Press forging is a manufacturing process where metal is shaped using compressive forces applied by a press. This method is widely used in industries to produce high-strength components with precise dimensions. Unlike hammer forging, which uses rapid impact forces, press forging applies a slow, continuous pressure to deform the metal. This process is ideal for creating complex shapes and ensuring uniform material properties. Hydraulic forging presses, which rely on hydraulic systems to generate the required force, are commonly used in this process. These presses are equipped with various components to ensure safety, precision, and efficiency.
Key Points Explained:
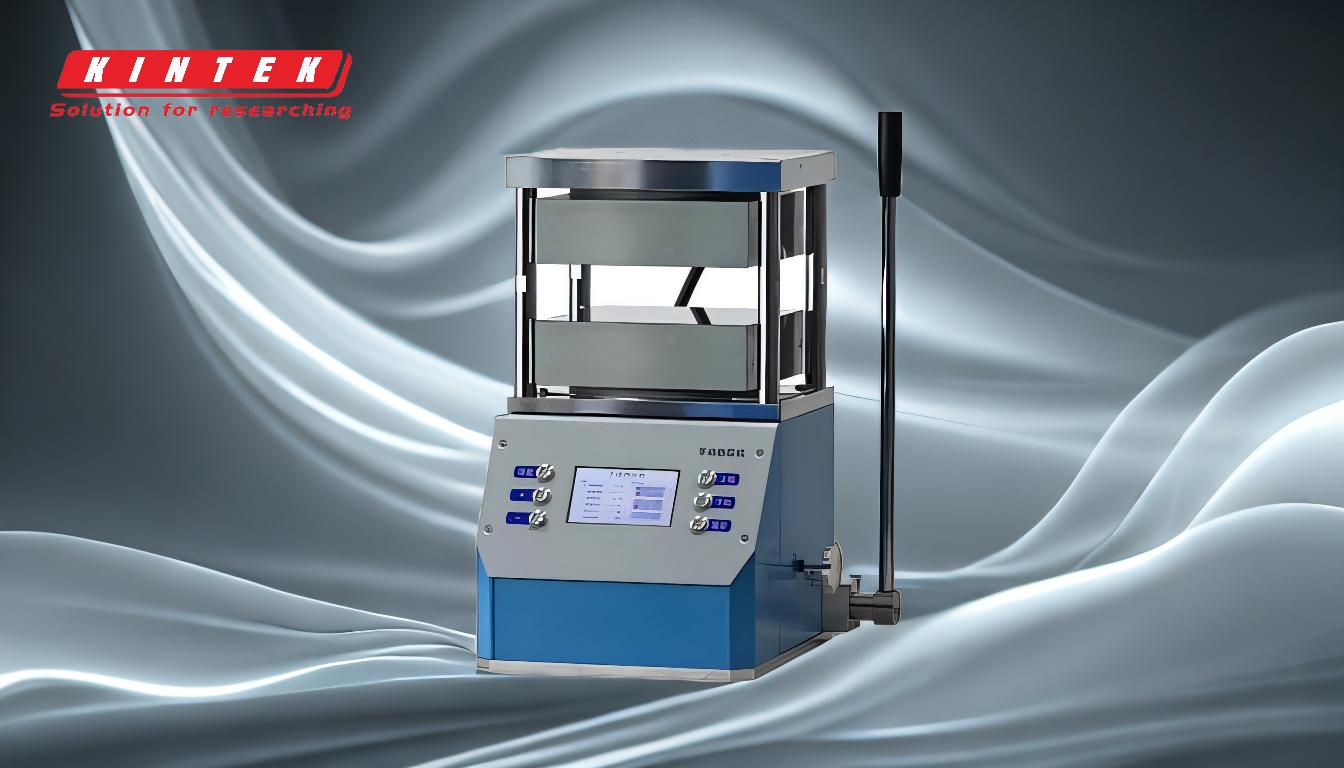
-
Definition of Press Forging:
- Press forging involves shaping metal using a press that applies continuous pressure. This method is suitable for producing parts with high strength and precise dimensions. The slow application of force allows for better control over the deformation process, resulting in uniform material properties.
-
Comparison with Hammer Forging:
- Unlike hammer forging, which uses rapid impact forces, press forging applies a slow, continuous pressure. This difference in force application affects the material's grain structure, with press forging typically resulting in a more uniform and refined grain structure.
-
Types of Press Forging:
- Hydraulic Press Forging: Uses hydraulic systems to generate the required force. It is known for its ability to apply high forces over a long period, making it suitable for large and complex parts.
- Mechanical Press Forging: Utilizes mechanical systems, such as cranks or screws, to apply force. This type is faster but may not provide the same level of control as hydraulic presses.
-
Key Components of a Hydraulic Forging Press:
- Safety Door: Ensures operator safety by preventing access to the press during operation.
- Limit Switch: Controls the movement of the press to prevent over-travel and ensure precise operation.
- Manual Control Valve: Allows operators to manually control the press's movement and pressure.
- Relief Valve: Protects the system from overpressure by releasing excess hydraulic fluid.
- Pressure Gauge: Monitors the hydraulic pressure to ensure it remains within safe and effective limits.
- Hydraulic Cylinder: Converts hydraulic energy into mechanical force to move the press's ram.
- Oil Tank: Stores the hydraulic fluid used in the system.
- Pressing Plate: The component that directly applies force to the workpiece, shaping it as required.
-
Advantages of Press Forging:
- Precision: The slow application of force allows for precise control over the shaping process, resulting in parts with tight tolerances.
- Uniformity: Continuous pressure ensures uniform deformation, leading to consistent material properties throughout the part.
- Complex Shapes: Press forging can produce complex shapes that may be difficult or impossible to achieve with other forging methods.
- Material Efficiency: The process minimizes material waste, making it cost-effective for high-volume production.
-
Applications of Press Forging:
- Automotive Industry: Used to produce high-strength components such as gears, axles, and crankshafts.
- Aerospace Industry: Ideal for manufacturing critical parts that require high precision and strength, such as turbine blades and structural components.
- Construction Industry: Used to create large, durable components like beams and columns.
- Tool and Die Making: Press forging is employed to produce durable tools and dies that can withstand high stress and wear.
-
Considerations for Equipment Purchasers:
- Capacity: Ensure the press has sufficient force capacity for the intended applications.
- Control Systems: Look for advanced control systems that offer precision and ease of operation.
- Safety Features: Prioritize presses with robust safety features to protect operators and equipment.
- Maintenance and Support: Consider the availability of maintenance services and technical support to minimize downtime and ensure long-term reliability.
Press forging is a versatile and efficient manufacturing process that offers numerous advantages in terms of precision, uniformity, and material efficiency. Understanding the key components and considerations can help equipment purchasers make informed decisions when selecting a hydraulic forging press for their specific needs.
Summary Table:
Aspect | Details |
---|---|
Definition | Shaping metal using continuous pressure for high-strength, precise parts. |
Types | Hydraulic (high force, long duration) and Mechanical (faster, less control). |
Key Components | Safety door, limit switch, manual control valve, relief valve, etc. |
Advantages | Precision, uniformity, complex shapes, material efficiency. |
Applications | Automotive, aerospace, construction, tool and die making. |
Considerations | Capacity, control systems, safety features, maintenance, and support. |
Ready to enhance your metal shaping process? Contact us today to find the perfect press forging solution!