Sputtering is a widely used thin-film deposition technique that involves ejecting atoms from a solid target material onto a substrate to form a thin, uniform film. This process occurs in a vacuum chamber where a high voltage is applied between the chamber and a target electrode made of the desired film material. Inert gases like argon are introduced, ionized, and accelerated toward the target, causing atoms to be ejected and deposited onto the substrate. Sputtering offers precise control over film thickness, uniformity, and density, making it suitable for applications in electronics, optics, and coatings. Variations like magnetron, ion beam, and reactive sputtering enhance its versatility for specific material and application needs.
Key Points Explained:
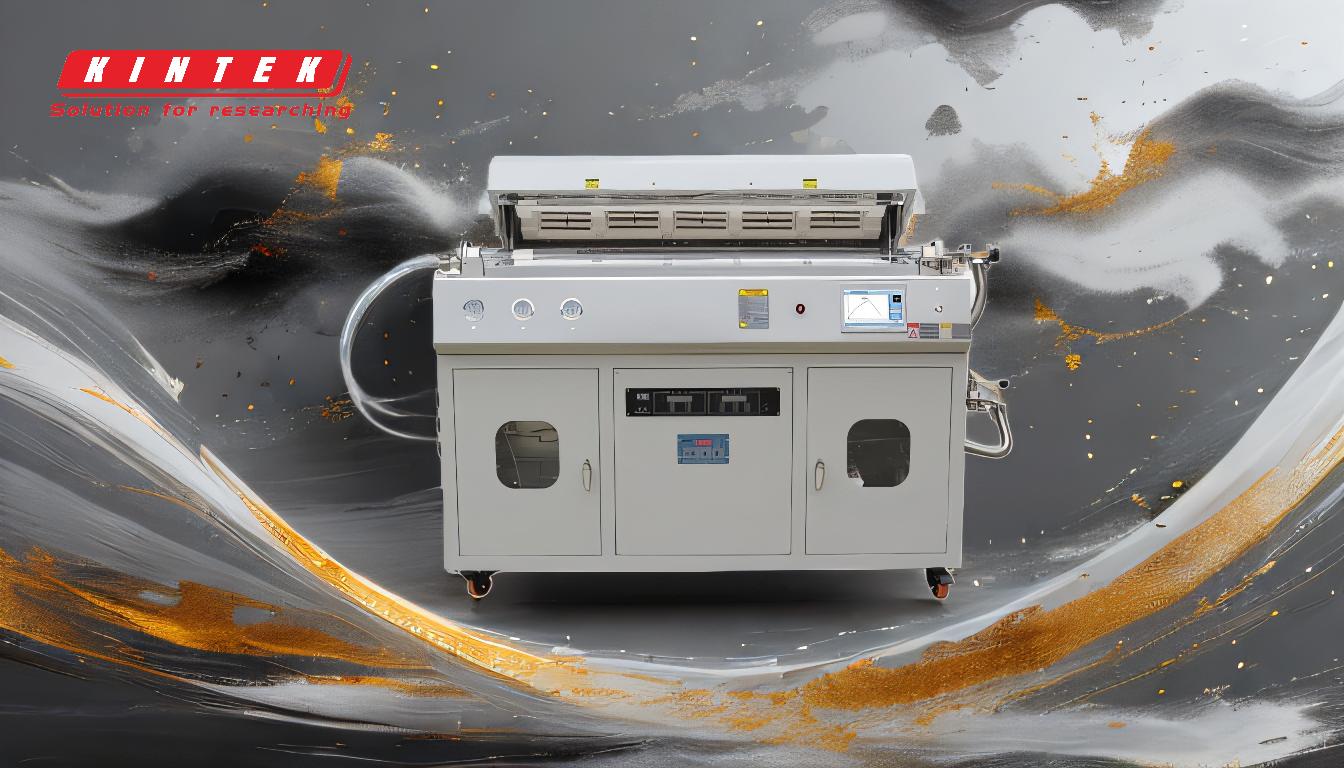
-
Basic Principle of Sputtering:
- Sputtering involves bombarding a target material (e.g., metal or ceramic) with high-energy ions, typically from an inert gas like argon.
