Low Pressure Chemical Vapor Deposition (LPCVD) offers several advantages over Atmospheric Pressure Chemical Vapor Deposition (APCVD), primarily due to the reduced pressure environment in which it operates. This method allows for better control over film uniformity, higher purity of deposited materials, and improved step coverage on complex geometries. LPCVD is particularly beneficial in semiconductor manufacturing and other high-precision industries where film quality and consistency are critical. The reduced pressure minimizes unwanted gas-phase reactions, leading to more precise and controlled deposition processes. Additionally, LPCVD systems often produce films with lower defect densities and better adhesion, making them suitable for advanced applications requiring high-performance coatings.
Key Points Explained:
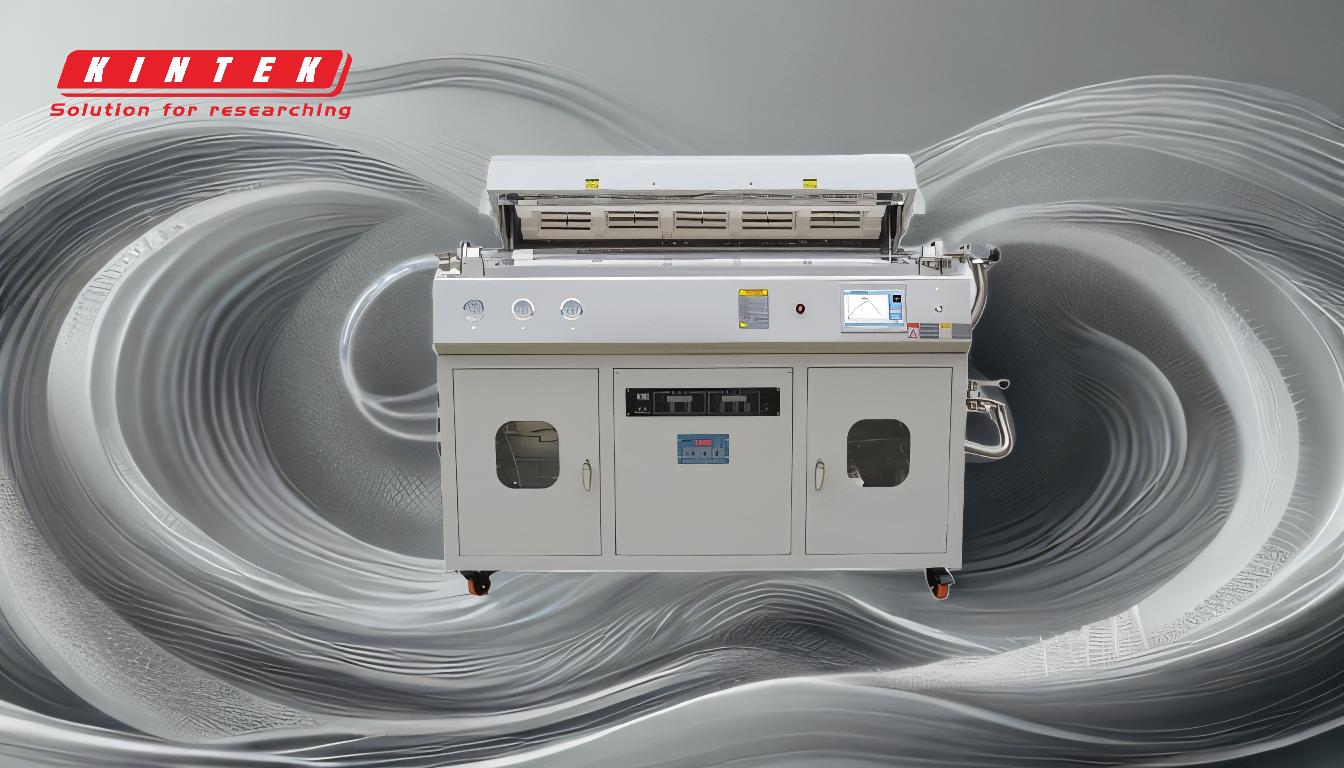
-
Improved Film Uniformity and Thickness Control:
- LPCVD operates at lower pressures, which reduces the mean free path of gas molecules. This allows for more uniform deposition across the substrate, even on complex geometries. The controlled environment ensures consistent film thickness, which is crucial for applications in semiconductor manufacturing and microelectronics.
-
Higher Purity and Lower Defect Density:
- The reduced pressure in LPCVD minimizes gas-phase reactions that can lead to impurities and defects. This results in films with higher purity and fewer defects, which is essential for high-performance applications such as integrated circuits and optical coatings.
-
Better Step Coverage on Complex Surfaces:
- LPCVD excels at coating intricate and three-dimensional surfaces due to its ability to penetrate deep trenches and vias. This is particularly important in semiconductor devices, where uniform coverage of complex structures is required for reliable performance.
-
Reduced Gas-Phase Reactions:
- At lower pressures, gas-phase reactions are minimized, leading to a more controlled deposition process. This reduces the formation of unwanted by-products and ensures that the deposition occurs primarily on the substrate surface, improving the quality of the final product.
-
Enhanced Adhesion and Film Density:
- Films deposited using LPCVD typically exhibit better adhesion to the substrate and higher density. This results in more durable coatings that can withstand harsh environments, making LPCVD suitable for applications requiring long-term reliability.
-
Scalability and Reproducibility:
- LPCVD processes are highly scalable and reproducible, making them ideal for industrial applications. The controlled environment allows for consistent results across large batches, which is critical for mass production in industries such as electronics and aerospace.
-
Lower Operating Temperatures:
- In some cases, LPCVD can achieve high-quality films at lower temperatures compared to APCVD. This is beneficial for temperature-sensitive substrates and can reduce energy consumption during the deposition process.
-
Versatility in Material Deposition:
- LPCVD can deposit a wide range of materials, including metals, ceramics, and semiconductors, with high precision. This versatility makes it a preferred choice for advanced applications in nanotechnology, photovoltaics, and MEMS (Micro-Electro-Mechanical Systems).
In summary, LPCVD offers significant advantages over APCVD, particularly in terms of film quality, uniformity, and control. These benefits make it a preferred method for high-precision applications where performance and reliability are paramount.
Summary Table:
Advantage | Description |
---|---|
Improved Film Uniformity | Ensures consistent film thickness, even on complex geometries. |
Higher Purity and Lower Defects | Minimizes gas-phase reactions, resulting in fewer impurities and defects. |
Better Step Coverage | Coats intricate surfaces uniformly, ideal for semiconductor devices. |
Reduced Gas-Phase Reactions | Controlled deposition process with fewer unwanted by-products. |
Enhanced Adhesion and Film Density | Produces durable coatings with better adhesion and higher density. |
Scalability and Reproducibility | Ideal for mass production with consistent results across large batches. |
Lower Operating Temperatures | Achieves high-quality films at lower temperatures, saving energy. |
Versatility in Material Deposition | Deposits metals, ceramics, and semiconductors with high precision for advanced applications. |
Interested in leveraging LPCVD for your high-precision applications? Contact our experts today to learn more!