PVD (Physical Vapor Deposition) coating is a vacuum-based process where a solid material is vaporized and then deposited onto a target material, forming a thin, durable, and functional layer. This process occurs in a vacuum chamber at high temperatures, typically between 50°C and 750°C, and involves the vaporized atoms traveling in a straight line to embed themselves into the target material. PVD coatings are known for their ability to enhance surface properties such as hardness, wear resistance, and chemical stability, while also being environmentally friendly. The process is highly controllable, allowing for precise modifications to the coating's composition and properties by introducing reactive gases.
Key Points Explained:
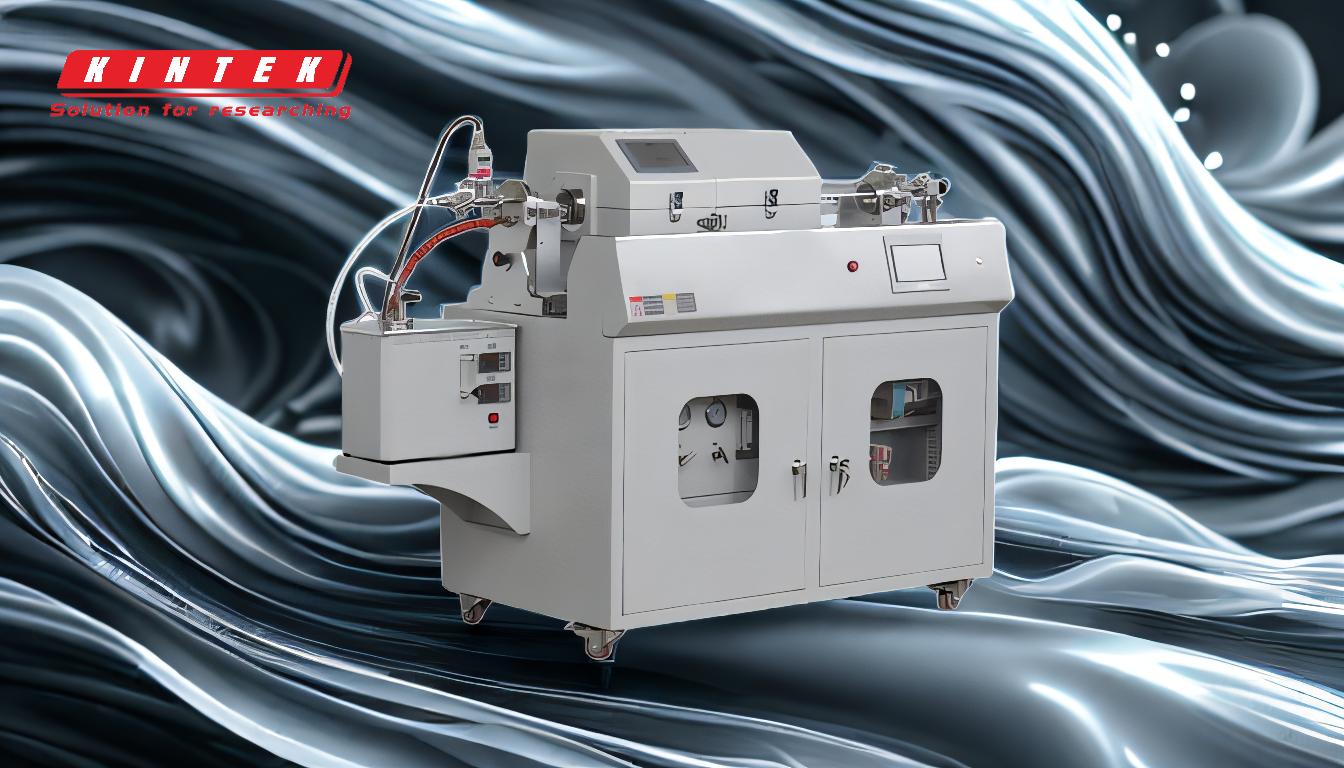
-
Basic Principle of PVD Coating:
- PVD coating involves converting a solid material (target) into vapor in a vacuum chamber.
