Sintering at low temperature is a process that consolidates powdery materials into dense, solid bodies using heat and pressure, but at temperatures significantly below the material's melting point. This method is energy-efficient and allows for greater control over material properties, making it particularly useful for high-melting-point materials and advanced manufacturing techniques like 3D printing. The process involves the diffusion of atoms across particle boundaries, fusing them together without liquefaction, resulting in a harder, stronger, and more durable mass. Cold sintering, a variant of this process, uses a transient solvent and pressure to achieve similar results at even lower temperatures.
Key Points Explained:
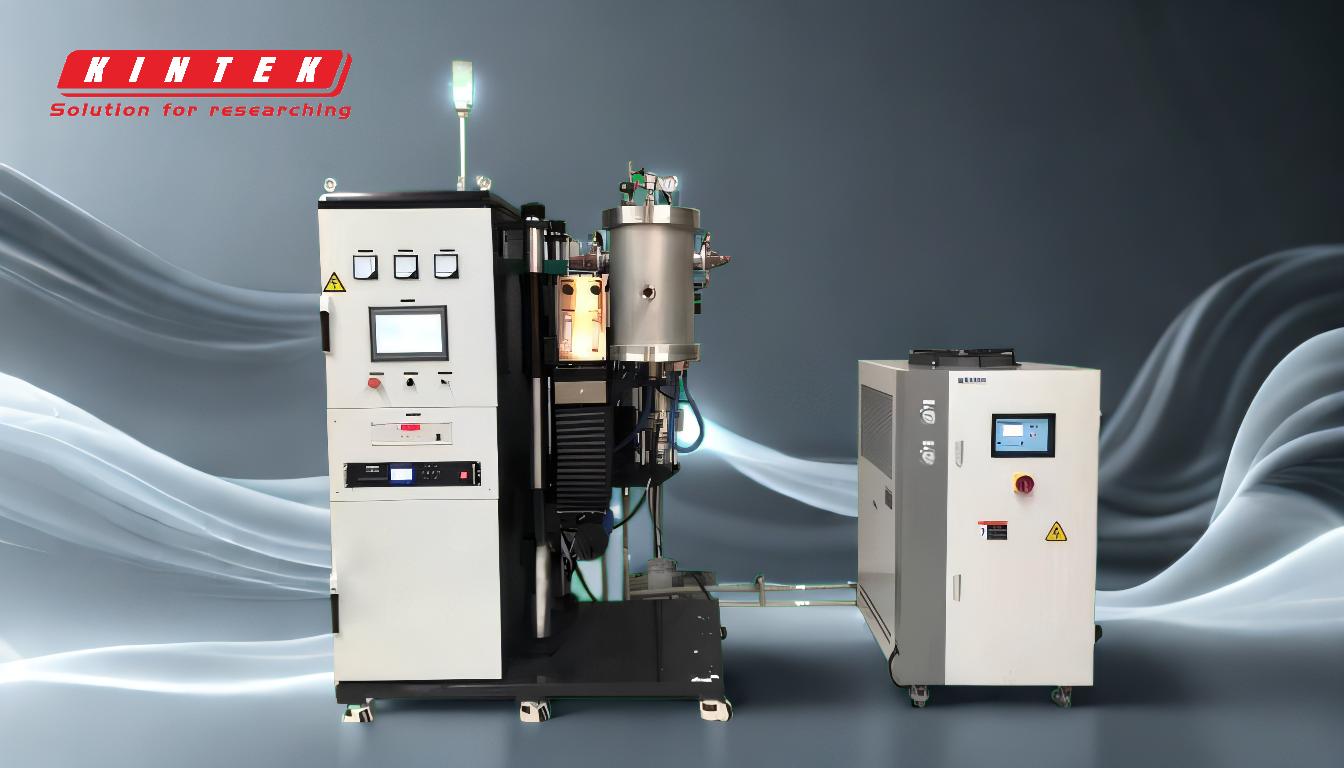
-
Definition of Low-Temperature Sintering:
- Sintering at low temperature is a process that transforms powdery materials into dense, solid bodies by applying heat and pressure, but at temperatures below the material's melting point.
- This method avoids liquefaction, allowing for the consolidation of materials without reaching their melting points.
-
Energy Efficiency:
- One of the primary advantages of low-temperature sintering is its energy efficiency. By operating at lower temperatures, the process consumes less energy compared to traditional sintering methods that require higher temperatures.
- This is particularly beneficial for materials with high melting points, such as tungsten and molybdenum, where traditional sintering would be energy-intensive.
-
Material Control and Consistency:
- Low-temperature sintering offers greater control over the material properties, leading to more consistent and predictable outcomes.
- This control is crucial in applications where material consistency is paramount, such as in the production of ceramics and metals for industrial use.
-
Applications in Advanced Manufacturing:
- The process is particularly useful in advanced manufacturing techniques like 3D printing, where precise control over material properties is essential.
- By enabling sintering at lower temperatures, it allows for the use of a broader range of materials in additive manufacturing, expanding the possibilities for innovation.
-
Cold Sintering:
- Cold sintering is a specialized form of low-temperature sintering that uses a transient solvent and pressure to consolidate materials.
- This method can achieve similar results to traditional sintering but at even lower temperatures, further enhancing energy efficiency and material control.
-
Stages of Sintering:
- The sintering process typically occurs in stages, each designed to increase the structural integrity and strength of the final product.
- These stages involve the gradual application of heat and pressure, allowing for the diffusion of atoms across particle boundaries, which fuses the particles together into a solid mass.
-
Benefits for High-Melting-Point Materials:
- Low-temperature sintering is particularly advantageous for materials with extremely high melting points, as it allows for their consolidation without the need for excessive heat.
- This makes the process suitable for a wide range of applications, from industrial ceramics to advanced metal alloys.
-
Enhanced Durability and Strength:
- The sintering process results in a harder, stronger, and more durable mass, making it ideal for applications where material strength is critical.
- By forcing atoms into tighter bonds, sintering enhances the mechanical properties of the material, ensuring it can withstand significant stress and wear.
In summary, sintering at low temperature is a versatile and efficient process that offers numerous advantages, particularly in terms of energy savings, material control, and the ability to work with high-melting-point materials. Its applications in advanced manufacturing and industrial production make it a valuable technique in modern material science and engineering.
Summary Table:
Key Aspect | Details |
---|---|
Definition | Consolidates powdery materials into dense bodies below melting point. |
Energy Efficiency | Consumes less energy, ideal for high-melting-point materials. |
Material Control | Offers precise control over material properties for consistent outcomes. |
Applications | Widely used in 3D printing and industrial ceramics/metal production. |
Cold Sintering | Uses transient solvent and pressure for even lower-temperature sintering. |
Enhanced Durability | Produces harder, stronger, and more durable materials. |
Discover how low-temperature sintering can revolutionize your manufacturing process—contact our experts today!