The arc melting method is a widely used technique in metallurgy for alloy preparation, leveraging electric energy to generate an electric arc that produces extremely high temperatures. This process involves creating an arc between electrodes or between an electrode and the material to be melted, resulting in the melting of metals or alloys. The method is particularly effective for preparing high-purity alloys and materials requiring precise control over composition and microstructure. Arc melting furnaces are designed to sustain stable arcs, ensuring consistent and efficient melting. This technique is favored in research and industrial settings for its ability to handle refractory materials and produce homogeneous alloys.
Key Points Explained:
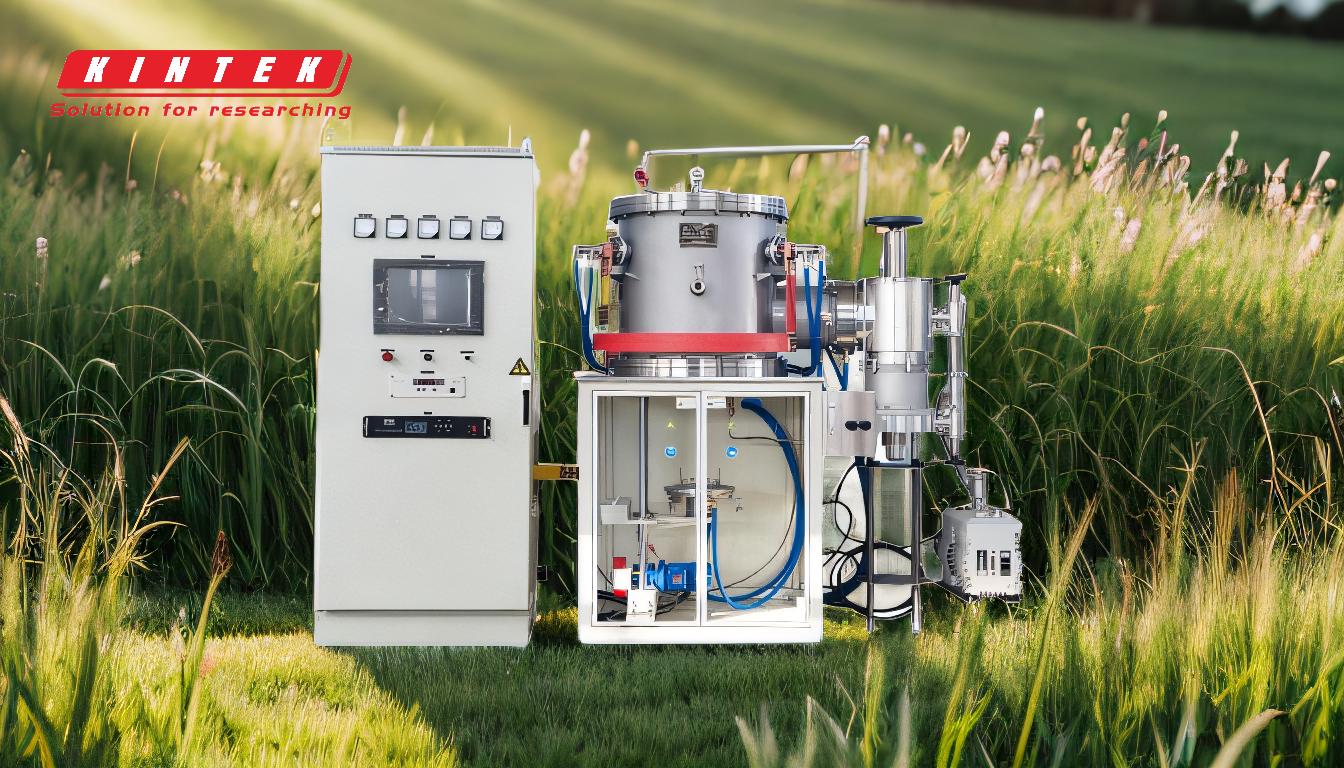
-
Definition and Principle of Arc Melting:
- Arc melting is an electrothermal metallurgical process that uses electric energy to generate an electric arc. This arc, which is a form of thermal plasma, produces temperatures high enough to melt metals and alloys.
