Pressure sintering is a specialized manufacturing process that combines heat and pressure to compact and bond powdered materials into a dense, solid mass without reaching the material's melting point. This process is widely used in industries such as powder metallurgy and ceramics to produce components with enhanced strength, durability, and precision. The three primary methods of pressure sintering are hot isostatic pressing (HIP), hot press sintering, and air pressure sintering. Each method applies pressure and heat differently, depending on the material and desired outcome. Pressure sintering is particularly useful for materials with high melting points, such as tungsten and molybdenum, where traditional melting methods are impractical. The process involves blending fine powders, compacting them into a desired shape, and then sintering them under controlled conditions to achieve the final product. This method not only improves material properties but also aligns with principles of resource efficiency and environmental protection.
Key Points Explained:
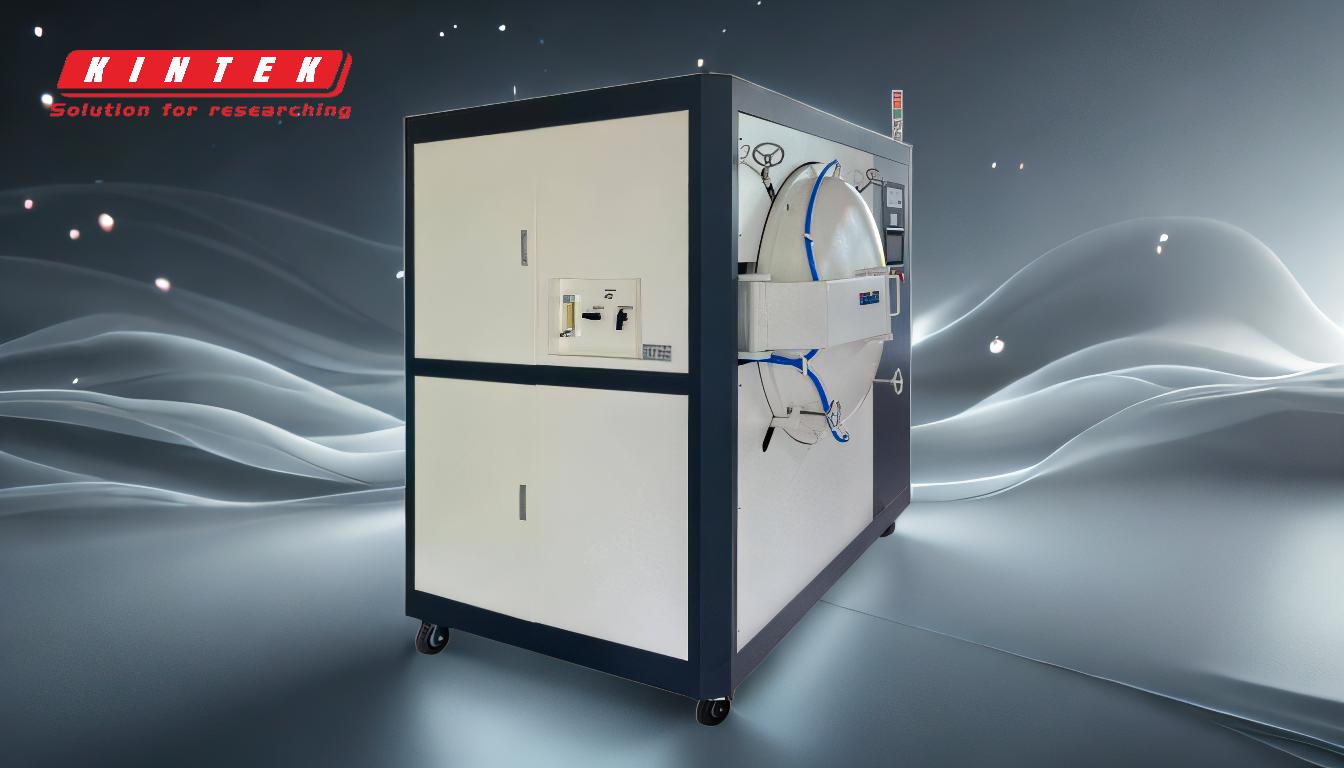
-
Definition of Pressure Sintering:
- Pressure sintering is a process that uses heat and pressure to bond powdered materials into a dense, solid structure without melting the material. This is particularly useful for materials with high melting points, such as tungsten and molybdenum, where traditional melting techniques are not feasible. The process relies on atomic diffusion across particle boundaries to fuse the material into a cohesive mass.
-
Primary Methods of Pressure Sintering:
- Hot Isostatic Pressing (HIP): This method applies uniform pressure and heat from all directions using a gas, such as argon, to achieve a fully dense product. It is ideal for materials requiring high density and uniformity.
- Hot Press Sintering: In this method, pressure and heat are applied uniaxially (in one direction) using a press. It is commonly used for ceramics and metals that require precise shaping.
- Air Pressure Sintering: This technique uses air or another gas to apply pressure during the sintering process. It is often used for materials that are sensitive to oxidation or require controlled atmospheres.
-
Steps in the Sintering Process:
- Blending: Fine powdered materials are mixed to ensure uniformity in composition.
- Compaction: The blended powder is pressed into a desired shape using a die or mold.
- Sintering: The compacted material is heated under controlled conditions, often with applied pressure, to bond the particles together.
-
Applications of Pressure Sintering:
- Powder Metallurgy: Used to produce metal components with complex shapes and high precision, such as gears, bearings, and automotive parts.
- Ceramics: Enables the production of high-strength ceramic components for industrial and medical applications.
- High-Melting-Point Materials: Ideal for materials like tungsten and molybdenum, which are difficult to process using traditional melting methods.
-
Benefits of Pressure Sintering:
- Enhanced Material Properties: Results in components with higher strength, durability, and wear resistance.
- Resource Efficiency: Optimizes raw material usage and reduces waste.
- Environmental Protection: Aligns with sustainable manufacturing practices by minimizing energy consumption and emissions.
-
Role in Steel Production:
- Sintering is a critical step in steel production, where iron ore powder, non-tobacco coal, and lime are mixed and sintered to produce sintered ore. This sintered ore improves blast furnace efficiency, reduces coking ratios, and enhances furnace permeability, ensuring smoother operations.
By understanding the principles and methods of pressure sintering, manufacturers can produce high-quality components with improved performance and sustainability. This process is a cornerstone of modern manufacturing, enabling the creation of advanced materials and products across various industries.
Summary Table:
Aspect | Details |
---|---|
Definition | Combines heat and pressure to bond powdered materials without melting. |
Primary Methods | Hot Isostatic Pressing (HIP), Hot Press Sintering, Air Pressure Sintering. |
Steps | Blending, Compaction, Sintering. |
Applications | Powder metallurgy, ceramics, high-melting-point materials. |
Benefits | Enhanced strength, resource efficiency, environmental protection. |
Role in Steel Production | Improves blast furnace efficiency and reduces coking ratios. |
Learn how pressure sintering can revolutionize your manufacturing process—contact us today for expert guidance!