Sintering dental materials is a critical process in dentistry that involves compacting and forming solid dental products, such as crowns, bridges, and implants, by applying heat and pressure without melting the material. This process enhances the material's strength, durability, and structural integrity, making it suitable for dental applications. Sintering is particularly useful for materials with high melting points, such as ceramics and metal alloys, as it allows for the creation of dense, durable dental restorations without the need for liquefaction. The process involves heating the material to a temperature below its melting point, allowing atoms to diffuse across particle boundaries and fuse together, resulting in a solid, cohesive mass.
Key Points Explained:
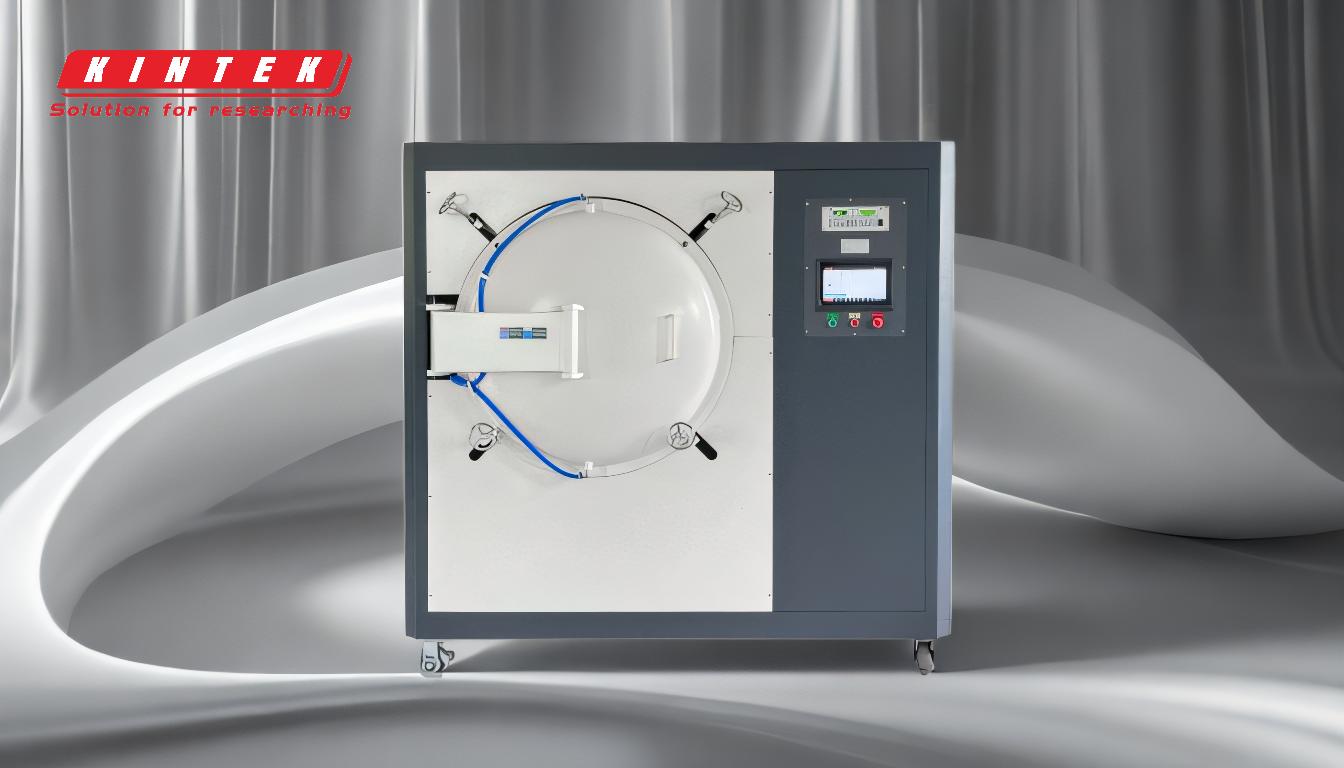
-
Definition of Sintering in Dentistry:
- Sintering is a manufacturing process used in dentistry to compact and form solid dental materials by applying heat and pressure.
- It does not involve melting the material to the point of liquefaction but instead relies on atomic diffusion to fuse particles together.
- This process is essential for creating dental restorations like crowns, bridges, and implants that are strong, durable, and biocompatible.
-
How Sintering Works:
- Sintering involves heating powdered or porous dental materials to a specific temperature below their melting point.
- The heat causes atoms to diffuse across the boundaries of the particles, creating strong bonds and forming a dense, solid mass.
- The process typically includes three stages: heating, holding at the sintering temperature, and cooling to achieve the desired properties.
-
Materials Used in Dental Sintering:
- Common materials include ceramics (e.g., zirconia) and metal alloys (e.g., cobalt-chromium, titanium).
- These materials are chosen for their high melting points, biocompatibility, and ability to withstand the mechanical stresses of dental applications.
-
Applications of Sintering in Dentistry:
- Dental Crowns and Bridges: Sintering is used to create strong, durable, and aesthetically pleasing restorations that match the natural teeth.
- Dental Implants: Sintered materials provide the structural integrity needed for implants to integrate with the jawbone.
- Orthodontic Appliances: Sintering is used to manufacture brackets and other orthodontic components that require high strength and precision.
-
Advantages of Sintering in Dental Materials:
- Enhanced Strength and Durability: Sintering creates a dense, cohesive structure that is stronger than the original powdered material.
- Biocompatibility: Sintered materials are safe for use in the human body, making them ideal for dental applications.
- Precision and Customization: The process allows for the creation of highly accurate and customized dental restorations that fit perfectly in the patient's mouth.
-
Challenges in Dental Sintering:
- Temperature Control: Maintaining the correct sintering temperature is crucial to avoid melting or incomplete fusion.
- Material Shrinkage: Sintering can cause materials to shrink, which must be accounted for during the design and manufacturing process.
- Time-Consuming: The sintering process can be time-consuming, especially for complex dental restorations.
-
Future Trends in Dental Sintering:
- Advanced Materials: Research is ongoing to develop new materials with improved properties, such as higher strength and better aesthetics.
- Automation and Digitalization: The use of digital technologies, such as CAD/CAM systems, is increasing, allowing for more precise and efficient sintering processes.
- Sustainability: Efforts are being made to reduce the environmental impact of sintering by using more sustainable materials and energy-efficient processes.
In summary, sintering dental materials is a vital process that enhances the strength, durability, and biocompatibility of dental restorations. By applying heat and pressure without melting, sintering creates dense, cohesive structures that are essential for high-quality dental care. The process is widely used in the production of crowns, bridges, implants, and orthodontic appliances, offering numerous advantages while also presenting some challenges that require careful management. As technology advances, the future of dental sintering looks promising, with new materials and processes on the horizon.
Summary Table:
Aspect | Details |
---|---|
Definition | Process of compacting dental materials using heat and pressure without melting. |
Key Materials | Ceramics (e.g., zirconia), metal alloys (e.g., cobalt-chromium, titanium). |
Applications | Crowns, bridges, implants, orthodontic appliances. |
Advantages | Enhanced strength, biocompatibility, precision, and customization. |
Challenges | Temperature control, material shrinkage, time-consuming process. |
Future Trends | Advanced materials, automation, digitalization, and sustainability. |
Discover how sintering can improve your dental restorations—contact our experts today!