Molding is a manufacturing process that involves shaping raw materials, such as plastics, glass, or ceramics, into a desired form using a mold. The process typically applies heat and pressure to a pliable material, forcing it into the cavity of a mold where it solidifies or hardens to take the shape of the mold. This technique is widely used in industries for producing complex and precise components. Below, the key aspects of molding are explained in detail.
Key Points Explained:
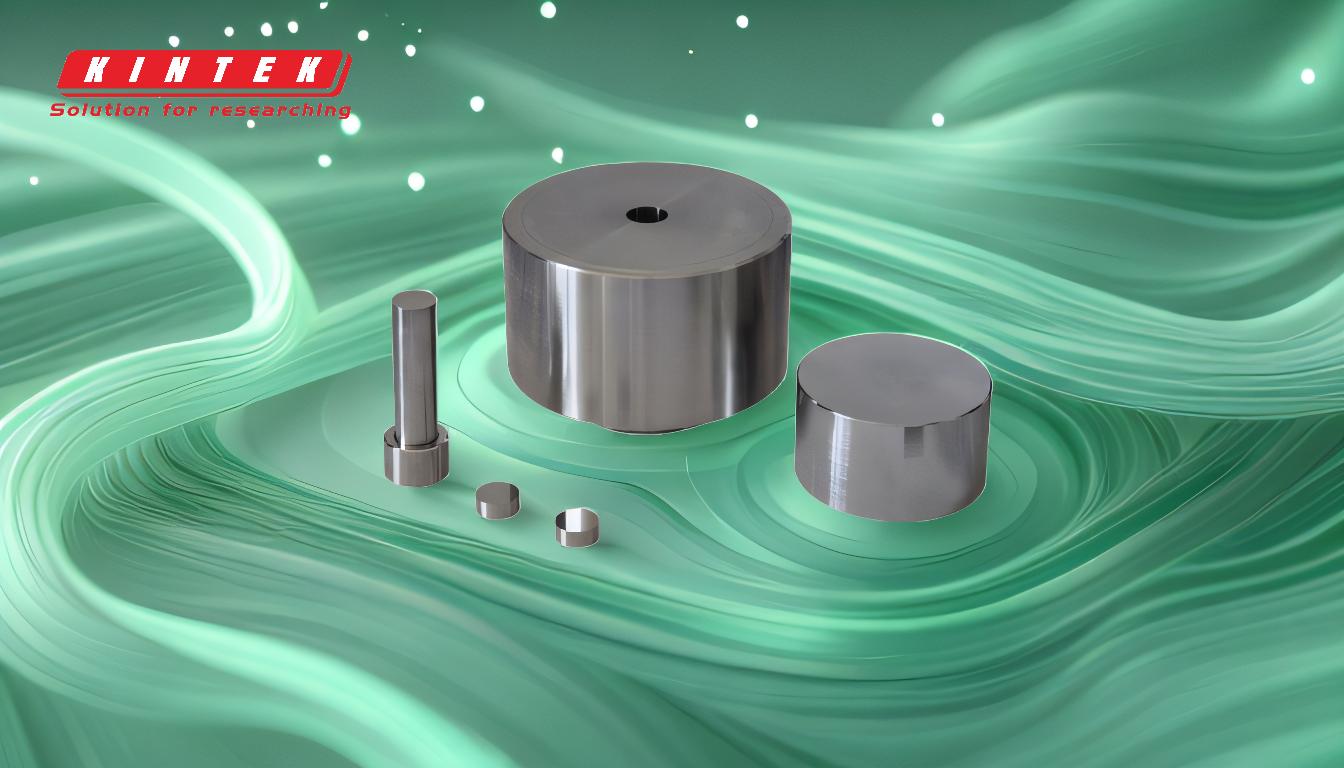
-
Definition of Molding Technique
- Molding is a process where a raw material, often in a pliable state, is shaped into a specific form using a mold.
- The mold acts as a rigid frame or matrix, defining the final shape of the product.
- The process is commonly used for materials like plastics, glass, and ceramics, which can be softened or melted to flow into the mold cavity.
-
Role of Pressure and Heat
- Pressure is applied to force the material into the mold cavity, ensuring it fills every detail of the mold.
- Heat is often used to soften or melt the material, making it easier to flow and conform to the mold's shape.
- The combination of heat and pressure ensures uniformity and precision in the final product.
-
Stages of the Molding Process
- Material Preparation: The raw material is prepared, often in pellet, powder, or liquid form, depending on the type of molding.
- Mold Filling: The material is injected, poured, or pressed into the mold cavity under controlled conditions.
- Solidification: The material is allowed to cool or cure, solidifying into the desired shape.
- Ejection: The finished product is removed from the mold, ready for further processing or use.
-
Types of Molding Techniques
- Injection Molding: Commonly used for plastics, where molten material is injected into a mold under high pressure.
- Blow Molding: Used for creating hollow objects, such as bottles, by inflating heated material into a mold.
- Compression Molding: Involves placing material into a heated mold and compressing it to shape.
- Rotational Molding: Used for large, hollow products, where material is rotated inside a mold to coat its interior.
- Transfer Molding: Similar to compression molding but involves transferring material from a chamber into the mold.
-
Applications of Molding
- Molding is used in a wide range of industries, including automotive, packaging, electronics, and consumer goods.
- It is ideal for producing high-volume, complex, and precise components with consistent quality.
- Examples include plastic housings for electronics, glass bottles, ceramic tiles, and rubber seals.
-
Advantages of Molding
- High Precision: Molding allows for the production of intricate and detailed parts.
- Efficiency: It is suitable for mass production, reducing per-unit costs.
- Material Versatility: A wide range of materials can be used, from thermoplastics to metals.
- Consistency: The process ensures uniformity across multiple products.
-
Challenges in Molding
- Initial Costs: Designing and manufacturing molds can be expensive, especially for complex shapes.
- Material Limitations: Not all materials are suitable for molding, and some may require specific conditions.
- Cycle Time: Depending on the material and process, cooling or curing times can affect production speed.
-
Considerations for Equipment and Consumable Purchasers
- Mold Design: Ensure the mold is designed for the specific material and product requirements.
- Material Selection: Choose materials that are compatible with the molding process and end-use application.
- Equipment Capabilities: Select molding machines that match the production volume and complexity of the parts.
- Maintenance: Regular maintenance of molds and equipment is essential to ensure longevity and consistent quality.
Molding is a versatile and efficient manufacturing technique that plays a critical role in producing a wide variety of products. By understanding the process, its types, and its applications, equipment and consumable purchasers can make informed decisions to optimize production and achieve high-quality results.
Summary Table:
Aspect | Details |
---|---|
Definition | Shaping raw materials using a mold with heat and pressure. |
Key Stages | Material Preparation, Mold Filling, Solidification, Ejection. |
Types of Molding | Injection, Blow, Compression, Rotational, Transfer Molding. |
Applications | Automotive, Packaging, Electronics, Consumer Goods. |
Advantages | High Precision, Efficiency, Material Versatility, Consistency. |
Challenges | High Initial Costs, Material Limitations, Cycle Time. |
Purchasing Tips | Mold Design, Material Selection, Equipment Capabilities, Maintenance. |
Ready to optimize your production with the right molding solution? Contact our experts today for personalized guidance!