Temperature control in resistance furnaces is a critical aspect of ensuring precise and efficient heating processes. It involves regulating the heat generated by the furnace to maintain a desired temperature range. This is achieved through various methods, such as adjusting the voltage supplied to the heating elements, modifying the resistance of the elements, or controlling the on/off cycles of the power supply. Advanced techniques like programmable temperature controllers and feedback-based automatic control systems further enhance precision, especially in applications like heat treatment under inert atmospheres. The control mechanisms can range from simple on/off switches to sophisticated proportional-integral-derivative (PID) systems, depending on the furnace's design and application requirements.
Key Points Explained:
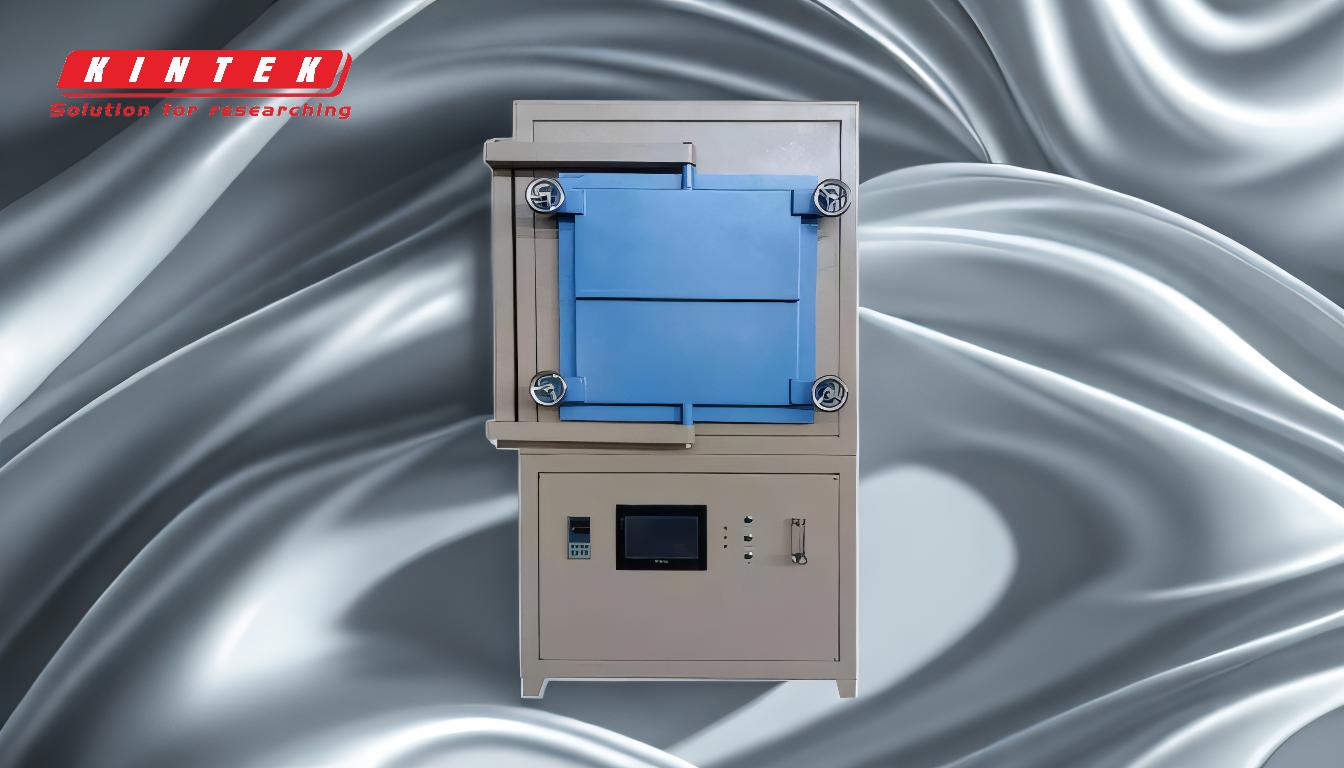
-
Principles of Temperature Control in Resistance Furnaces:
- Temperature control is achieved by manipulating the heat source energy, which is directly related to the electrical energy supplied to the heating elements.
- The primary methods include:
- Voltage Control: Adjusting the voltage supplied to the heating elements using transformers, auto-transformers, or induction regulators.
- Resistance Control: Varying the resistance of the heating elements to regulate heat generation.
- On/Off Control: Modulating the ratio of on and off times of the power supply to maintain the desired temperature.
-
Automatic Temperature Control Systems:
- These systems use feedback mechanisms to compare the actual furnace temperature with the desired temperature and adjust the heat source accordingly.
- Common control methods include:
- Two-Position Control: The heat source is turned on or off based on temperature thresholds.
- Proportional Control: The heat source energy is adjusted proportionally to the temperature deviation.
- PID Control: Combines proportional, integral, and derivative actions to achieve precise and stable temperature regulation.
-
Programmable Temperature Controllers:
- These controllers allow for precise control of heating and cooling rates, making them ideal for applications requiring strict temperature profiles, such as heat treatment in inert atmospheres.
- They enable users to set specific temperature ramps, dwell times, and cooling rates, ensuring consistent and repeatable results.
-
Types of Resistance Furnaces and Their Temperature Ranges:
- Resistance furnaces are categorized based on their maximum operating temperatures and the heating elements used.
- Examples include:
- Box Resistance Furnace: Operates below 1200°C, with variations up to 1800°C depending on the heating elements (e.g., resistance wire, silicon carbide rod, or silicon molybdenum rod).
- Muffle Furnace: Uses automatic temperature control to maintain precise temperature ranges for specific applications.
-
Applications and Benefits of Precise Temperature Control:
- Precise temperature control is essential in industries such as metallurgy, ceramics, and materials science, where specific thermal profiles are required for processes like annealing, sintering, and heat treatment.
- Benefits include improved product quality, energy efficiency, and process repeatability.
-
Resistance Heating Principle:
- Resistance heating relies on the principle that electrical resistance in a conductor generates heat when current flows through it.
- This heat is produced as electrons collide with atoms in the material, transferring kinetic energy as thermal energy.
By understanding these key points, equipment and consumable purchasers can make informed decisions about selecting the right resistance furnace and control systems for their specific needs, ensuring optimal performance and efficiency.
Summary Table:
Aspect | Details |
---|---|
Control Methods | Voltage control, resistance control, on/off control |
Automatic Systems | Two-position, proportional, and PID control for precise temperature regulation |
Programmable Controllers | Set temperature ramps, dwell times, and cooling rates for specific profiles |
Furnace Types | Box resistance furnace (up to 1800°C), muffle furnace with automatic control |
Applications | Heat treatment, annealing, sintering in metallurgy, ceramics, and materials science |
Benefits | Improved product quality, energy efficiency, and process repeatability |
Discover how precise temperature control can optimize your processes—contact our experts today!