Preventive maintenance (PM) refers to the systematic and scheduled upkeep of equipment and assets to ensure their optimal performance and longevity. By conducting regular inspections, cleaning, adjustments, and repairs, PM aims to prevent unexpected equipment failures, reduce downtime, and minimize repair costs. This proactive approach helps maintain operational efficiency, extends the lifespan of equipment, and ensures safety in the workplace. It is a critical component of asset management, particularly for industries reliant on machinery and technology.
Key Points Explained:
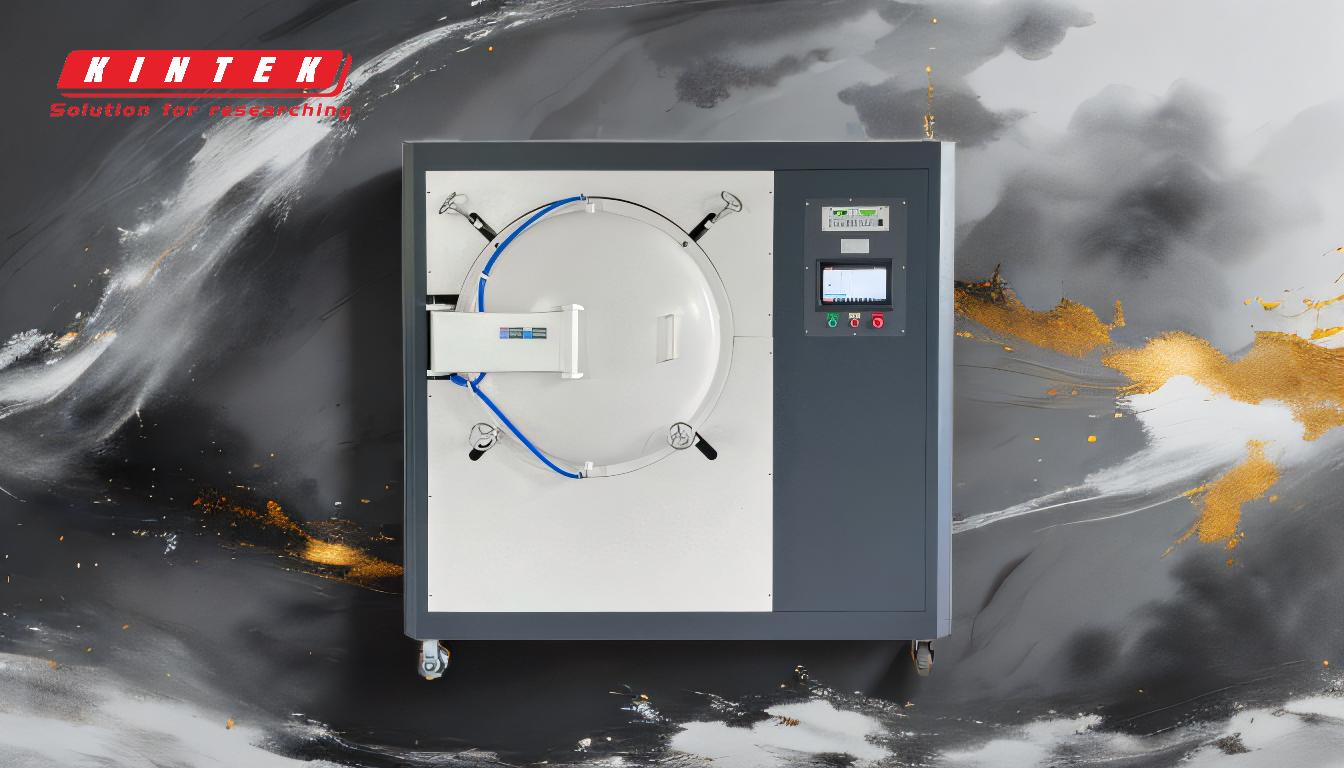
-
Definition and Purpose of Preventive Maintenance
- Preventive maintenance involves scheduled activities to inspect, service, and maintain equipment before issues arise.
- Its primary purpose is to prevent unexpected breakdowns, which can lead to costly downtime and disruptions in operations.
- By addressing potential problems early, PM ensures equipment operates efficiently and safely.
-
Types of Preventive Maintenance
- Time-Based Maintenance: Tasks are performed at regular intervals, such as weekly, monthly, or annually, regardless of equipment usage.
- Usage-Based Maintenance: Maintenance is triggered by the amount of usage, such as after a certain number of operating hours or production cycles.
- Condition-Based Maintenance: Maintenance is performed based on real-time monitoring of equipment conditions, such as vibration, temperature, or pressure.
-
Benefits of Preventive Maintenance
- Reduced Downtime: Regular maintenance minimizes the risk of unexpected failures, keeping operations running smoothly.
- Cost Savings: Preventing major breakdowns reduces the need for expensive repairs or replacements.
- Extended Equipment Lifespan: Proper care and timely repairs help equipment last longer.
- Improved Safety: Well-maintained equipment is less likely to malfunction, reducing the risk of accidents.
- Enhanced Efficiency: Regularly serviced equipment operates at peak performance, saving energy and resources.
-
Key Components of a Preventive Maintenance Program
- Scheduling: Establishing a maintenance calendar to ensure tasks are performed consistently.
- Inspection: Regularly checking equipment for signs of wear, damage, or inefficiency.
- Lubrication and Cleaning: Keeping equipment well-lubricated and free of debris to prevent friction and overheating.
- Calibration and Adjustments: Ensuring equipment operates within specified parameters for accuracy and efficiency.
- Record-Keeping: Documenting maintenance activities to track performance and identify recurring issues.
-
Challenges of Preventive Maintenance
- Initial Costs: Setting up a PM program may require upfront investment in tools, training, and software.
- Resource Allocation: Allocating time and personnel for maintenance tasks can be challenging, especially in high-demand environments.
- Over-Maintenance: Performing maintenance too frequently can lead to unnecessary wear and increased costs.
- Data Management: Keeping accurate records and analyzing data to optimize maintenance schedules requires robust systems.
-
Best Practices for Implementing Preventive Maintenance
- Conduct a Needs Assessment: Identify critical equipment and prioritize maintenance tasks based on their impact on operations.
- Use Technology: Implement maintenance management software to automate scheduling, track tasks, and analyze data.
- Train Personnel: Ensure staff are well-trained to perform maintenance tasks effectively and safely.
- Monitor and Adjust: Continuously evaluate the effectiveness of the PM program and make adjustments as needed.
- Collaborate with Vendors: Work with equipment manufacturers or suppliers to obtain maintenance guidelines and support.
By understanding and implementing preventive maintenance, organizations can significantly enhance their operational efficiency, reduce costs, and ensure the reliability of their equipment.
Summary Table:
Aspect | Details |
---|---|
Definition | Scheduled upkeep to prevent equipment failures and ensure optimal performance. |
Types | Time-Based, Usage-Based, Condition-Based Maintenance. |
Benefits | Reduced downtime, cost savings, extended equipment lifespan, improved safety, enhanced efficiency. |
Key Components | Scheduling, inspection, lubrication, calibration, record-keeping. |
Challenges | Initial costs, resource allocation, over-maintenance, data management. |
Best Practices | Needs assessment, technology use, personnel training, monitoring, vendor collaboration. |
Ready to optimize your equipment performance? Contact us today to start your preventive maintenance program!