Heat treatment is a critical process in metallurgy and materials science, used to alter the physical and sometimes chemical properties of materials, primarily metals. However, during heat treatment, contamination can occur, which can significantly affect the quality and performance of the treated materials. Contamination in heat treatment can arise from various sources, including the environment, equipment, and the materials themselves. This contamination can manifest as surface oxidation, scaling, decarburization, or the introduction of impurities that can degrade the material's properties. Understanding and mitigating these contamination sources is essential for achieving the desired material characteristics and ensuring the longevity and reliability of the treated components.
Key Points Explained:
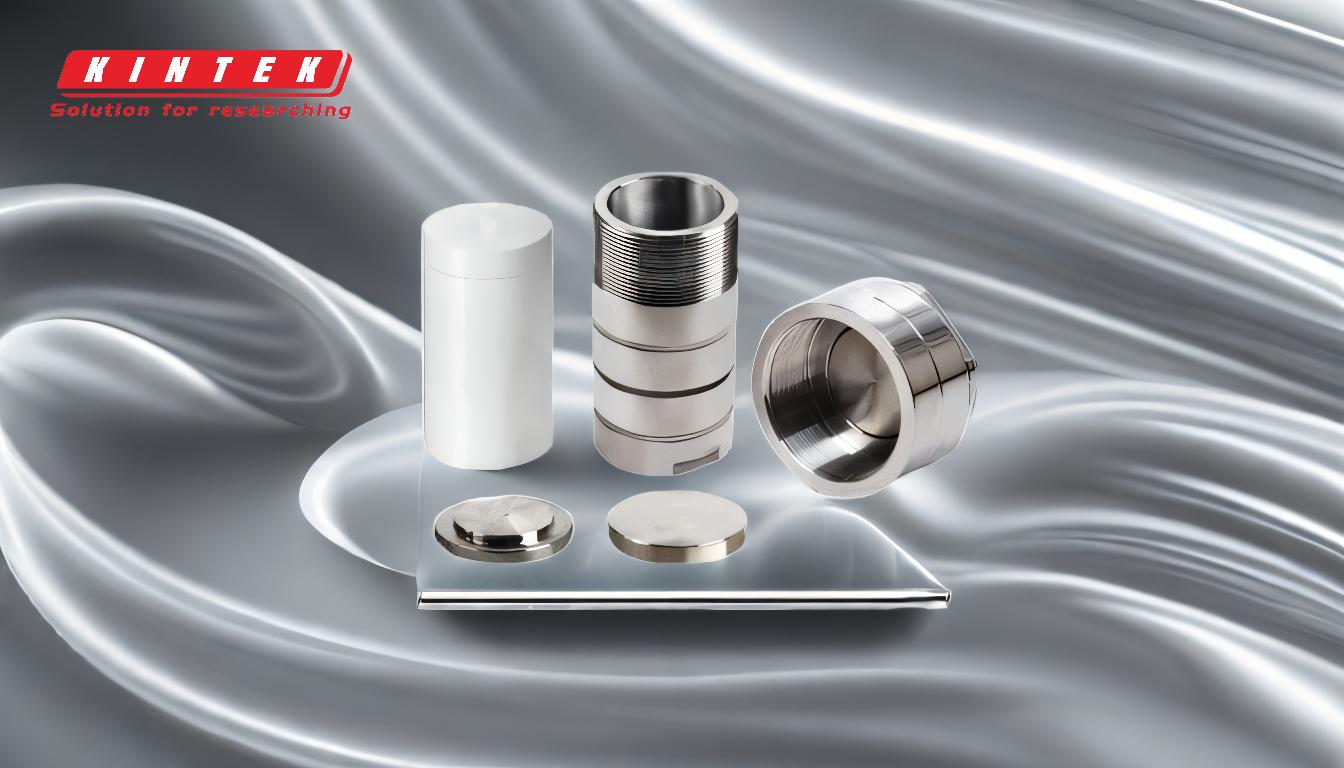
-
Types of Contamination in Heat Treatment:
- Oxidation: This occurs when the metal reacts with oxygen in the atmosphere, forming an oxide layer on the surface. This layer can be detrimental to the material's properties, especially if it is thick or uneven.
- Scaling: Similar to oxidation, scaling involves the formation of a thick layer of oxide on the metal surface, which can lead to material loss and surface roughness.
- Decarburization: This is the loss of carbon from the surface layer of steel during heat treatment, which can weaken the material and reduce its hardness.
- Impurities: Contaminants such as sulfur, phosphorus, or other elements can be introduced during the heat treatment process, leading to embrittlement or other undesirable properties.
-
Sources of Contamination:
- Atmosphere: The environment in which heat treatment is performed can introduce contaminants. For example, an ordinary atmosphere can lead to oxidation and scaling.
- Equipment: The heat treatment equipment itself can be a source of contamination if it is not properly maintained or if it introduces foreign materials into the process.
- Materials: The materials being treated can also contribute to contamination if they contain impurities or if they react with the treatment environment.
-
Impact of Contamination:
- Surface Quality: Contamination can lead to poor surface quality, which can affect the material's appearance and its ability to be further processed or coated.
- Mechanical Properties: Contaminants can alter the mechanical properties of the material, such as its strength, hardness, and ductility, leading to reduced performance.
- Corrosion Resistance: Contamination can reduce the material's resistance to corrosion, making it more susceptible to environmental degradation.
-
Mitigation Strategies:
- Controlled Atmosphere: Using a controlled atmosphere, such as an inert gas or vacuum, can prevent oxidation and other forms of contamination.
- Proper Equipment Maintenance: Regular maintenance and cleaning of heat treatment equipment can prevent the introduction of contaminants.
- Material Selection: Choosing materials with low impurity levels and ensuring they are properly prepared before heat treatment can reduce the risk of contamination.
-
Common Heat Treatment Methods and Contamination Risks:
- Annealing: This process involves heating the material to a specific temperature and then cooling it slowly. Contamination risks include oxidation and scaling, especially if the process is not performed in a controlled atmosphere.
- Quenching: Rapid cooling of the material can lead to thermal stresses and potential contamination if the quenching medium is not clean or if the material is exposed to air during cooling.
- Tempering: This process involves reheating the material to a lower temperature after quenching to reduce brittleness. Contamination risks include oxidation and the introduction of impurities during reheating.
- Normalizing: Similar to annealing, but with faster cooling, normalizing can also lead to surface oxidation if not performed in a controlled environment.
- Case Hardening: This process involves adding carbon or nitrogen to the surface of the material to increase hardness. Contamination risks include improper gas composition or impurities in the hardening medium.
- Martensitic Transformation: This is a phase transformation that occurs during quenching, leading to a hard, brittle structure. Contamination risks include improper cooling rates or exposure to contaminants during the transformation process.
In conclusion, contamination in heat treatment is a significant concern that can affect the quality and performance of treated materials. By understanding the types and sources of contamination, as well as implementing effective mitigation strategies, it is possible to minimize these risks and achieve the desired material properties. Proper control of the heat treatment environment, equipment maintenance, and material selection are key factors in reducing contamination and ensuring the success of the heat treatment process.
Summary Table:
Aspect | Details |
---|---|
Types of Contamination | Oxidation, Scaling, Decarburization, Impurities |
Sources | Atmosphere, Equipment, Materials |
Impacts | Poor surface quality, reduced mechanical properties, lower corrosion resistance |
Mitigation Strategies | Controlled atmosphere, proper equipment maintenance, material selection |
Ensure your heat treatment processes are contamination-free—contact our experts today for tailored solutions!