Physical Vapor Deposition (PVD) is a vacuum-based coating technology used to deposit thin films or coatings onto substrates. The process involves converting a solid or liquid material into a vapor phase through physical mechanisms, transporting the vapor through a vacuum or low-pressure environment, and condensing it onto a substrate to form a thin film. PVD is widely used in industries requiring precise thin-film coatings for mechanical, optical, chemical, or electronic applications, such as semiconductors, solar panels, food packaging, and cutting tools. The process is highly controllable, with variants like sputtering, thermal evaporation, and electron beam deposition, each suited for specific applications.
Key Points Explained:
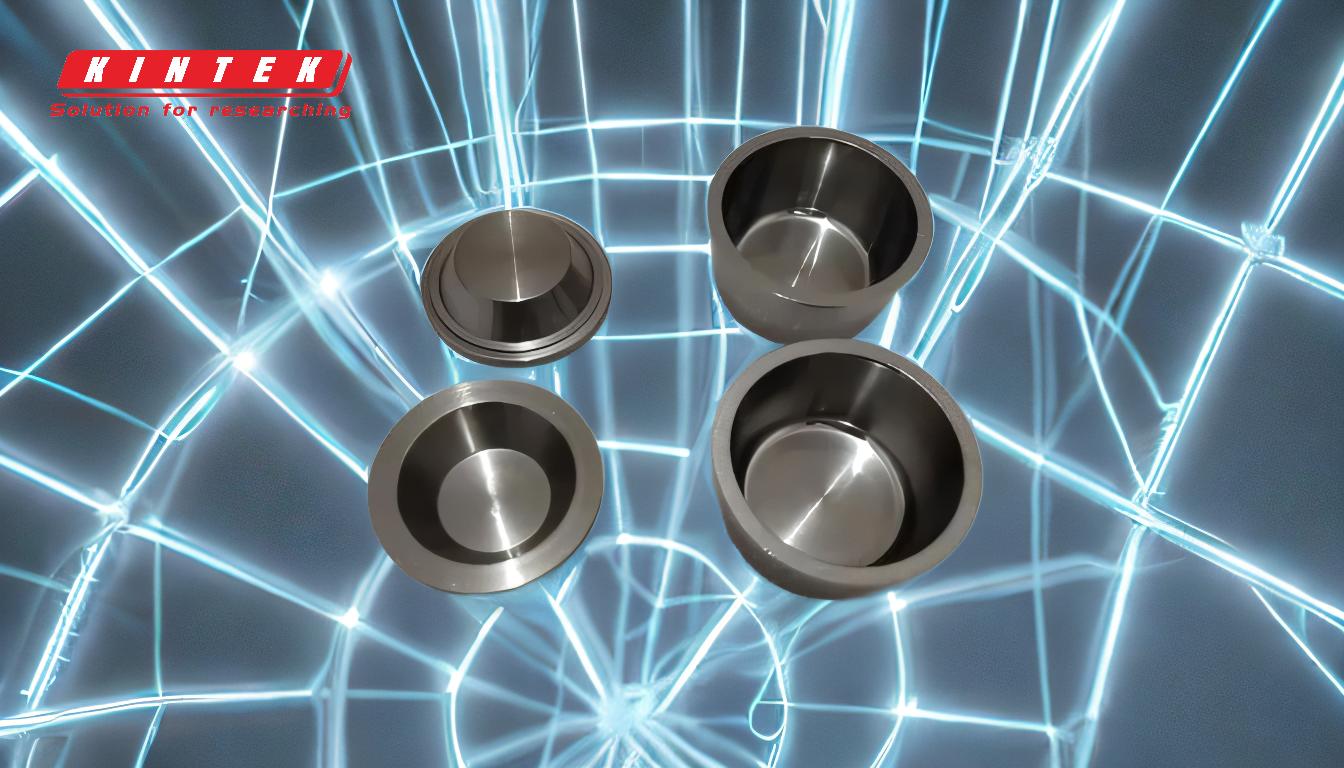
-
Definition and Overview of PVD:
- PVD is a vacuum-based process where a solid or liquid material is vaporized and then condensed onto a substrate to form a thin film.
