Induction brazing is a highly efficient and precise method for joining metals, offering numerous advantages over traditional brazing techniques. It uses electromagnetic induction to generate heat directly within the workpiece, ensuring localized heating and minimal thermal distortion. This method is particularly beneficial for high-precision applications, as it provides excellent control over the heating process, resulting in clean, flux-free joints with superior strength and consistency. Induction brazing is also faster, more energy-efficient, and environmentally friendly compared to torch or furnace brazing, making it ideal for industries requiring high-quality, repeatable results.
Key Points Explained:
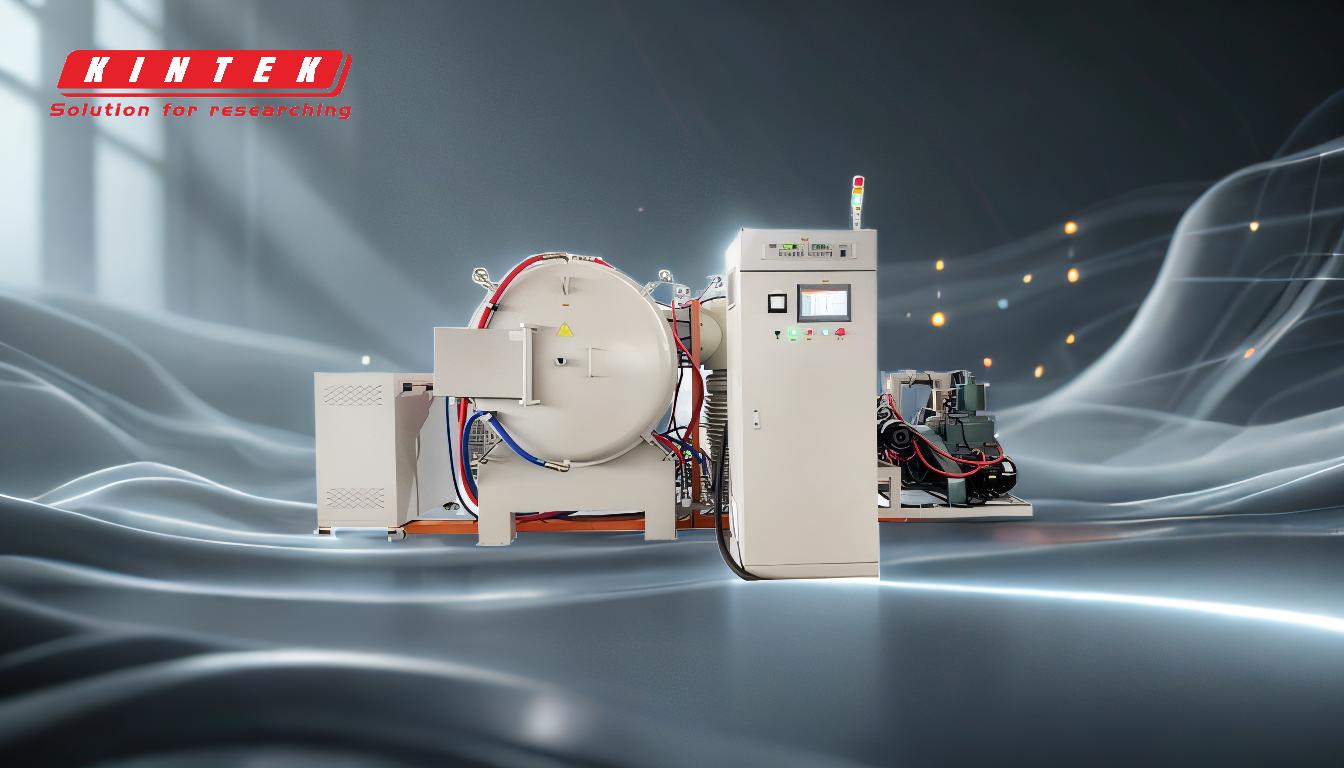
-
Localized Heating and Minimal Distortion:
- Induction brazing heats only the specific area where the joint is required, reducing the risk of thermal distortion in the surrounding material. This precision is especially critical for delicate or complex assemblies where maintaining dimensional accuracy is essential.
-
Clean, Flux-Free Joints:
- Unlike traditional methods that may require flux to prevent oxidation, induction brazing often eliminates the need for flux. This results in cleaner joints free from contaminants, reducing the need for post-processing and ensuring a more aesthetically pleasing finish.
-
Superior Joint Strength and Consistency:
- The controlled heating process of induction brazing ensures uniform temperature distribution, leading to stronger and more consistent joints. This is particularly important for industries like aerospace and medical, where joint integrity is critical.
-
Energy Efficiency and Speed:
- Induction brazing is faster than other methods, such as torch or furnace brazing, because it directly heats the workpiece. This efficiency translates to lower energy consumption and reduced production time, making it a cost-effective solution for high-volume manufacturing.
-
Versatility in Material Compatibility:
- Induction brazing can join a wide range of materials, including dissimilar metals and ceramics. This versatility makes it suitable for complex applications where traditional brazing methods may fall short.
-
Repeatability and Process Control:
- The process offers precise control over heating and cooling cycles, ensuring repeatable results. This is crucial for industries requiring tight tolerances and consistent product quality.
-
Environmental and Safety Benefits:
- Since induction brazing often eliminates the need for flux, it reduces the release of harmful fumes and residues. This makes it a safer and more environmentally friendly option compared to flux-based brazing techniques.
-
Cost-Effectiveness:
- The combination of faster processing times, reduced material waste, and lower energy consumption makes induction brazing a cost-effective choice for many manufacturers. Additionally, it requires less operator skill, further reducing labor costs.
By leveraging these advantages, induction brazing stands out as a superior method for achieving high-quality, reliable, and efficient metal joining in various industrial applications.
Summary Table:
Advantage | Description |
---|---|
Localized Heating | Heats only the joint area, minimizing thermal distortion. |
Clean, Flux-Free Joints | Eliminates the need for flux, reducing contaminants and post-processing. |
Superior Joint Strength | Ensures uniform temperature for stronger, consistent joints. |
Energy Efficiency and Speed | Faster process with lower energy consumption, ideal for high-volume production. |
Material Versatility | Joins dissimilar metals and ceramics, suitable for complex applications. |
Repeatability and Control | Precise heating and cooling cycles for consistent, high-quality results. |
Environmental and Safety | Reduces harmful fumes and residues, making it eco-friendly and safer. |
Cost-Effectiveness | Lower energy, material waste, and labor costs for efficient manufacturing. |
Ready to enhance your metal joining process? Contact us today to learn more about induction brazing solutions!