A PECVD (Plasma-Enhanced Chemical Vapor Deposition) system is a specialized equipment used for depositing thin films on substrates at relatively low temperatures compared to traditional CVD methods. This process is widely used in semiconductor manufacturing, display technology, and other advanced material applications. The system leverages plasma to enhance the chemical reactions, allowing for lower processing temperatures and better control over film properties. Key components of a PECVD system include the gas system, plasma generator, vacuum chamber, and heating mechanisms, which work together to create a controlled environment for thin-film deposition.
Key Points Explained:
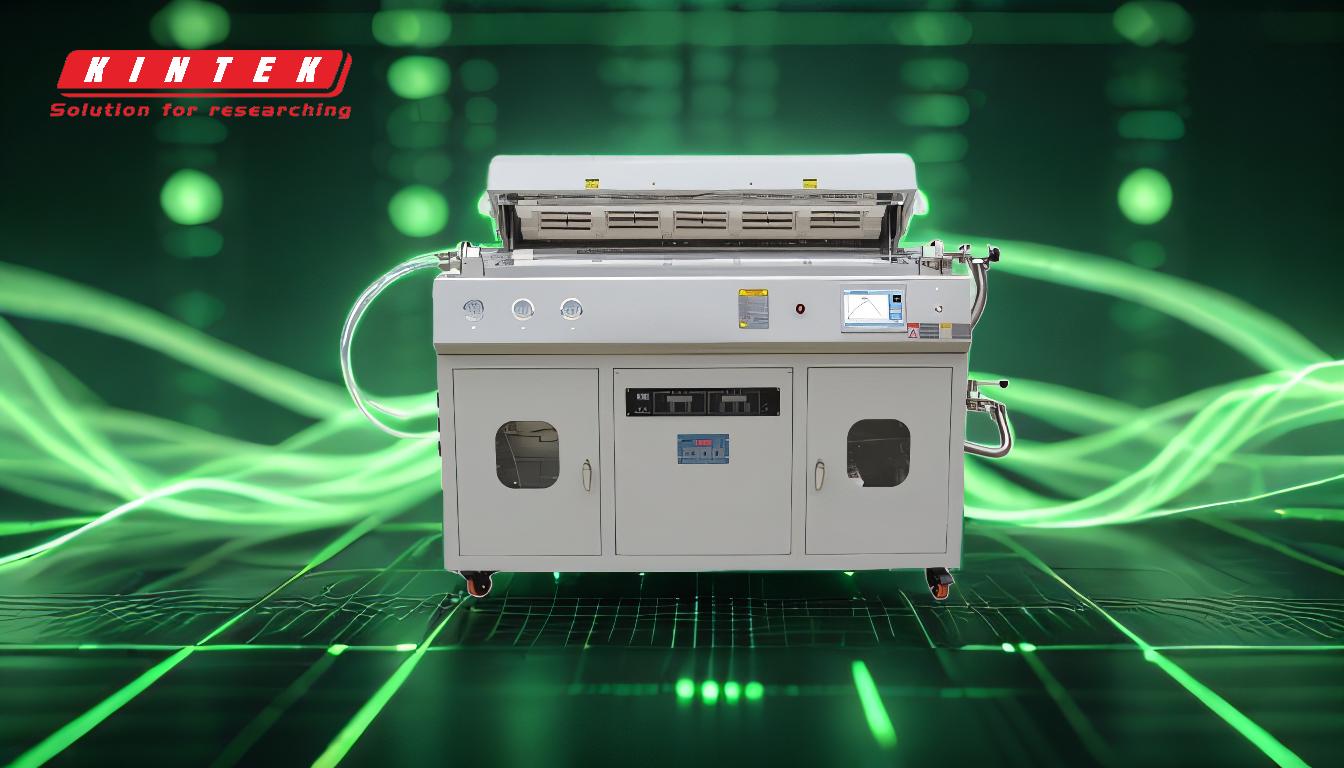
-
Definition and Purpose of PECVD:
- PECVD stands for Plasma-Enhanced Chemical Vapor Deposition, a process used to deposit thin films on substrates.
- It is particularly useful in applications requiring low-temperature processing, such as semiconductor manufacturing and display technology.
-
Main Components of a PECVD System:
- Gas System: Controls the flow and mixture of reactive gases into the chamber.
- Plasma Generator: Creates the plasma needed to ionize the gases and enhance chemical reactions.
- Vacuum Chamber: Maintains a controlled environment with reduced pressure to sustain the plasma state.
- Substrate Heating Device: Heats the substrate to the required temperature and removes impurities.
-
Applications of PECVD:
- Semiconductor Manufacturing: Used for forming insulating layers like silicon oxide and silicon nitride in integrated circuits.
- Display Technology: Essential in producing thin-film transistors (TFT) for LCD displays.
- Advanced Material Development: Applied in creating interlayer insulating films for larger-scale integrated circuits and compound semiconductor devices.
-
Operational Mechanism:
- Radio Frequency Power Supply: Ionizes the reactive gases to create plasma.
- Water Cooling System: Provides cooling for various components, including pumps and the plasma generator.
- Temperature Control System: Ensures the substrate is heated to the precise temperature needed for deposition.
-
Advantages of PECVD:
- Lower Processing Temperatures: Allows for deposition on temperature-sensitive substrates.
- Enhanced Control: Offers better control over film properties and uniformity.
- Versatility: Suitable for a wide range of materials and applications.
-
System Integration and Safety:
- Vacuum and Pressure Control Systems: Maintain the necessary environment for plasma generation and film deposition.
- Safety Protection Systems: Ensure safe operation by monitoring and controlling various parameters.
- Computer Control: Provides precise control and monitoring of the entire deposition process.
By understanding these key points, one can appreciate the complexity and versatility of PECVD systems, making them indispensable in modern material science and electronics manufacturing.
Summary Table:
Aspect | Details |
---|---|
Definition | Plasma-Enhanced Chemical Vapor Deposition for thin-film deposition. |
Key Components | Gas system, plasma generator, vacuum chamber, substrate heating device. |
Applications | Semiconductor manufacturing, display technology, advanced material science. |
Advantages | Lower processing temperatures, enhanced control, versatility. |
Operational Features | RF power supply, water cooling, temperature control, computer integration. |
Learn how a PECVD system can revolutionize your manufacturing process—contact us today!