- The ions are accelerated by a high-voltage electric field, colliding with the target and ejecting atoms from its surface.
- These ejected atoms travel through the vacuum chamber and deposit onto a substrate, forming a thin film.
-
Components of the Sputtering Process:
- Vacuum Chamber: Provides a controlled environment to minimize contamination and ensure efficient ion bombardment.
- Target Material: The source of the atoms to be deposited, made of the desired film material.
- Substrate: The surface onto which the thin film is deposited.
- Inert Gas (e.g., Argon): Ionized to create the plasma that drives the sputtering process.
- High-Voltage Power Supply: Generates the electric field necessary to accelerate ions toward the target.
-
Advantages of Sputtering:
- Uniform Deposition: Sputtering produces highly uniform thin films, even over large or complex surfaces.
- Precise Thickness Control: Film thickness can be precisely controlled by adjusting deposition time and process parameters.
- Low-Temperature Deposition: Suitable for temperature-sensitive substrates, as it can operate at lower temperatures compared to other deposition methods.
- Material Versatility: Can deposit a wide range of materials, including metals, alloys, and ceramics.
-
Types of Sputtering Techniques:
- Magnetron Sputtering: Uses magnetic fields to confine electrons near the target, increasing ionization efficiency and deposition rates.
- Ion Beam Sputtering: Employs a focused ion beam to sputter the target, offering high precision and control for specialized applications.
- Reactive Sputtering: Introduces reactive gases (e.g., oxygen or nitrogen) to form compound films like oxides or nitrides during deposition.
- Ion-Assisted Sputtering: Combines ion bombardment with sputtering to improve film adhesion and density.
- Gas Flow Sputtering: Utilizes gas flow to enhance the transport of sputtered atoms to the substrate.
-
Applications of Sputtering:
- Electronics: Used to deposit conductive and insulating layers in semiconductor devices, solar cells, and displays.
- Optics: Produces anti-reflective, reflective, and protective coatings for lenses, mirrors, and optical filters.
- Coatings: Applied in wear-resistant, decorative, and functional coatings for automotive parts, cookware, and tools.
- Historical Use: Thomas Edison used sputtering in 1904 to coat wax phonograph recordings with metal for mass duplication.
-
Process Control and Optimization:
- Gas Pressure and Flow Rate: Adjusted to optimize ion density and deposition rate.
- Power Supply Parameters: Controlled to regulate ion energy and sputtering efficiency.
- Substrate Temperature: Managed to influence film properties like stress and adhesion.
- Target-to-Substrate Distance: Optimized to ensure uniform deposition and minimize defects.
-
Challenges and Considerations:
- Residual Stress: Can occur in the deposited film, affecting its mechanical properties.
- Contamination: Requires a high-quality vacuum environment to prevent impurities.
- Target Erosion: The target material erodes over time, necessitating periodic replacement or refurbishment.
By understanding these key aspects, a purchaser of sputtering equipment or consumables can make informed decisions about the specific techniques and parameters needed for their application, ensuring optimal performance and cost-effectiveness.
Summary Table:
Key Aspect | Details |
---|---|
Basic Principle | Bombarding a target material with high-energy ions to eject atoms. |
Components | Vacuum chamber, target material, substrate, inert gas, high-voltage supply. |
Advantages | Uniform deposition, precise thickness control, low-temperature operation. |
Techniques | Magnetron, ion beam, reactive, ion-assisted, and gas flow sputtering. |
Applications | Electronics, optics, coatings, and historical uses like phonograph records. |
Challenges | Residual stress, contamination, and target erosion. |
Ready to optimize your thin-film deposition process? Contact our experts today for tailored sputtering solutions!