In sputtering, the cathode and anode play crucial roles in the deposition process. The cathode is the target material that gets bombarded by ions, causing atoms to be ejected and deposited onto a substrate. The anode, on the other hand, is typically the substrate holder or a separate electrode that completes the electrical circuit. Understanding the functions and characteristics of these electrodes is essential for optimizing the sputtering process and achieving high-quality thin films.
Key Points Explained:
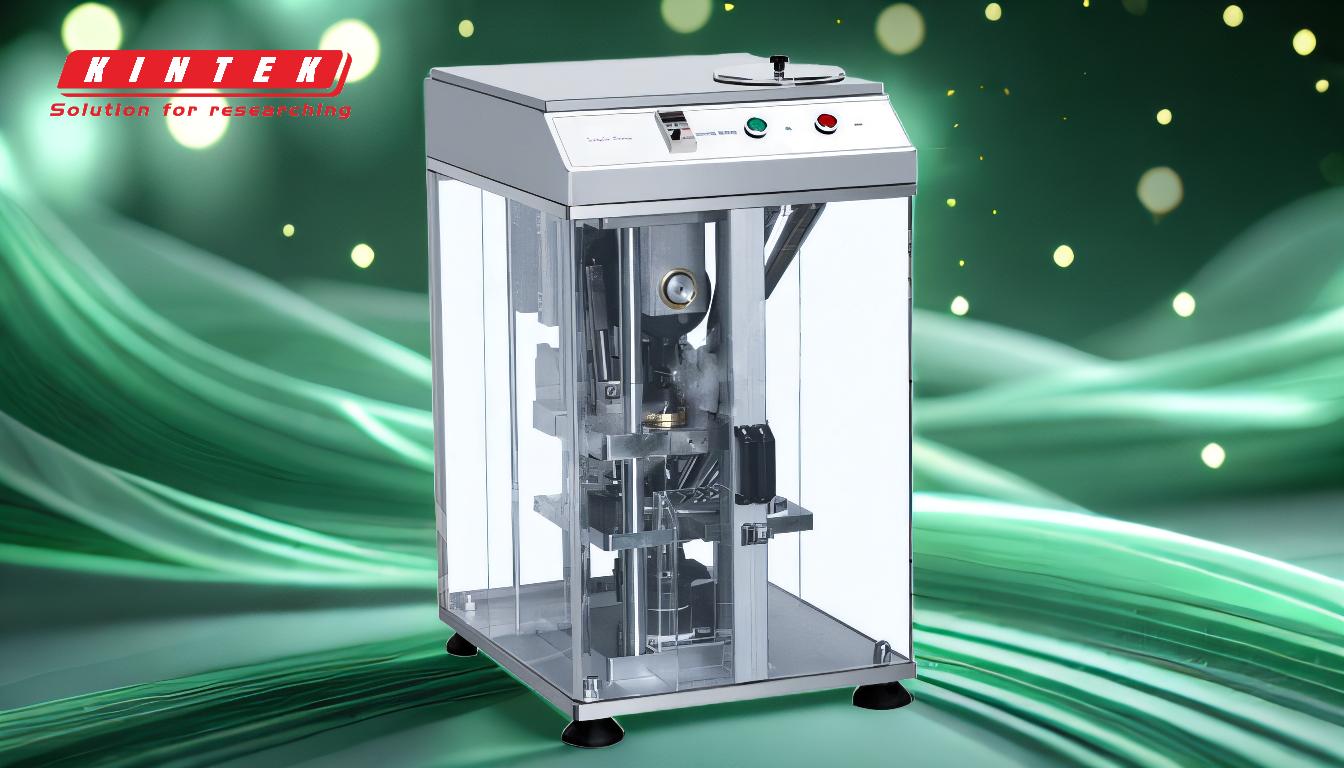
-
Cathode in Sputtering:
- Definition: The cathode in sputtering is the target material that is subjected to ion bombardment. It is typically made of the material that you want to deposit as a thin film.
