Physical Vapor Deposition (PVD) is a manufacturing process used to deposit thin films of material onto a substrate. This technique involves the physical transfer of material from a solid source to a substrate in a vacuum environment. PVD is widely used in various industries, including aerospace, optics, and decorative coatings, due to its ability to produce high-quality, durable, and precise thin films. The process is versatile, allowing for the deposition of materials with thicknesses ranging from a few nanometers to micrometers, and it can be used to create multilayer coatings, graded compositions, and hybrid structures.
Key Points Explained:
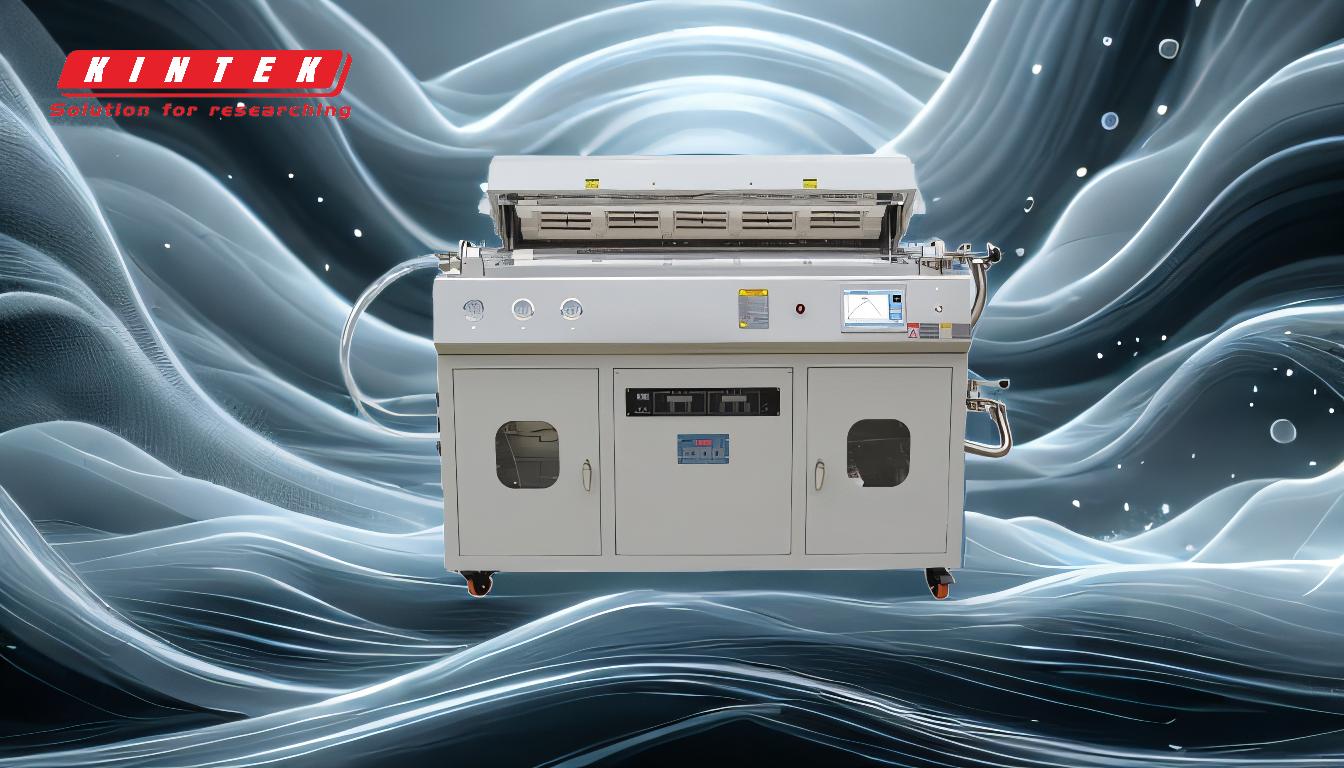
-
Definition and Process of PVD:
- PVD is a vacuum-based process where material is physically transferred from a solid source to a substrate.
- The process typically involves the evaporation or sputtering of the source material, which then condenses on the substrate to form a thin film.
- This method is highly controlled, allowing for precise deposition of materials with specific properties.
-
Applications of PVD:
- High-Temperature and Ablation Resistance: PVD coatings are used to enhance the resistance of substrates to high temperatures and ablation, making them ideal for aerospace applications.
- Optics: In the optics industry, PVD is used to create highly sophisticated mirrors and coated glasses. These coatings can be protective, reflective, or absorbing, and are essential for components in laser systems and optical instruments.
- Decorative Coatings: PVD is also used for decorative purposes, providing durable and aesthetically pleasing finishes on various materials, including glass.
-
Advantages of PVD:
- Precision and Control: PVD allows for the deposition of very thin and uniform layers, which is crucial for applications requiring high precision.
- Versatility: The process can be used to deposit a wide range of materials, including metals, ceramics, and composites, and can create complex multilayer structures.
- Durability: PVD coatings are known for their hardness and resistance to wear, making them suitable for demanding environments.
-
Hybrid Techniques:
- PVD can be combined with other deposition techniques, such as microwave plasma chemical vapor deposition, to create hybrid processes that leverage the strengths of each method.
- These hybrid techniques can produce coatings with unique properties, such as enhanced adhesion, improved wear resistance, and tailored optical characteristics.
-
Future Trends:
- The continued development of PVD technology is expected to lead to even more advanced applications, particularly in the fields of nanotechnology and advanced materials.
- Innovations in PVD processes, such as the integration of plasma-enhanced techniques, are likely to expand the range of materials and substrates that can be effectively coated.
In summary, PVD is a critical technology in modern manufacturing, offering precise, durable, and versatile solutions for a wide range of applications. Its ability to produce high-quality thin films makes it indispensable in industries such as aerospace, optics, and decorative coatings. The ongoing evolution of PVD techniques, including hybrid processes, promises to further enhance its capabilities and applications in the future.
Summary Table:
Aspect | Details |
---|---|
Definition | Vacuum-based process for transferring material from a solid source to a substrate. |
Key Applications | Aerospace, optics, decorative coatings. |
Advantages | Precision, versatility, durability. |
Hybrid Techniques | Combines with methods like microwave plasma CVD for enhanced properties. |
Future Trends | Nanotechnology, advanced materials, and plasma-enhanced techniques. |
Unlock the potential of PVD for your manufacturing needs—contact our experts today!