Brazing and soldering are both metal-joining techniques, but they differ significantly in terms of strength, application, and suitability for specific tasks. Brazing is often preferred over soldering when stronger, more durable joints are required, as it does not melt the base metals and creates connections that are as strong as the base materials themselves. This makes brazing ideal for industries like automotive, HVAC, and cookware, where reliability and durability are critical. Soldering, on the other hand, is better suited for delicate or semi-permanent connections, such as in electronics, where weaker bonds are acceptable or even desirable. The choice between brazing and soldering depends on the specific requirements of the project, including joint strength, thermal considerations, and material compatibility.
Key Points Explained:
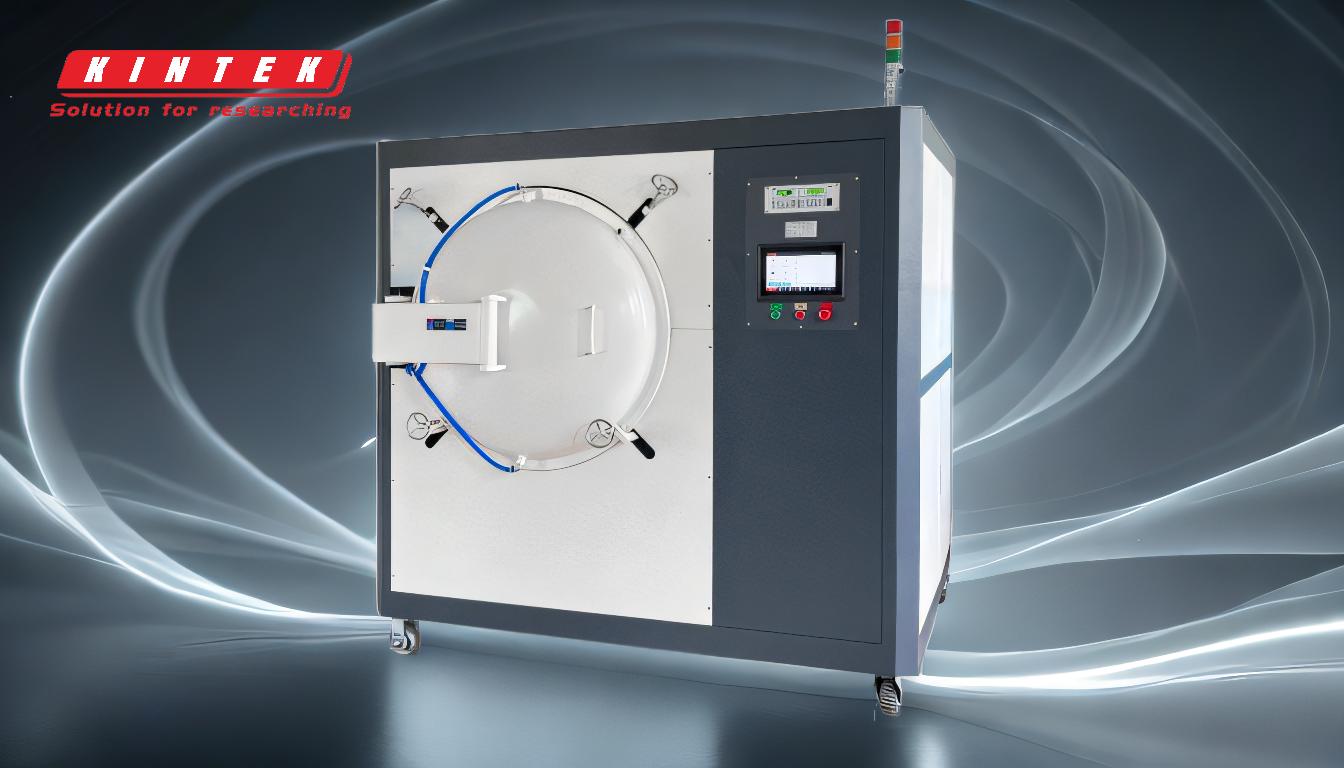
-
Base Metal Integrity:
- Brazing does not melt the base metals, which preserves their structural integrity and prevents weakening. The filler metal used in brazing solidifies to form a strong bond without altering the base materials.
- Soldering, while effective for delicate tasks, creates weaker joints because it relies on lower-temperature filler metals that do not achieve the same level of bonding strength as brazing.
-
Joint Strength:
- Brazed joints are as strong as the base metals, making them highly durable and reliable for applications requiring robust connections. This is particularly important in industries like automotive and HVAC, where joints must withstand significant stress and environmental conditions.
- Soldered joints are weaker and more suitable for applications where strength is not a primary concern, such as in electronics or temporary connections.
-
Versatility and Material Compatibility:
- Brazing can join dissimilar metals and even nonmetals, making it a versatile solution for complex assemblies. It is also cost-effective for high-volume production due to its ability to create precise, repeatable joints.
- Soldering is limited in its ability to join dissimilar materials and is generally used for simpler, smaller-scale applications.
-
Thermal Considerations:
- Brazing reduces thermal distortion compared to welding, as it operates at lower temperatures and does not melt the base metals. This makes it ideal for applications where maintaining dimensional accuracy is critical.
- Soldering operates at even lower temperatures than brazing, which minimizes the risk of thermal damage to delicate components, such as those found in electronics.
-
Applications and Industry Use:
- Brazing is widely used in industries requiring strong, durable joints, such as cookware, automotive, and HVAC systems. Its ability to create reliable connections in high-stress environments makes it a preferred choice for many manufacturers.
- Soldering is commonly used in electronics and other industries where weaker, semi-permanent connections are acceptable or even desirable. Its lower-temperature process is ideal for delicate components that could be damaged by higher heat.
By understanding these key differences, equipment and consumable purchasers can make informed decisions about which joining method is best suited for their specific needs. Brazing offers superior strength and durability, while soldering provides a gentler, more flexible solution for delicate applications.
Summary Table:
Aspect | Brazing | Soldering |
---|---|---|
Base Metal Integrity | Does not melt base metals, preserving structural integrity. | Weaker joints due to lower-temperature filler metals. |
Joint Strength | Joints as strong as base metals, ideal for high-stress applications. | Suitable for delicate or semi-permanent connections. |
Material Compatibility | Can join dissimilar metals and nonmetals, versatile for complex assemblies. | Limited to simpler, smaller-scale applications. |
Thermal Considerations | Reduces thermal distortion, ideal for dimensional accuracy. | Lower temperatures minimize damage to delicate components. |
Applications | Automotive, HVAC, cookware—where strong, durable joints are critical. | Electronics—where weaker, semi-permanent connections are acceptable. |
Need help choosing the right metal-joining method for your project? Contact our experts today!