- The arc is typically created between two electrodes or between an electrode and the material being melted. The intense heat generated by the arc allows for the melting of even refractory materials, which are difficult to melt using conventional methods.
-
Components of an Arc Melting Furnace:
- The primary component of an arc melting furnace is the electric welder, which converts standard electrical voltages (220V or 380V) into low voltage and high current. This conversion is crucial for generating the necessary arc intensity.
- The furnace also includes electrodes, which are usually made of materials like tungsten or graphite, and a crucible or hearth to hold the material being melted. The design ensures that the arc remains stable and self-sustaining throughout the melting process.
-
Process of Arc Melting:
- The arc is initiated by creating a short circuit between the positive and negative electrodes. Once the arc is established, it becomes a self-sustaining discharge phenomenon, maintaining stable combustion without extinguishing.
- The material to be melted is placed in the crucible, and the arc is directed towards it. The high temperature of the arc (often exceeding 3000°C) rapidly melts the material, allowing for the formation of alloys with precise compositions.
- The process can be conducted in a controlled atmosphere (e.g., inert gas like argon) to prevent oxidation and contamination, ensuring the production of high-purity alloys.
-
Advantages of Arc Melting:
- High Purity: Arc melting is capable of producing high-purity alloys, as the process can be conducted in a vacuum or inert atmosphere, minimizing contamination.
- Versatility: The method is suitable for melting a wide range of materials, including refractory metals and alloys that are difficult to melt using other techniques.
- Precision: Arc melting allows for precise control over the composition and microstructure of the alloy, making it ideal for research and development purposes.
- Efficiency: The process is relatively fast and efficient, with the ability to melt materials quickly due to the high temperatures generated by the arc.
-
Applications of Arc Melting:
- Research and Development: Arc melting is extensively used in laboratories for the preparation of experimental alloys and materials. Its ability to produce small, high-quality samples makes it ideal for research purposes.
- Industrial Production: In industrial settings, arc melting is used for the production of specialized alloys, particularly those used in aerospace, electronics, and other high-tech industries.
- Refractory Materials: The method is particularly useful for melting refractory materials, such as tungsten, molybdenum, and titanium, which require extremely high temperatures to melt.
-
Considerations for Equipment Purchasers:
- Power Requirements: When purchasing an arc melting furnace, it is important to consider the power requirements, as the process requires high current and low voltage. Ensure that the facility has the necessary electrical infrastructure.
- Atmosphere Control: For applications requiring high-purity alloys, furnaces with atmosphere control (e.g., vacuum or inert gas) should be considered to prevent contamination.
- Material Compatibility: The furnace should be compatible with the materials you intend to melt, including the ability to handle refractory metals if necessary.
- Safety Features: Given the high temperatures involved, safety features such as cooling systems, protective shielding, and emergency shut-off mechanisms are essential.
In summary, the arc melting method is a powerful and versatile technique for alloy preparation, offering high purity, precision, and efficiency. It is widely used in both research and industrial applications, particularly for melting refractory materials and producing specialized alloys. When selecting equipment, considerations such as power requirements, atmosphere control, material compatibility, and safety features are crucial to ensure optimal performance and safety.
Summary Table:
Aspect | Details |
---|---|
Definition | Electrothermal process using electric arcs to melt metals and alloys. |
Key Components | Electric welder, electrodes (tungsten/graphite), crucible/hearth. |
Process | Arc generates >3000°C heat, melts materials in controlled atmospheres. |
Advantages | High purity, versatility, precision, and efficiency. |
Applications | Research, industrial production, refractory material melting. |
Equipment Considerations | Power requirements, atmosphere control, material compatibility, safety. |
Discover how arc melting can enhance your alloy preparation—contact our experts today!