatings on lenses and mirrors.
- Semiconductor Devices: Essential for depositing metal layers in the fabrication of integrated circuits and other electronic components.
- Decorative Coatings: Applied to various products to enhance their appearance and provide a metallic finish.
- Protective Coatings: Used to form barrier films that protect against corrosion and wear.
-
Advantages of Metal Evaporation:
- High Purity: The vacuum environment ensures that the deposited films are free from contaminants.
- Uniformity: The process allows for the deposition of very thin and uniform layers, which is crucial for many high-tech applications.
- Versatility: Can be used with a wide range of metals and alloys, making it suitable for diverse applications.
-
Challenges and Considerations:
- Equipment Cost: High-vacuum systems and specialized heating sources can be expensive.
- Process Control: Requires precise control of temperature, pressure, and deposition rates to achieve the desired film properties.
- Material Limitations: Some materials may not be suitable for evaporation due to their high melting points or other physical properties.
-
Comparison with Other Deposition Techniques:
- Sputtering: Another PVD technique where atoms are ejected from a target material due to bombardment by energetic ions. Sputtering can deposit a wider range of materials but may not achieve the same level of purity as evaporation.
- Chemical Vapor Deposition (CVD): Involves chemical reactions to deposit thin films. CVD can produce very high-quality films but often requires higher temperatures and more complex equipment.
In summary, metal evaporation is a critical process in modern technology, enabling the creation of high-quality thin films for a variety of applications. Its ability to produce pure, uniform coatings makes it indispensable in industries ranging from electronics to optics. However, the process requires careful control and specialized equipment, which can be a barrier to its use in some contexts.
Summary Table:
Aspect | Details |
---|---|
Definition | A PVD technique where metal is heated to evaporate and deposit on a substrate. |
Key Techniques | Thermal Evaporation, E-Beam Evaporation, Multi-Source Evaporation. |
Applications | Optical coatings, semiconductor devices, decorative & protective coatings. |
Advantages | High purity, uniformity, and versatility. |
Challenges | High equipment cost, precise process control, material limitations. |
Comparison with Others | Sputtering (wider material range), CVD (higher quality but complex setup). |
Interested in metal evaporation for your projects? Contact us today to learn more!