Furnace brazing, particularly using a vacuum brazing furnace, offers numerous advantages, making it a preferred method for joining metal components in industries like aerospace, particle physics, and metallurgical research. The process involves heating assemblies in a controlled environment to melt and flow a filler metal into joints, creating strong, contamination-free bonds. Key benefits include uniform temperature distribution, precise control, low contamination, and the ability to join complex or unweldable materials. Additionally, vacuum brazing prevents oxidation and thermal distortion, ensuring high-quality, repeatable results. This method is ideal for applications requiring precision, scalability, and environmental cleanliness.
Key Points Explained:
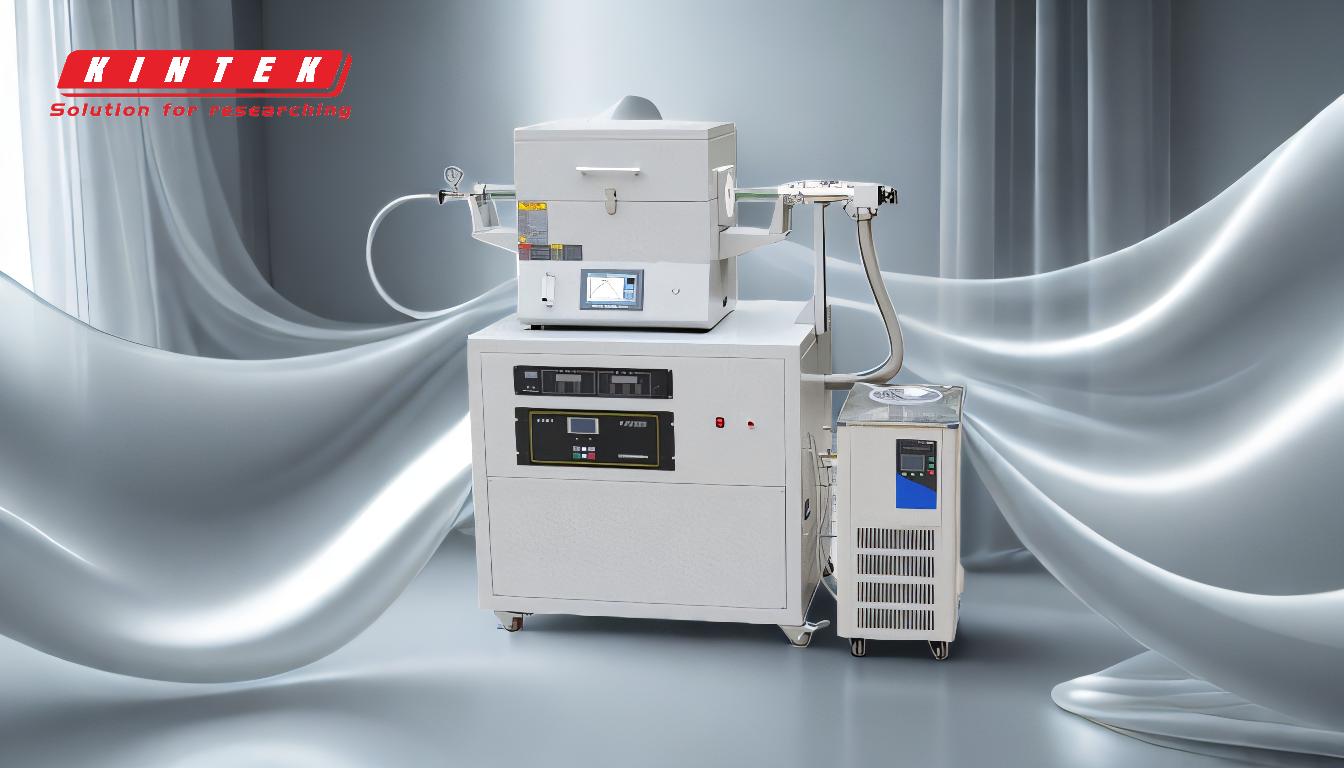
-
Uniform Temperature Distribution:
- Vacuum brazing furnaces provide uniform temperatures within the range of 1100–1500°C (2000–2800°F), ensuring consistent heating across the entire assembly. This uniformity is critical for achieving strong, reliable joints, especially in large or complex parts.
-
Precise Temperature Control:
- The furnace offers precise temperature control within a small area, allowing for accurate heating cycles. This precision is essential for maintaining the integrity of the base materials and ensuring the filler metal flows correctly into the joints.
-
Low Contamination:
- Operating in a vacuum environment eliminates exposure to carbon, oxygen, and other gases, preventing contamination. This is particularly important for reactive materials that would otherwise form oxide layers, compromising the joint quality.
-
Oxide Layer Removal:
- The furnace operates at temperatures higher than oxide formation, enabling oxidized pieces to lose their oxide layer before brazing. This ensures a clean surface for the filler metal to bond effectively.
-
Scalability and Repeatability:
- Furnace brazing allows for the simultaneous creation of thousands of joints, making it highly scalable. The process is computer-controlled, ensuring metallurgical repeatability and consistent results across multiple batches.
-
Joining Unweldable Materials:
- Vacuum brazing can join materials that are difficult or impossible to weld, expanding the range of applications. This capability is particularly valuable in industries like aerospace, where advanced materials are often used.
-
Prevention of Thermal Distortion:
- The controlled heating and cooling process minimizes thermal distortion, which is a common issue in other metal joining methods. This ensures that the final product retains its intended dimensions and properties.
-
Environmental Benefits:
- Vacuum brazing is a clean process with minimal environmental pollution. The absence of fluxes and the controlled atmosphere reduce waste and ensure a clean, smooth surface finish.
-
Sophisticated Cycle Programming:
- The furnace features advanced cycle programming, including barcode-linked programs for recognizing workpieces. This automation reduces human error and ensures precise heating cycles tailored to each piece.
-
Applications in High-Tech Industries:
- Vacuum brazing furnaces are designed to meet stringent requirements in industries like aerospace and particle physics. They comply with standards like NADCAP, ensuring high-quality results for critical applications.
In summary, furnace brazing, especially with a vacuum brazing furnace, offers unparalleled advantages in terms of precision, cleanliness, and scalability. Its ability to handle complex designs, prevent contamination, and ensure repeatability makes it an indispensable tool for modern manufacturing and research.
Summary Table:
Advantage | Description |
---|---|
Uniform Temperature Distribution | Ensures consistent heating across the assembly, ideal for large or complex parts. |
Precise Temperature Control | Accurate heating cycles maintain material integrity and ensure proper filler metal flow. |
Low Contamination | Vacuum environment prevents exposure to gases, ensuring clean, contamination-free joints. |
Oxide Layer Removal | High temperatures remove oxide layers, enabling effective bonding of filler metal. |
Scalability and Repeatability | Computer-controlled process allows for thousands of joints with consistent, repeatable results. |
Joining Unweldable Materials | Capable of bonding materials that are difficult or impossible to weld. |
Prevention of Thermal Distortion | Minimizes distortion, ensuring the final product retains its intended dimensions. |
Environmental Benefits | Clean process with minimal pollution, reducing waste and ensuring smooth surface finishes. |
Sophisticated Cycle Programming | Advanced automation reduces errors and ensures precise, tailored heating cycles. |
Applications in High-Tech Industries | Meets stringent standards like NADCAP, ideal for aerospace, particle physics, and metallurgical research. |
Ready to enhance your manufacturing process with furnace brazing? Contact our experts today to learn more!