Heat treatment is a widely used process in manufacturing and material science to alter the physical and mechanical properties of materials, particularly metals like steel. It offers numerous advantages, such as improving strength, flexibility, wear resistance, and machinability, while also enhancing electrical and magnetic properties. However, it also has some disadvantages, including potential material distortion, increased costs, and the need for precise control to avoid defects. Understanding both the benefits and drawbacks is crucial for making informed decisions in material selection and manufacturing processes.
Key Points Explained:
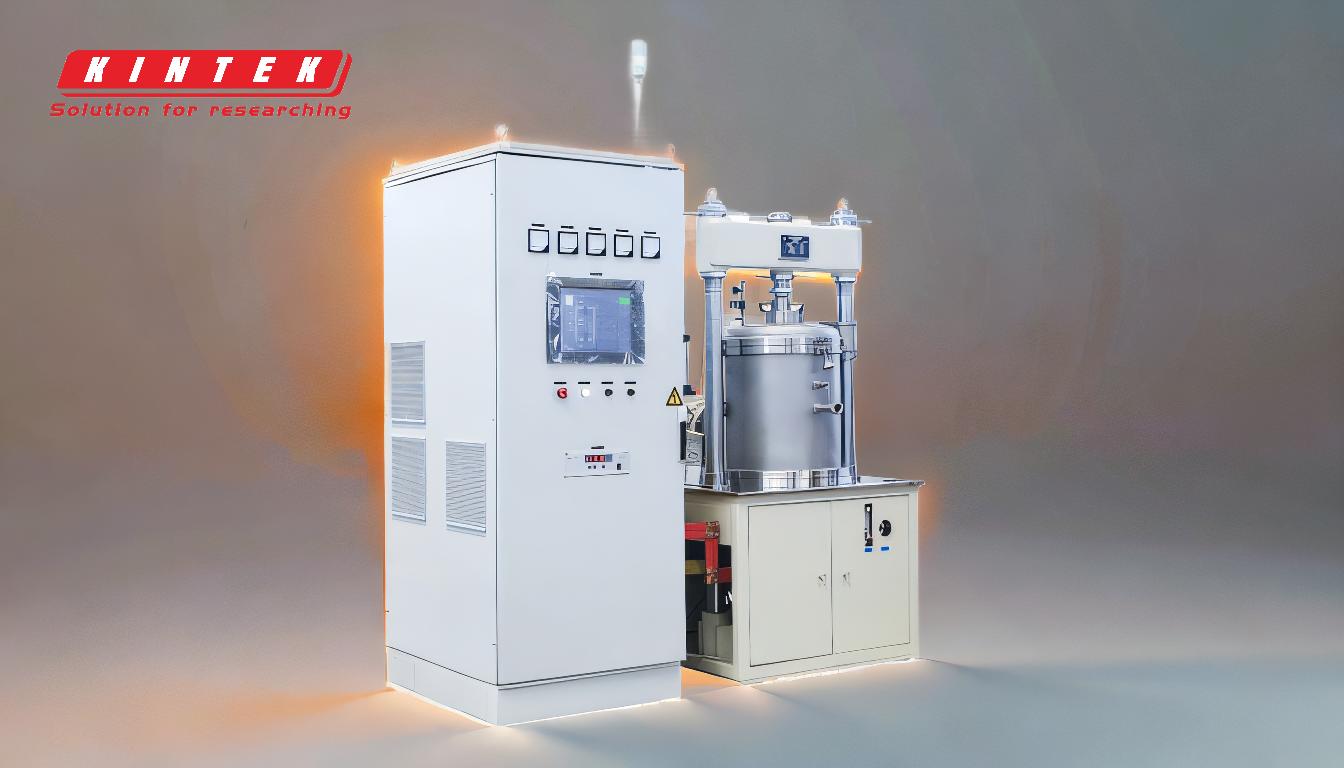
-
Advantages of Heat Treatment:
-
Improved Material Properties:
- Heat treatment can significantly enhance the physical and mechanical properties of materials. For example, it can increase hardness, strength, and wear resistance, making materials more durable and suitable for demanding applications.
-
Stress Relief:
- The process helps relieve internal stresses in materials, which can occur during manufacturing processes like welding or machining. This stress relief makes parts easier to work with and reduces the risk of failure.
-
Enhanced Flexibility and Toughness:
- Heat treatment can improve the flexibility and toughness of materials, making them less brittle and more resistant to impact and fatigue.
-
Improved Machinability and Weldability:
- By altering the microstructure of materials, heat treatment can make them easier to machine or weld, which is particularly beneficial in manufacturing processes.
-
Enhanced Electrical and Magnetic Properties:
- Certain heat treatment processes can improve the electrical conductivity and magnetic properties of materials, making them suitable for specialized applications in electronics and electrical engineering.
-
Improved Material Properties:
-
Disadvantages of Heat Treatment:
-
Material Distortion:
- One of the primary disadvantages of heat treatment is the potential for material distortion or warping. This can occur due to uneven heating or cooling, leading to dimensional inaccuracies in the final product.
-
Increased Costs:
- Heat treatment can be an expensive process due to the need for specialized equipment, energy consumption, and skilled labor. These costs can add up, especially for large-scale production.
-
Precision and Control Requirements:
- The process requires precise control of temperature, time, and cooling rates to achieve the desired material properties. Any deviation can result in defects or suboptimal performance.
-
Potential for Surface Oxidation:
- During heat treatment, materials can be exposed to high temperatures in the presence of oxygen, leading to surface oxidation or scaling. This can affect the material's surface finish and require additional post-treatment processes.
-
Limited Applicability to Certain Materials:
- Not all materials respond well to heat treatment. For example, some non-ferrous metals and certain alloys may not achieve the desired properties through heat treatment, limiting its applicability.
-
Material Distortion:
-
Applications and Considerations:
-
Steel and Metal Manufacturing:
- Heat treatment is particularly beneficial for steel and other metals used in manufacturing processes like hot forming, welding, and machining. It helps improve the material's performance and longevity in these applications.
-
Specialized Applications:
- In industries like aerospace, automotive, and electronics, heat treatment is used to create materials with specific properties tailored to the demands of these sectors.
-
Quality Control:
- Ensuring the quality of heat-treated materials requires rigorous testing and inspection to verify that the desired properties have been achieved without introducing defects.
-
Steel and Metal Manufacturing:
In conclusion, heat treatment offers significant advantages in enhancing material properties and performance, but it also comes with challenges such as cost, precision requirements, and potential material distortion. Understanding these factors is essential for leveraging the benefits of heat treatment while mitigating its drawbacks in various industrial applications.
Summary Table:
Aspect | Advantages | Disadvantages |
---|---|---|
Material Properties | Enhances hardness, strength, wear resistance, and durability | Potential material distortion or warping |
Stress Relief | Reduces internal stresses, improving workability and reducing failure risks | Increased costs due to equipment, energy, and skilled labor |
Flexibility/Toughness | Improves flexibility and toughness, reducing brittleness | Requires precise control of temperature, time, and cooling rates |
Machinability | Enhances machinability and weldability for manufacturing processes | Risk of surface oxidation or scaling during treatment |
Electrical/Magnetic | Improves electrical conductivity and magnetic properties for specialized uses | Limited applicability to certain materials, such as non-ferrous metals and alloys |
Want to optimize your material performance with heat treatment? Contact our experts today!