Hot press forming, a process facilitated by a hot press machine, offers numerous advantages in manufacturing, particularly in industries requiring high-strength, lightweight components. This method involves heating materials to a specific temperature and then pressing them into the desired shape using a mold. The process is widely used in automotive, aerospace, and construction industries due to its ability to produce parts with superior mechanical properties and dimensional accuracy. By leveraging the heat and pressure applied during hot press forming, manufacturers can achieve complex geometries, reduce material waste, and enhance the overall performance of the final product. This method also allows for the use of advanced materials, such as high-strength steels and composites, which are difficult to form using traditional methods.
Key Points Explained:
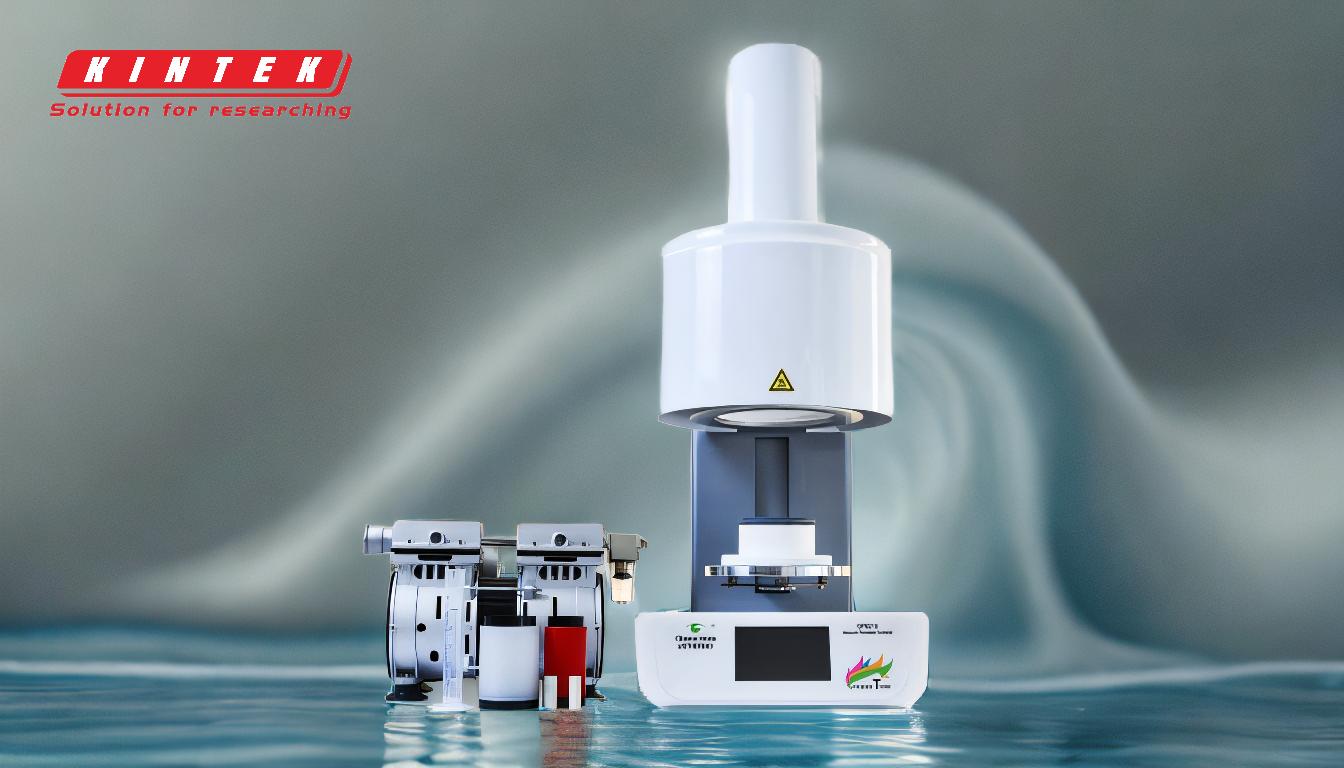
-
Enhanced Material Properties:
- Hot press forming significantly improves the mechanical properties of materials, such as tensile strength and hardness. The process involves heating the material to a temperature where it becomes more malleable, allowing it to be shaped without cracking or breaking. Once cooled, the material retains its new shape and exhibits enhanced strength due to the formation of a martensitic microstructure, particularly in high-strength steels.
-
Improved Dimensional Accuracy:
- The use of a hot press machine ensures that the final product has high dimensional accuracy and consistency. The molds used in the process are precisely engineered, and the controlled application of heat and pressure minimizes distortions and variations. This is crucial for industries like automotive manufacturing, where tight tolerances are required for components to fit together perfectly.
-
Complex Geometries:
- Hot press forming allows for the creation of complex shapes and intricate designs that would be difficult or impossible to achieve with traditional cold forming methods. The ability to form materials at high temperatures means that they can be molded into more detailed and sophisticated geometries, which is particularly beneficial for lightweight and aerodynamic components in the aerospace industry.
-
Reduced Material Waste:
- The process is highly efficient, with minimal material waste compared to other forming techniques. Since the material is heated and formed in a single step, there is less need for secondary machining or finishing processes, which can generate significant waste. This efficiency not only reduces costs but also aligns with sustainability goals by minimizing the environmental impact of manufacturing.
-
Use of Advanced Materials:
- Hot press forming is compatible with a wide range of advanced materials, including high-strength steels, aluminum alloys, and composites. These materials are often challenging to work with using traditional methods due to their high strength and low formability. However, the high temperatures used in hot press forming make these materials more pliable, allowing for the production of lightweight yet strong components.
-
Cost-Effectiveness:
- While the initial investment in a hot press machine and molds can be high, the overall cost-effectiveness of the process is significant. The reduction in material waste, the ability to produce complex parts in a single step, and the improved mechanical properties of the final product all contribute to lower production costs over time. Additionally, the durability and performance of hot-pressed components often result in longer service life, further enhancing cost savings.
-
Applications in Key Industries:
- The advantages of hot press forming make it particularly valuable in industries such as automotive, aerospace, and construction. In the automotive industry, for example, hot-pressed components are used in safety-critical parts like door beams and bumper reinforcements, where high strength and lightweight properties are essential. In aerospace, the ability to produce complex, lightweight components is crucial for improving fuel efficiency and performance.
In summary, hot press forming, facilitated by a hot press machine, offers a range of benefits that make it an attractive option for manufacturers looking to produce high-strength, lightweight, and complex components. The process enhances material properties, improves dimensional accuracy, allows for the creation of intricate geometries, reduces material waste, and is compatible with advanced materials. These advantages, combined with cost-effectiveness and broad industry applications, make hot press forming a highly valuable manufacturing technique.
Summary Table:
Advantage | Description |
---|---|
Enhanced Material Properties | Improves tensile strength, hardness, and durability through precise heat and pressure. |
Improved Dimensional Accuracy | Ensures high precision and consistency, ideal for tight-tolerance industries. |
Complex Geometries | Enables intricate designs and lightweight components for aerospace and automotive. |
Reduced Material Waste | Minimizes waste with efficient single-step forming, aligning with sustainability goals. |
Use of Advanced Materials | Compatible with high-strength steels, aluminum alloys, and composites. |
Cost-Effectiveness | Lowers production costs through reduced waste, durability, and efficiency. |
Industry Applications | Widely used in automotive, aerospace, and construction for high-performance parts. |
Ready to enhance your manufacturing process? Contact us today to learn more about hot press forming!