Chemical vapor deposition (CVD) is a sophisticated process used to deposit thin films of materials onto a substrate through chemical reactions in a controlled environment. The apparatus for CVD is designed to facilitate these reactions and ensure precise deposition. It typically includes components such as a gas delivery system, reaction chamber, energy source, vacuum system, and exhaust gas treatment system. The process involves several steps, including the evaporation of volatile compounds, thermal decomposition or chemical reactions, and the deposition of nonvolatile products onto the substrate. CVD is widely used in industries such as semiconductor manufacturing, nanotechnology, and magnetic coating applications due to its ability to produce high-quality, uniform thin films.
Key Points Explained:
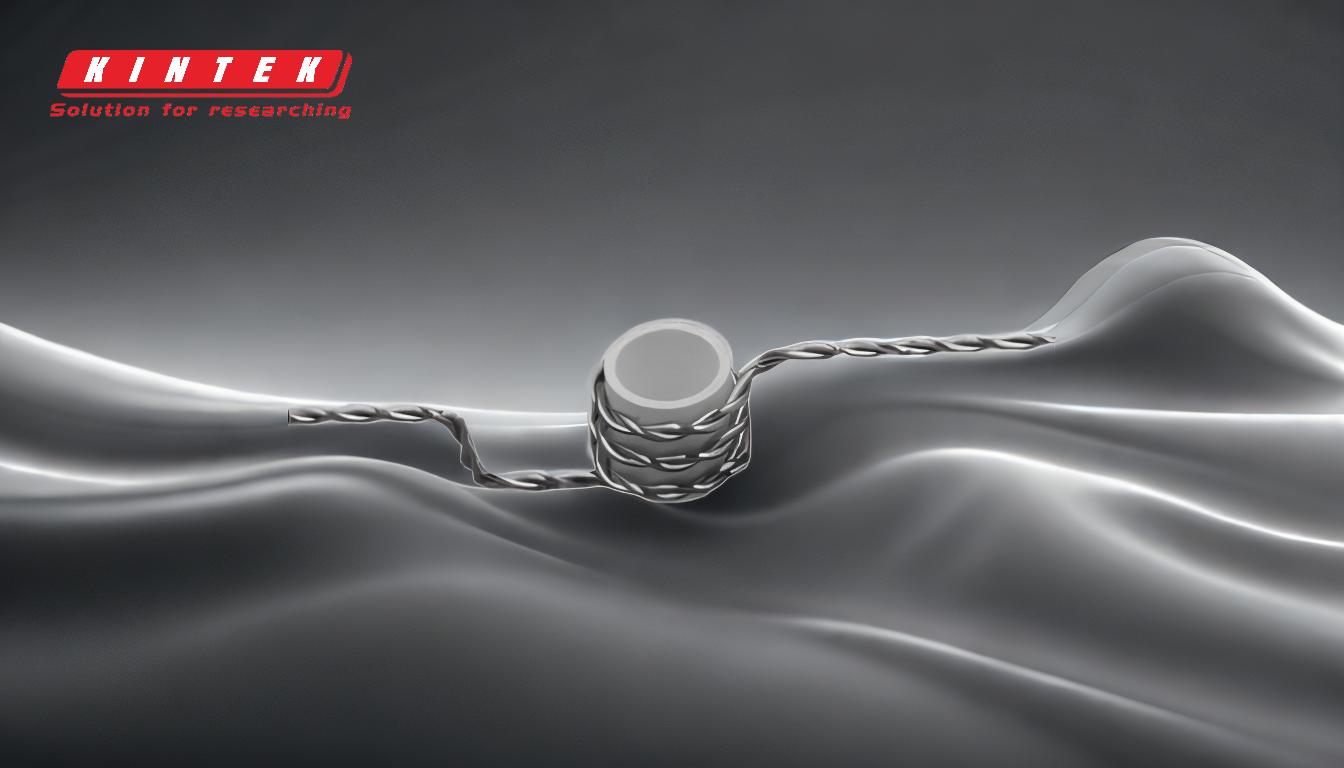
-
Components of CVD Apparatus:
- Gas Delivery System: This system controls the flow of precursor gases into the reaction chamber. Precise control of gas flow rates is crucial for achieving uniform deposition.