- It is a physical process, meaning it does not involve chemical reactions to create the vapor phase.
- The process is used to deposit coatings with specific mechanical, optical, chemical, or electronic properties.
-
Core Mechanisms of PVD:
- Vaporization: The target material is converted from a solid or liquid into a vapor phase using physical methods such as sputtering, thermal evaporation, or electron beam bombardment.
- Transport: The vaporized material is transported through a vacuum or low-pressure environment to the substrate.
- Condensation: The vapor condenses on the substrate, forming a thin film or coating.
-
Types of PVD Processes:
- Sputter Deposition: Atoms are ejected from a solid target material through momentum exchange with high-energy particles (e.g., ions) and then deposited onto the substrate.
- Thermal Evaporation: The target material is heated to its vaporization point, and the resulting vapor is deposited onto the substrate.
- Electron Beam Deposition: A high-energy electron beam is used to vaporize the target material, which is then deposited onto the substrate.
- Pulsed Laser Deposition: A laser beam is used to ablate the target material, creating a vapor that is deposited onto the substrate.
- Cathodic Arc Deposition: An electric arc is used to vaporize the target material, which is then deposited onto the substrate.
-
Key Components of PVD Apparatus:
- Vacuum Chamber: The process occurs in a vacuum to minimize contamination and allow particles to travel freely.
- Target Material: The solid or liquid material to be vaporized and deposited.
- Substrate: The surface onto which the thin film is deposited.
- Energy Source: Provides the energy needed to vaporize the target material (e.g., electrical energy, electron beam, laser).
- Quartz Crystal Rate Monitor: Used to control the rate and thickness of the deposited film.
-
Applications of PVD:
- Semiconductor Industry: Used to deposit thin films for electronic devices, such as transistors and solar panels.
- Food Packaging: Aluminized PET films are created using PVD for use in food packaging and balloons.
- Tool Coating: Titanium nitride coatings are applied to cutting tools to improve durability and performance in metalworking.
- Optical Coatings: PVD is used to create anti-reflective and protective coatings for lenses and mirrors.
-
Advantages of PVD:
- Precision: The process allows for precise control over film thickness and composition.
- Versatility: A wide range of materials can be deposited using PVD, including metals, ceramics, and composites.
- Durability: PVD coatings are highly durable and resistant to wear, corrosion, and high temperatures.
- Clean Process: The vacuum environment minimizes contamination, resulting in high-purity coatings.
-
Challenges and Considerations:
- Cost: PVD equipment and processes can be expensive due to the need for vacuum systems and specialized energy sources.
- Complexity: The process requires careful control of parameters such as pressure, temperature, and energy input.
- Substrate Compatibility: The substrate must be able to withstand the vacuum and energy conditions of the PVD process.
In summary, PVD is a versatile and precise technology for depositing thin films and coatings with specific functional properties. Its applications span multiple industries, and its ability to produce high-quality, durable coatings makes it a valuable tool in modern manufacturing. However, the process requires specialized equipment and careful control to achieve optimal results.
Summary Table:
Aspect | Details |
---|---|
Definition | Vacuum-based process to deposit thin films on substrates via vaporization. |
Core Mechanisms | Vaporization, transport through vacuum, condensation on substrate. |
Types of PVD Processes | Sputter deposition, thermal evaporation, electron beam deposition, etc. |
Key Components | Vacuum chamber, target material, substrate, energy source, rate monitor. |
Applications | Semiconductors, food packaging, tool coatings, optical coatings. |
Advantages | Precision, versatility, durability, clean process. |
Challenges | High cost, complexity, substrate compatibility. |
Discover how PVD can enhance your manufacturing process—contact our experts today!