Sintered metal is a versatile material with a wide range of applications across various industries. It is primarily used for creating custom metal forms, especially in 3D printing, due to its relatively low sintering temperature. This makes it ideal for combining metals with high melting points. Additionally, sintering is employed in the production of sintered plastic and filters, showcasing its adaptability in different manufacturing processes. The unique properties of sintered metal, such as porosity and strength, make it suitable for applications ranging from automotive components to filtration systems.
Key Points Explained:
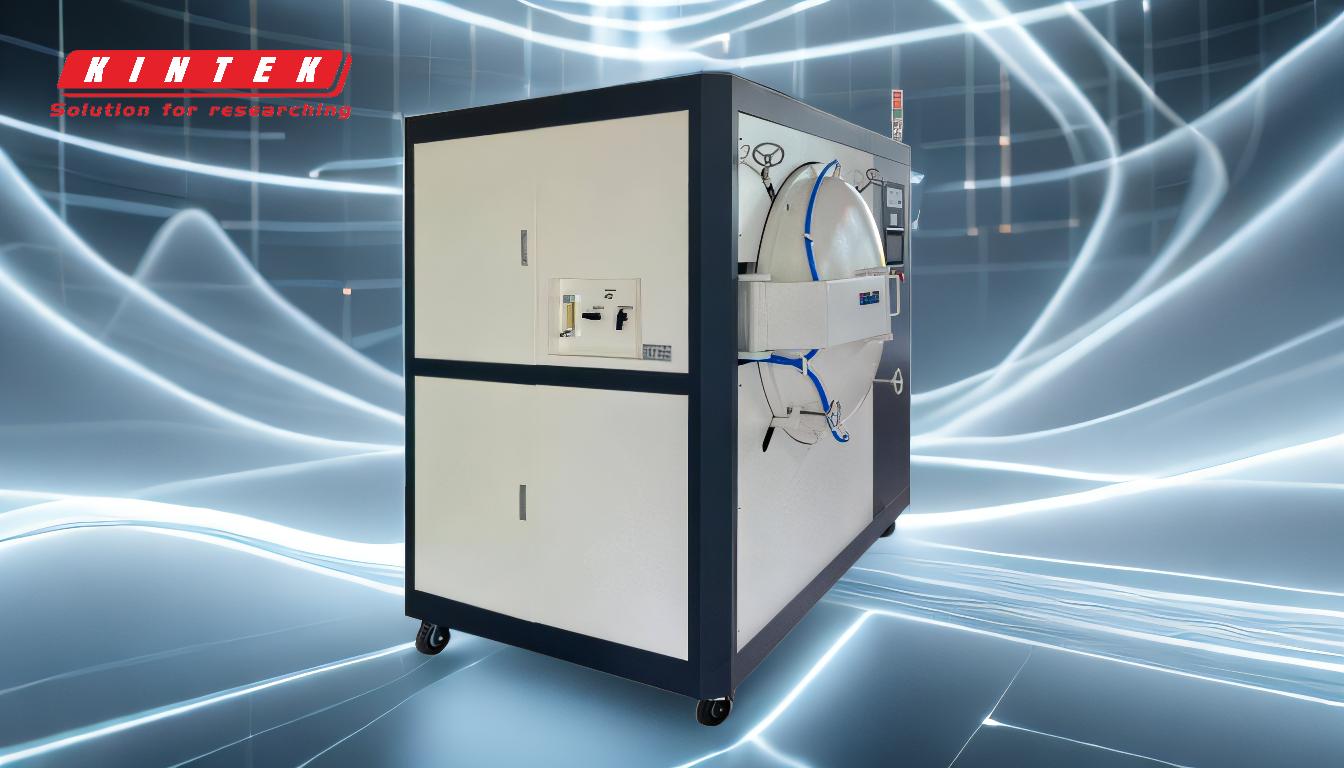
-
Custom Metal Forms in 3D Printing:
- Sintered metal is extensively used in 3D printing to create custom metal forms. The sintering process allows for the precise shaping of metal powders into complex geometries, which is particularly useful in additive manufacturing. This method is advantageous because it operates at lower temperatures compared to traditional melting processes, making it suitable for metals with high melting points.
-
Combining High Melting Point Metals:
- One of the primary uses of sintered metal is in the combination of metals that have high melting points. Traditional melting methods can be inefficient or impractical for these metals, but sintering provides a viable alternative. By using powdered metals and applying heat and pressure, sintering allows these metals to be fused without reaching their melting points, resulting in strong and durable components.
-
Sintered Plastic and Filters:
- Beyond metals, sintering is also applied in the creation of sintered plastic and filters. Sintered plastic is used in various applications where porous or lightweight materials are needed. Sintered filters, on the other hand, are widely used in industries such as automotive, chemical, and food processing for their ability to provide precise filtration. The porous nature of sintered materials makes them ideal for filtering liquids and gases, ensuring high efficiency and durability.
-
Industrial Applications:
- Sintered metals find applications in numerous industries, including automotive, aerospace, and electronics. In the automotive industry, sintered metal components are used in engines, transmissions, and braking systems due to their strength and wear resistance. In aerospace, sintered metals are valued for their lightweight and high-performance characteristics. The electronics industry utilizes sintered metals in components like connectors and heat sinks, where thermal conductivity and durability are crucial.
-
Advantages of Sintered Metals:
- The sintering process offers several advantages, including the ability to produce complex shapes with high precision, excellent material properties, and cost-effectiveness. Sintered metals typically have good mechanical properties, such as high strength and wear resistance, making them suitable for demanding applications. Additionally, the process allows for the use of a wide range of materials, including alloys, which can be tailored to meet specific requirements.
In summary, sintered metal is a highly adaptable material with applications ranging from custom metal forms in 3D printing to the production of filters and industrial components. Its unique properties and the advantages of the sintering process make it a valuable material in various high-tech and industrial applications.
Summary Table:
Application | Description |
---|---|
Custom Metal Forms (3D Printing) | Used in additive manufacturing to create complex geometries with high precision. |
Combining High Melting Point Metals | Fuses metals without melting, ideal for durable, high-strength components. |
Sintered Plastic and Filters | Produces lightweight, porous materials for filtration and specialized applications. |
Industrial Applications | Used in automotive, aerospace, and electronics for strength, wear resistance, and thermal conductivity. |
Advantages | High precision, cost-effectiveness, and tailored material properties. |
Learn how sintered metal can enhance your manufacturing process—contact us today!