The ball milling process is a versatile and widely used technique for grinding, mixing, and processing materials across various industries. It involves the use of a rotating cylindrical chamber filled with grinding media (typically steel or ceramic balls) to reduce particle size, mix materials, or alter material properties. This process is essential in industries such as mining, cement production, ceramics, and pharmaceuticals, as well as in scientific research for tasks like mechanical alloying, powder production, and particle size reduction. Ball milling is valued for its ability to achieve fine grinding, homogenization, and material transformation.
Key Points Explained:
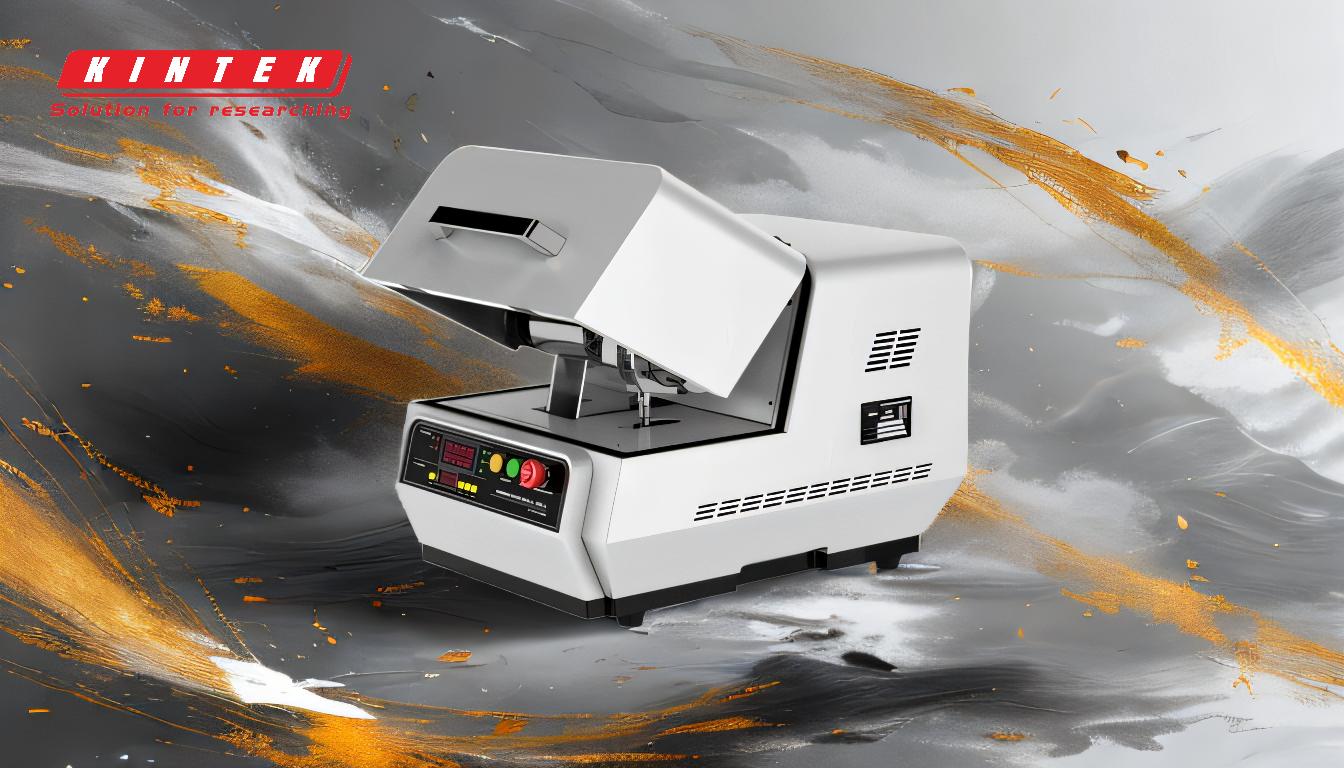
-
Primary Purpose of Ball Milling: Grinding and Size Reduction
- Ball mills are primarily used to grind materials into fine powders or smaller particles. This is crucial in industries like mining, where ores need to be ground down for further processing.
- In scientific research, ball milling is used to reduce particle size for analysis or to create uniform particle distributions.
- The process is also employed to eliminate agglomeration (clumping of particles) and change particle shape, which can improve material properties.
-
Applications in Specific Industries
- Mining: Ball mills are used to grind mining ores into fine particles, enabling efficient extraction of valuable minerals.
- Cement Production: In the cement industry, ball mills grind raw materials like limestone and clay into a fine powder, which is then heated to produce cement.
- Ceramics and Pottery: Ball mills grind materials like feldspar and pigments to create fine powders used in ceramics and pottery.
- Pharmaceuticals: In this industry, ball milling is used to produce fine powders for drug formulations and to ensure uniform mixing of active ingredients.
-
Material Transformation and Mechanical Alloying
- Ball milling can alter material properties, such as hardness, reactivity, and thermal conductivity, by inducing structural changes at the atomic or molecular level.
- Mechanical alloying, a process enabled by ball milling, involves the repeated fracturing and welding of powder particles to create alloys with unique properties.
-
Mixing and Homogenization
- Ball mills are effective for mixing different materials to create homogeneous blends. This is particularly important in industries like fertilizers, where uniform distribution of nutrients is critical.
- In scientific research, ball milling is used to mix materials for experiments or to create composite materials.
-
Production of Powders
- Ball milling is widely used to produce fine powders for various applications, including pigments, ceramics, and advanced materials.
- The process ensures that powders have consistent particle sizes and shapes, which is essential for quality control in manufacturing.
-
Versatility Across Industries
- Ball mills are used in a wide range of industries, including cement, silicates, refractory materials, fertilizers, glass ceramics, and more.
- Their adaptability makes them a valuable tool for both industrial production and scientific research.
-
Scientific and Laboratory Applications
- In research laboratories, ball mills are used to grind materials for analysis, such as spectroscopy or microscopy.
- They are also used to prepare samples for experiments, ensuring consistent particle size and distribution.
By understanding the diverse applications of ball milling, equipment and consumable purchasers can make informed decisions about the types of ball mills and grinding media needed for their specific industry or research needs. The process's ability to achieve precise particle size reduction, material mixing, and property alteration makes it an indispensable tool in modern manufacturing and scientific exploration.
Summary Table:
Key Aspect | Description |
---|---|
Primary Purpose | Grinding and size reduction for fine powders or smaller particles. |
Applications | Mining, cement production, ceramics, pharmaceuticals, and scientific research. |
Material Transformation | Alters properties like hardness, reactivity, and thermal conductivity. |
Mixing and Homogenization | Creates uniform blends for fertilizers, composites, and experiments. |
Powder Production | Produces fine powders for pigments, ceramics, and advanced materials. |
Versatility | Used in cement, silicates, fertilizers, glass ceramics, and more. |
Scientific Applications | Prepares samples for analysis and experiments with consistent particle sizes. |
Ready to optimize your material processing? Contact us today to find the perfect ball milling solution for your needs!