- The vaporized material condenses and forms a thin, bonded layer on the target material (work-piece).
- This process occurs atom by atom, ensuring a uniform and durable coating.
-
Vacuum Chamber Environment:
- The process takes place in a vacuum chamber to ensure the vaporized material remains clean and uncontaminated.
- The vacuum environment allows the vaporized atoms to travel in a straight line, adhering to the target material in their path.
-
Temperature Range:
- PVD coating is performed at high temperatures, typically between 50°C and 750°C.
- The specific temperature depends on the material being vaporized and the desired properties of the coating.
-
Line of Sight Deposition:
- PVD is a "line of sight" technique, meaning the vaporized atoms travel directly to the target material.
- Proper positioning or rotation of the target material is crucial to ensure even and complete coverage.
-
Coating Composition and Modification:
- The composition of the coating can be modified by introducing reactive gases (e.g., nitrogen) during the process.
- For example, adding nitrogen can result in the formation of metal nitrides, which enhance the coating's hardness and wear resistance.
-
Techniques for Vaporization:
- Various methods are used to vaporize the solid material, including:
- Sputtering: Bombarding the target material with ions to dislodge atoms.
- Cathodic Arc: Using an electric arc to vaporize the target material.
- Electron Beam: Heating the target material with an electron beam.
- Thermal Evaporation: Heating the target material in a crucible until it vaporizes.
- Various methods are used to vaporize the solid material, including:
-
Properties of PVD Coatings:
- Thickness: PVD coatings are extremely thin, typically ranging from 0.5 to 5 micrometers.
- Hardness: The coatings significantly increase the surface hardness of the target material.
- Wear Resistance: PVD coatings improve the material's resistance to wear and abrasion.
- Chemical Stability: The coatings are chemically stable, making them resistant to corrosion and oxidation.
- Aesthetic Appeal: PVD coatings can be adjusted to achieve various colors and finishes, enhancing the product's appearance.
-
Environmental Benefits:
- PVD coating is considered more environmentally friendly compared to other coating methods like CVD (Chemical Vapor Deposition).
- The process produces minimal waste and does not involve harmful chemicals, making it a sustainable option.
-
Applications of PVD Coatings:
- PVD coatings are widely used in industries such as:
- Automotive: For coating engine components, tools, and decorative parts.
- Aerospace: For enhancing the durability and performance of aircraft components.
- Medical: For coating surgical instruments and implants to improve biocompatibility and wear resistance.
- Electronics: For coating semiconductors and other electronic components to enhance conductivity and durability.
- Consumer Goods: For coating watches, jewelry, and other decorative items to improve appearance and durability.
- PVD coatings are widely used in industries such as:
-
Advantages of PVD Coating:
- Durability: PVD coatings are highly durable and resistant to chipping, cracking, and peeling.
- Versatility: The process can be used to coat a wide range of materials, including metals, ceramics, and plastics.
- Precision: PVD allows for precise control over the coating's thickness, composition, and properties.
- Eco-Friendly: The process is environmentally friendly, producing minimal waste and emissions.
In summary, PVD coating is a sophisticated and versatile process that enhances the properties of materials by applying a thin, durable, and functional layer. Its ability to improve hardness, wear resistance, and chemical stability, combined with its environmental benefits, makes it a preferred choice in various industries.
Summary Table:
Key Aspect | Details |
---|---|
Process | Vacuum-based, high-temperature (50°C–750°C) deposition of vaporized atoms. |
Coating Thickness | 0.5–5 micrometers. |
Key Properties | Hardness, wear resistance, chemical stability, aesthetic appeal. |
Vaporization Techniques | Sputtering, Cathodic Arc, Electron Beam, Thermal Evaporation. |
Applications | Automotive, Aerospace, Medical, Electronics, Consumer Goods. |
Advantages | Durable, versatile, precise, eco-friendly. |
Discover how PVD coating can elevate your product's performance—contact our experts today!