- Function: When high-energy ions (usually argon ions) strike the cathode, they dislodge atoms from its surface. These atoms then travel through the vacuum chamber and deposit onto the substrate.
- Material Considerations: The cathode material must be conductive and able to withstand the high-energy bombardment without degrading. Common materials include metals like gold, silver, and aluminum, as well as compounds like oxides and nitrides.
-
Anode in Sputtering:
- Definition: The anode in sputtering is the electrode that completes the electrical circuit. It can be the substrate holder or a separate electrode placed within the vacuum chamber.
- Function: The anode collects electrons that are emitted from the cathode during the sputtering process. This helps maintain the plasma discharge necessary for the sputtering to occur.
- Material Considerations: The anode material should be conductive and stable under the conditions of the sputtering process. Often, it is made from materials like stainless steel or other conductive alloys.
-
Electrode Configuration:
- Cathode-Anode Relationship: In a typical sputtering setup, the cathode (target) and anode (substrate holder) are positioned opposite each other within the vacuum chamber. The distance between them, known as the target-to-substrate distance, can affect the uniformity and quality of the deposited film.
- Electrical Circuit: The cathode is connected to the negative terminal of the power supply, while the anode is connected to the positive terminal. This setup creates an electric field that accelerates ions towards the cathode, initiating the sputtering process.
-
Plasma Generation:
- Role of Cathode and Anode: The cathode and anode are essential for generating and maintaining the plasma. The cathode emits secondary electrons when bombarded by ions, and these electrons are accelerated towards the anode, helping to sustain the plasma.
- Plasma Characteristics: The plasma consists of ions, electrons, and neutral particles. The interaction between the cathode and anode helps maintain the ionization of the gas (usually argon) within the chamber, ensuring a continuous supply of ions for sputtering.
-
Process Optimization:
- Power Supply: The voltage and current applied to the cathode and anode can be adjusted to control the sputtering rate and the quality of the deposited film. Higher voltages generally increase the sputtering rate but may also lead to more defects in the film.
- Gas Pressure: The pressure of the sputtering gas (argon) affects the mean free path of the sputtered atoms and the energy of the ions. Optimal gas pressure is crucial for achieving uniform and high-quality films.
- Substrate Temperature: The temperature of the substrate (anode) can influence the adhesion and crystallinity of the deposited film. Controlling the substrate temperature is often necessary for specific applications.
-
Applications and Considerations:
- Thin Film Deposition: Sputtering is widely used in the semiconductor industry for depositing thin films of metals, oxides, and nitrides. The choice of cathode material directly affects the properties of the deposited film.
- Reactive Sputtering: In reactive sputtering, a reactive gas (like oxygen or nitrogen) is introduced into the chamber. The cathode material reacts with this gas to form compounds (e.g., oxides or nitrides) that are then deposited onto the substrate.
- Magnetron Sputtering: This advanced technique uses magnetic fields to confine electrons near the cathode, increasing the ionization of the sputtering gas and enhancing the sputtering rate. The cathode in magnetron sputtering is often equipped with magnets to achieve this effect.
Understanding the roles and interactions of the cathode and anode in sputtering is fundamental for controlling the deposition process and achieving desired film properties. By optimizing the electrode configuration, power supply, and process parameters, high-quality thin films can be produced for a wide range of applications.
Summary Table:
Aspect | Cathode | Anode |
---|---|---|
Definition | Target material bombarded by ions to eject atoms for deposition. | Electrode completing the electrical circuit, often the substrate holder. |
Function | Source of material for thin film deposition. | Collects electrons to sustain plasma discharge. |
Material | Conductive materials like gold, silver, aluminum, oxides, or nitrides. | Conductive and stable materials like stainless steel or alloys. |
Role in Plasma | Emits secondary electrons to maintain plasma. | Accelerates electrons to sustain ionization. |
Process Optimization | Adjust voltage/current for sputtering rate and film quality. | Control substrate temperature for film adhesion and crystallinity. |
Optimize your sputtering process today—contact our experts for tailored solutions!