Positive molding, also known as male molding, is a manufacturing process where a mold is created to have the same shape and features as the desired object or component. This type of mold is designed to directly replicate the surface details of the final product, making it ideal for applications where precision and detail are critical. Positive molds are typically used in industries such as automotive, aerospace, and consumer goods, where the quality and accuracy of the final product are paramount.
Key Points Explained:
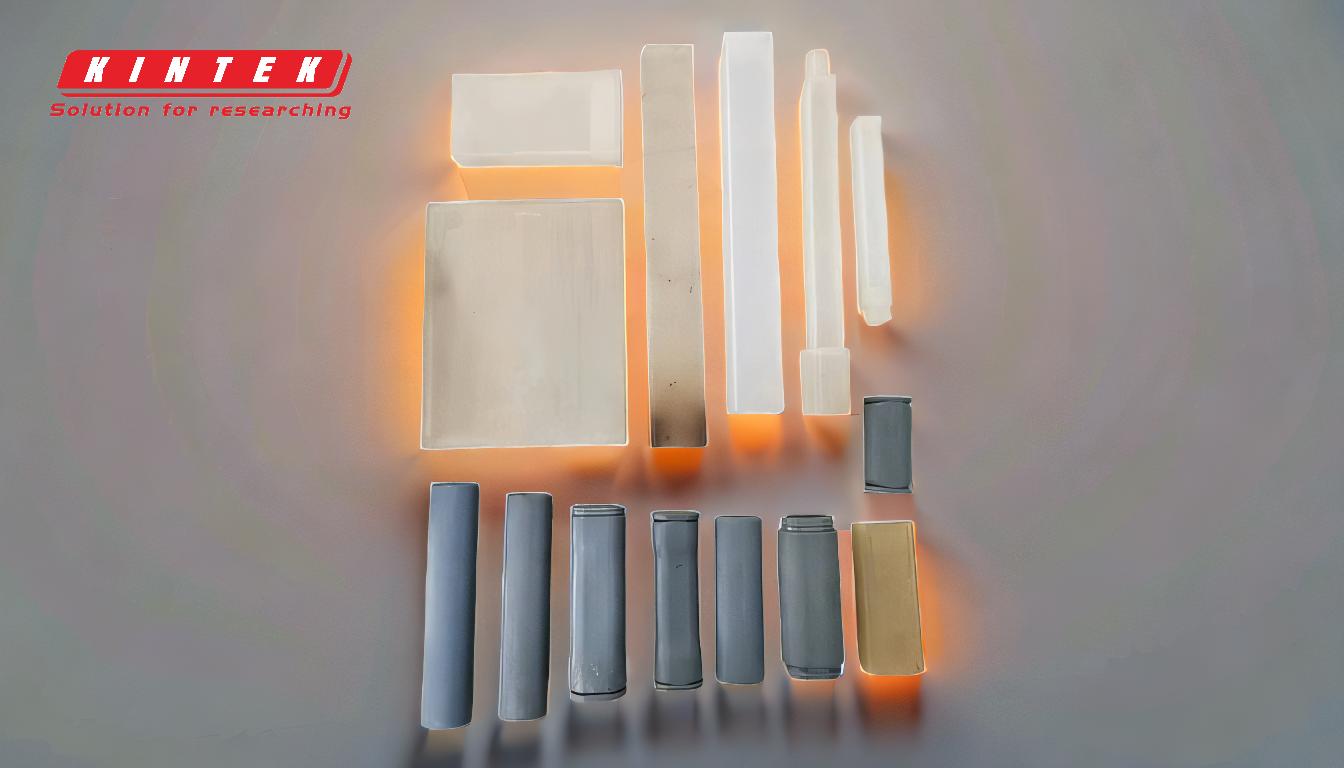
-
Definition of Positive Molding:
- Positive molding involves creating a mold that mirrors the exact shape and features of the desired object. This mold, often referred to as a male mold, is used to produce components with precise surface details.
-
Materials Used in Positive Molds:
- The materials used for positive molds must be capable of accurately replicating the object's surface details. Common materials include metals like aluminum and steel, as well as high-quality plastics and composites. The choice of material depends on the specific requirements of the final product, such as durability, heat resistance, and surface finish.
-
Applications of Positive Molding:
- Automotive Industry: Positive molds are used to create detailed and precise components such as dashboards, interior trim, and exterior body parts.
- Aerospace Industry: In aerospace, positive molds are essential for producing lightweight yet strong components with complex geometries, such as turbine blades and structural elements.
- Consumer Goods: Items like electronic housings, toys, and household appliances often require the high level of detail that positive molding can provide.
-
Advantages of Positive Molding:
- Precision and Detail: Positive molds allow for the creation of components with intricate details and high accuracy.
- Consistency: The use of positive molds ensures that each produced part is consistent in shape and quality, which is crucial for mass production.
- Versatility: Positive molding can be used with a variety of materials, making it suitable for a wide range of applications.
-
Challenges and Considerations:
- Cost: The creation of positive molds can be expensive, particularly when high-precision materials and techniques are required.
- Complexity: Designing and manufacturing positive molds for complex geometries can be challenging and may require advanced engineering and machining capabilities.
- Maintenance: Positive molds need to be maintained regularly to ensure they continue to produce high-quality parts, which can add to the overall cost and effort.
-
Comparison with Negative Molding:
- Positive vs. Negative Molds: While positive molds replicate the object's shape directly, negative molds create a cavity that the material fills to form the object. Negative molds are often used for hollow or concave shapes, whereas positive molds are better suited for solid or convex shapes.
-
Future Trends in Positive Molding:
- Advanced Materials: The development of new materials with enhanced properties, such as higher durability and better heat resistance, is expected to expand the applications of positive molding.
- Automation and AI: The integration of automation and artificial intelligence in the molding process can improve precision, reduce costs, and increase production efficiency.
- Sustainability: There is a growing focus on using sustainable materials and processes in positive molding to reduce environmental impact.
In summary, positive molding is a highly effective manufacturing technique for producing detailed and precise components. Its applications span various industries, and while it comes with certain challenges, ongoing advancements in materials and technology are likely to enhance its capabilities and efficiency further.
Summary Table:
Aspect | Details |
---|---|
Definition | A mold that replicates the exact shape and features of the desired object. |
Materials | Aluminum, steel, plastics, and composites for durability and precision. |
Applications | Automotive, aerospace, and consumer goods for detailed and precise parts. |
Advantages | High precision, consistency, and versatility across materials. |
Challenges | High cost, complexity in design, and regular maintenance requirements. |
Future Trends | Advanced materials, automation, AI integration, and sustainability focus. |
Discover how positive molding can elevate your manufacturing process—contact us today for expert guidance!