A hydraulic press is a powerful machine capable of exerting immense force, often used in industrial applications to compress, mold, or break materials. However, there are certain materials and objects that a hydraulic press cannot break due to their unique properties, such as extreme hardness, flexibility, or resilience. For instance, materials like graphene, diamond, or certain high-performance composites can resist the force of a hydraulic press. Additionally, objects with specific structural designs, such as those made from advanced ceramics or reinforced with carbon fibers, may also withstand the pressure. Understanding these limitations is crucial for equipment purchasers to ensure they select the right tools for their specific needs.
Key Points Explained:
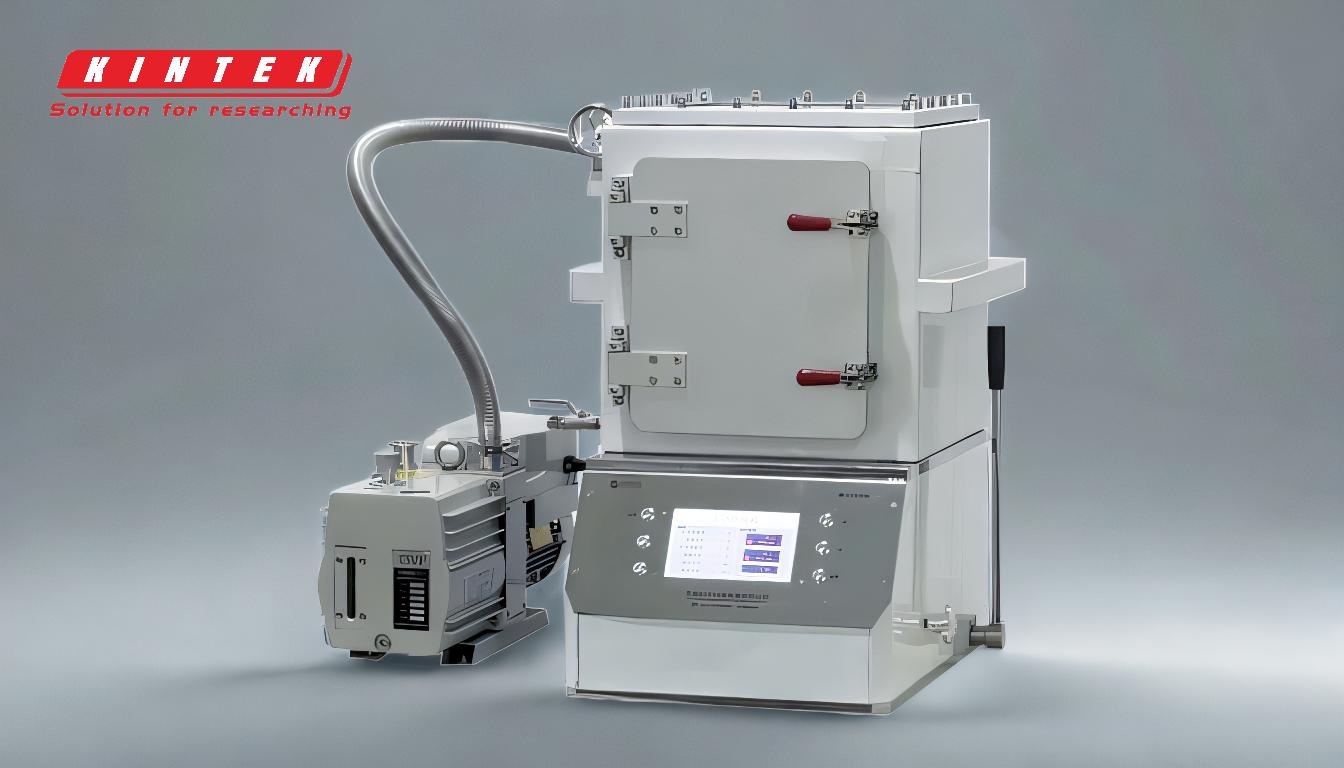
-
Materials with Extreme Hardness
- Materials like diamonds and graphene are among the hardest substances known. Their atomic structure makes them highly resistant to deformation or breaking under pressure.
- Diamonds, for example, have a tightly bonded carbon lattice that can withstand immense compressive forces.
- Graphene, a single layer of carbon atoms arranged in a hexagonal lattice, is incredibly strong and flexible, making it nearly impossible for a hydraulic press to break.
- These materials are often used in high-performance applications where durability is critical.
-
High-Performance Composites
- Composites like carbon fiber-reinforced polymers (CFRP) are designed to combine strength and lightweight properties.
- The fibers in these materials distribute stress evenly, preventing localized failure even under high pressure.
- A hydraulic hot press machine might struggle to break such composites because the materials are engineered to resist compression and shear forces.
- These composites are commonly used in aerospace, automotive, and sporting goods industries.
-
Advanced Ceramics
- Ceramics like silicon carbide or alumina are known for their hardness and thermal stability.
- They are often used in applications requiring resistance to wear, heat, and pressure.
- While ceramics can be brittle, their hardness makes them difficult to break with a hydraulic press unless subjected to precise, localized force.
- Their use in cutting tools, armor, and industrial machinery highlights their durability.
-
Flexible and Resilient Materials
- Some materials, like certain elastomers or polymers, are designed to absorb and distribute force rather than break.
- For example, rubber or polyurethane can deform under pressure but return to their original shape, making them resistant to breaking.
- These materials are often used in shock absorbers, seals, and protective gear.
-
Structural Design Factors
- The design of an object can also determine its resistance to a hydraulic press.
- Objects with reinforced structures, such as honeycomb designs or layered composites, can distribute force more effectively.
- Even if the individual materials are not exceptionally hard, the overall structure can prevent failure under pressure.
- This principle is often applied in engineering and construction to create durable and lightweight components.
-
Limitations of Hydraulic Presses
- While hydraulic presses are incredibly powerful, they have limitations based on the material properties and the design of the object being pressed.
- The force exerted by a hydraulic press is limited by its capacity, which varies depending on the model and application.
- Understanding these limitations helps equipment purchasers choose the right press for their specific needs, ensuring efficiency and safety in operations.
By considering these factors, purchasers can make informed decisions about the materials and equipment they use, ensuring optimal performance and durability in their applications.
Summary Table:
Category | Examples | Key Properties |
---|---|---|
Extreme Hardness | Diamond, Graphene | Tightly bonded atomic structures; highly resistant to deformation or breaking. |
High-Performance Composites | Carbon Fiber-Reinforced Polymers (CFRP) | Strong, lightweight, and stress-distributing fibers resist compression and shear. |
Advanced Ceramics | Silicon Carbide, Alumina | Hardness and thermal stability; resistant to wear, heat, and pressure. |
Flexible Materials | Rubber, Polyurethane | Absorb and distribute force; return to original shape after deformation. |
Structural Design | Honeycomb Structures, Layered Composites | Reinforced designs distribute force effectively, preventing failure under pressure. |
Need help selecting the right hydraulic press for your needs? Contact our experts today for personalized advice!