Sputtering equipment is a specialized tool used in the process of Physical Vapor Deposition (PVD) to deposit thin films of material onto a substrate. This process involves creating a plasma by applying a high voltage across a low-pressure gas, typically argon. The plasma ions then bombard a target material, causing atoms to be ejected and deposited onto a substrate, forming a thin film. Sputtering is widely used in industries such as electronics, optics, and semiconductor manufacturing for applications like LED displays, optical filters, and precision optics.
Key Points Explained:
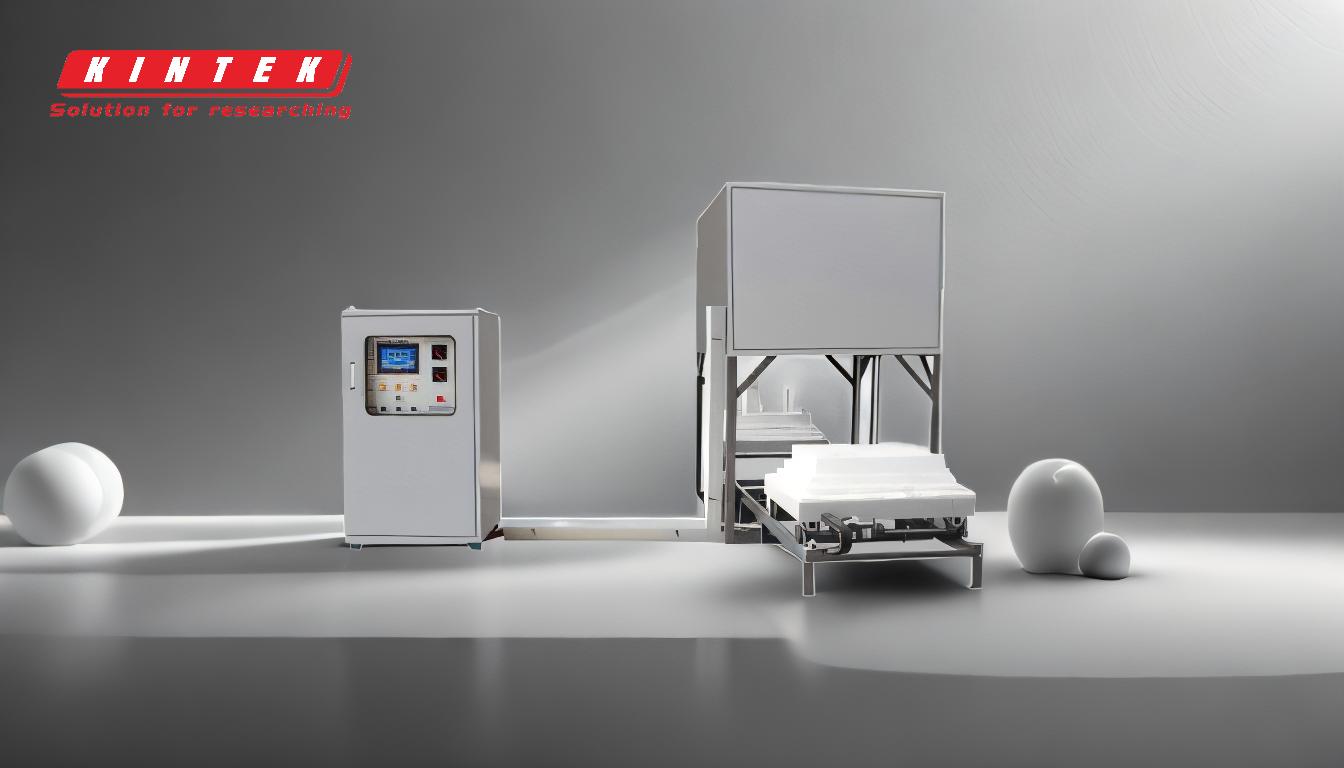
-
Basic Principle of Sputtering:
- Sputtering is a PVD technique where high-energy ions bombard a target material, causing atoms to be ejected from the target surface.
- These ejected atoms then travel through a vacuum and deposit onto a substrate, forming a thin film.
-
Role of Plasma in Sputtering:
- A high voltage is applied across a low-pressure gas (usually argon) to create a plasma.
- The plasma consists of electrons and gas ions, which are accelerated towards the target material.
- The impact of these ions on the target causes the ejection of target atoms.
-
Magnetron Sputtering:
- In magnetron sputtering, magnetic fields are used to control the movement of charged particles, enhancing the density of the plasma.
- This results in a higher deposition rate and better control over the film properties.
- The process is efficient and widely used for depositing thin films in various industrial applications.
-
Applications of Sputtering Equipment:
- LED Displays: Sputtering is used to deposit thin films that are essential for the functionality of LED displays.
- Optical Filters: The process is employed to create high-quality optical filters used in various optical devices.
- Precision Optics: Sputtering is crucial for producing the thin films needed in precision optics, ensuring high performance and durability.
-
Advantages of Sputtering:
- High-Quality Films: Sputtering produces films with excellent uniformity, adhesion, and density.
- Versatility: It can deposit a wide range of materials, including metals, alloys, and ceramics.
- Controlled Deposition: The process allows for precise control over film thickness and composition, making it suitable for complex applications.
-
Components of Sputtering Equipment:
- Vacuum Chamber: Maintains the low-pressure environment necessary for the sputtering process.
- Target Material: The material to be deposited, which is bombarded by plasma ions.
- Substrate Holder: Holds the substrate where the thin film will be deposited.
- Power Supply: Provides the high voltage needed to create the plasma.
- Magnetic Fields (in Magnetron Sputtering): Enhance plasma density and control particle behavior.
-
Process Control and Optimization:
- Pressure Control: Maintaining the correct gas pressure is crucial for stable plasma generation.
- Temperature Control: The substrate temperature can affect film properties, so it must be carefully controlled.
- Deposition Rate: Adjusting the power and magnetic fields can optimize the deposition rate for specific applications.
In summary, sputtering equipment is a vital tool in modern manufacturing, enabling the deposition of high-quality thin films for a variety of advanced applications. Its ability to produce uniform, adherent, and precise coatings makes it indispensable in industries ranging from electronics to optics.
Summary Table:
Aspect | Details |
---|---|
Basic Principle | High-energy ions bombard a target, ejecting atoms to form thin films. |
Role of Plasma | Created by high voltage in low-pressure gas, accelerating ions to the target. |
Magnetron Sputtering | Uses magnetic fields to enhance plasma density and deposition efficiency. |
Applications | LED displays, optical filters, precision optics. |
Advantages | High-quality films, versatility, controlled deposition. |
Key Components | Vacuum chamber, target material, substrate holder, power supply. |
Process Control | Pressure, temperature, and deposition rate optimization. |
Discover how sputtering equipment can elevate your manufacturing process—contact us today for expert guidance!