The ash content of a furnace refers to the inorganic, noncombustible material left after a sample is completely burned. This residue typically consists of oxides of inorganic elements present in the original sample. Ashing furnaces are designed to precisely control the combustion process, ensuring uniform temperature and stable conditions for accurate ash content measurement. The furnace's heating elements, chamber, and airflow systems work together to burn samples at controlled rates, allowing for precise weighing before, during, and after combustion. The ash content is a critical metric in various industries, as it provides insight into the purity and composition of materials.
Key Points Explained:
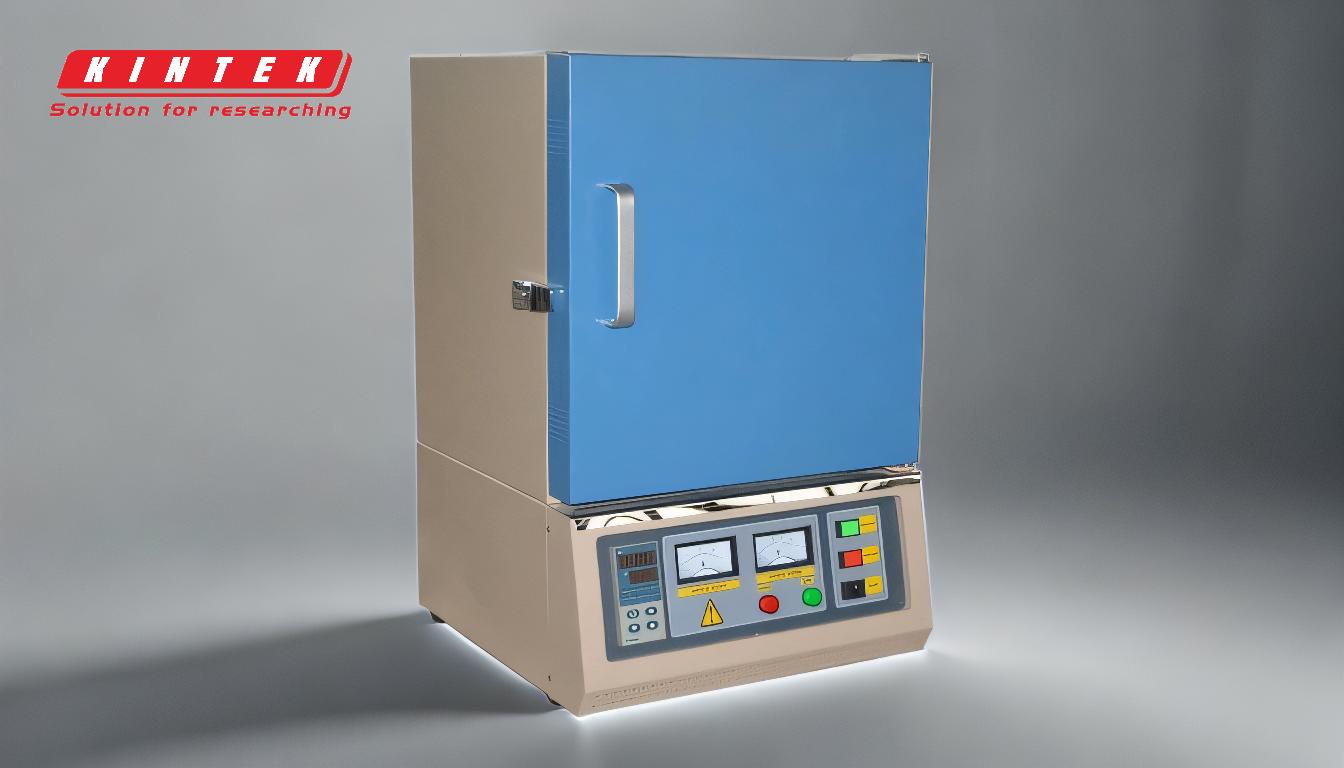
-
Definition of Ash Content:
- Ash content is the measure of inorganic, noncombustible material remaining after a sample is completely burned.
- It consists of oxides of inorganic elements present in the original sample, such as metals and minerals.
-
Role of an Ashing Furnace:
- An ashing furnace is specialized equipment designed to burn samples under controlled conditions.
- It ensures uniform temperature, stable heating, and precise airflow to achieve accurate ash content measurements.
-
Components of an Ashing Furnace:
- Heating Element: Provides high-temperature heat to combust the sample.
- Chamber: Encloses the sample and maintains controlled atmospheric conditions.
- Scale: Weighs the sample before, during, and after combustion to determine ash content.
- Airflow System: Controls air metering and exhaustion to achieve multiple air changes per minute, ensuring complete combustion.
-
Process of Measuring Ash Content:
- The sample is weighed before combustion.
- It is then placed in the furnace and burned at high temperatures until only inorganic residues remain.
- The residue (ash) is weighed again to calculate the ash content as a percentage of the original sample weight.
-
Importance of Ash Content Measurement:
- Material Purity: Indicates the presence of impurities or inorganic additives in materials like coal, food, or polymers.
- Quality Control: Essential in industries such as food processing, pharmaceuticals, and materials science to ensure product consistency.
- Environmental Analysis: Helps assess the environmental impact of materials by identifying noncombustible components.
-
Advantages of Modern Ashing Furnaces:
- Uniform Temperature: Ensures consistent combustion conditions for accurate results.
- Fast Heating: Reduces processing time and improves efficiency.
- Energy Efficiency: Designed to minimize energy consumption while maintaining high performance.
- Durability: Long-lasting components reduce maintenance and replacement costs.
-
Applications of Ash Content Analysis:
- Food Industry: Determines the mineral content in food products.
- Coal and Fuel Analysis: Measures the noncombustible residue in fuels to assess quality and efficiency.
- Pharmaceuticals: Ensures the purity of raw materials and finished products.
- Environmental Testing: Analyzes soil, waste, and other materials for inorganic contaminants.
By understanding the ash content of a furnace and the processes involved, purchasers can make informed decisions about equipment selection, ensuring they meet the specific needs of their industry while maintaining accuracy and efficiency in material analysis.
Summary Table:
Key Aspect | Description |
---|---|
Definition of Ash Content | Inorganic, noncombustible material left after complete combustion of a sample. |
Role of Ashing Furnace | Ensures uniform temperature, stable heating, and precise airflow for accuracy. |
Components | Heating element, chamber, scale, and airflow system for controlled combustion. |
Measurement Process | Sample is weighed before and after combustion to calculate ash content. |
Importance | Indicates material purity, ensures quality control, and aids environmental analysis. |
Advantages | Uniform temperature, fast heating, energy efficiency, and durability. |
Applications | Food industry, coal/fuel analysis, pharmaceuticals, and environmental testing. |
Discover how ashing furnaces can enhance your material analysis—contact us today for expert guidance!