- Reaction Chamber (Reactor): The chamber is where the chemical reactions occur. It is designed to maintain specific temperature and pressure conditions to facilitate the deposition process.
- Loading/Unloading System: This system allows for the efficient transfer of substrates into and out of the reaction chamber, minimizing contamination and downtime.
- Energy Source: Heat or plasma is often used to provide the energy required for the chemical reactions. Common energy sources include resistive heating, induction heating, or plasma generation.
- Vacuum System: A vacuum is created to remove unwanted gases and ensure a controlled environment for the deposition process.
- Process Control System: Automation and monitoring systems ensure precise control over temperature, pressure, gas flow, and other critical parameters.
- Exhaust Gas Treatment System: This system safely removes and treats by-products and unreacted gases to prevent environmental contamination.
-
CVD Process Steps:
- Evaporation of Volatile Compounds: The precursor material is vaporized, often by heating, to create a gaseous phase.
- Thermal Decomposition or Chemical Reaction: The vaporized compounds decompose or react with other gases, vapors, or liquids at the substrate surface.
- Deposition of Nonvolatile Products: The resulting nonvolatile reaction products are deposited onto the substrate, forming a thin film.
-
Applications of CVD:
- Semiconductor Manufacturing: CVD is used to deposit thin films of materials such as silicon dioxide, silicon nitride, and polysilicon, which are essential for integrated circuits.
- Magnetic Coatings: CVD is employed to apply magnetic coatings on computer hard drives, enabling high-density data storage.
- Nanotechnology: CVD is a key technology for growing carbon nanotubes and other nanostructures, offering a cost-effective and scalable method for producing nano-scale materials.
-
Methods of CVD:
- Chemical Transport Method: Involves the transport of a solid precursor material in the form of a gas to the substrate.
- Pyrolysis Method: Uses thermal decomposition of a gaseous precursor to deposit a solid material.
- Synthesis Reaction Method: Involves chemical reactions between gaseous precursors to form the desired material.
-
Key Process Parameters:
- Target Materials: The choice of precursor materials, which can range from metals to semiconductors, is critical for achieving the desired film properties.
- Deposition Technology: Techniques such as electron beam lithography (EBL), atomic layer deposition (ALD), atmospheric pressure chemical vapor deposition (APCVD), and plasma-enhanced chemical vapor deposition (PECVD) are used to achieve specific film characteristics.
- Chamber Pressure and Substrate Temperature: These parameters influence the rate and quality of material deposition. Higher temperatures and lower pressures often result in faster deposition rates and higher-quality films.
-
Detailed CVD Process:
- Transport of Gaseous Species: The precursor gases are transported to the substrate surface.
- Adsorption: The gaseous species adsorb onto the substrate surface.
- Surface Reactions: Heterogeneous surface-catalyzed reactions occur, leading to the formation of the desired material.
- Surface Diffusion: The species diffuse across the substrate surface to growth sites.
- Nucleation and Growth: The film nucleates and grows on the substrate.
- Desorption and Transport of By-products: Gaseous reaction products are desorbed and transported away from the substrate, ensuring a clean deposition environment.
By understanding these key points, one can appreciate the complexity and precision required in the design and operation of chemical vapor deposition apparatus. The process is integral to many advanced manufacturing techniques, enabling the production of high-performance materials and devices.
Summary Table:
Component | Function |
---|---|
Gas Delivery System | Controls precursor gas flow for uniform deposition. |
Reaction Chamber | Maintains temperature and pressure for chemical reactions. |
Loading/Unloading System | Transfers substrates efficiently, minimizing contamination. |
Energy Source | Provides heat or plasma for chemical reactions. |
Vacuum System | Creates a controlled environment by removing unwanted gases. |
Process Control System | Automates and monitors critical parameters like temperature and pressure. |
Exhaust Gas Treatment | Safely removes and treats by-products to prevent contamination. |
Discover how CVD apparatus can enhance your manufacturing process—contact our experts today for more details!