Sintering furnaces are essential in various industries for transforming compact powders into durable, thermally resistant molds without melting the material. They are widely used in powder metallurgy, ceramics, and advanced materials manufacturing. These furnaces operate below the melting point of the powder, enabling precise shaping and enhancing material properties like strength and density. Applications range from creating metal components for automotive and aerospace industries to producing advanced ceramics and magnetic materials. The versatility of sintering furnaces makes them indispensable in industries requiring high-performance materials, such as energy, electronics, and construction.
Key Points Explained:
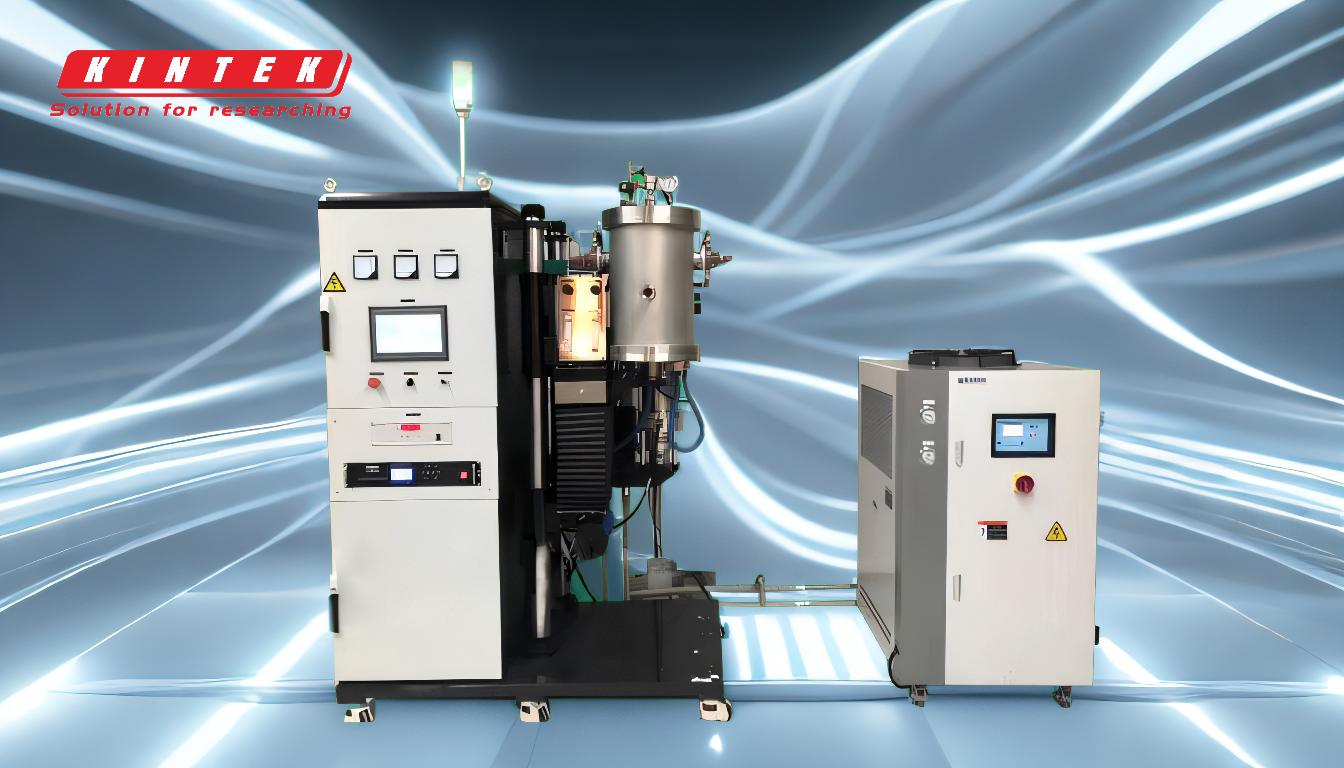
-
Solid-State Sintering Process:
- Sintering furnaces utilize solid-state sintering, where compacted powders are heated below their melting point to bond particles. This method ensures the material retains its shape while improving mechanical properties like strength and density.
- Applications include manufacturing metal components for automotive and aerospace industries, where precision and durability are critical.
-
Powder Metallurgy:
- Sintering furnaces are pivotal in powder metallurgy, producing components like gears, bearings, and filters. The process enhances material properties, making them suitable for high-stress applications.
- For example, sintering furnace is used to create stainless steel-based materials and cemented carbide, which are essential in cutting tools and wear-resistant parts.
-
Ceramics and Advanced Materials:
- These furnaces are used to produce advanced ceramics, such as zirconia and alumina, which are vital in electronics, medical devices, and industrial applications.
- They also play a role in manufacturing magnetic materials like neodymium-iron-boron, used in electric vehicles and renewable energy systems.
-
Energy Efficiency and Environmental Benefits:
- Sintering furnaces, especially vacuum and used models, are energy-efficient and reduce decarburization, making them environmentally friendly.
- For instance, used sintering furnaces are employed in diamond saw blade production, offering significant energy savings.
-
Versatility Across Industries:
- Sintering furnaces are used in diverse sectors, including aerospace, automotive, electronics, and construction. They enable the production of high-performance materials like superalloys and refractory materials.
- Rotary tube furnaces, a type of sintering furnace, are utilized in battery materials and new energy applications, highlighting their adaptability.
-
Specialized Applications:
- Vacuum sintering furnaces are ideal for materials requiring controlled atmospheres, such as metal injection molding products and high-specific-gravity gold.
- Retort furnaces, another variant, are used in shale oil extraction and charcoal development, showcasing the broad utility of sintering technology.
By understanding these key points, purchasers can evaluate the suitability of sintering furnaces for their specific needs, ensuring optimal performance and cost-efficiency in their operations.
Summary Table:
Application | Key Uses |
---|---|
Powder Metallurgy | Gears, bearings, filters, cutting tools, wear-resistant parts |
Ceramics & Advanced Materials | Zirconia, alumina, magnetic materials for electronics and renewable energy |
Energy & Environmental | Diamond saw blade production, energy-efficient processes |
Specialized Applications | Metal injection molding, shale oil extraction, high-specific-gravity gold |
Versatility Across Industries | Aerospace, automotive, electronics, construction, battery materials |
Ready to enhance your material production? Contact us today to find the perfect sintering furnace for your needs!