The cooling rate of a muffle furnace depends on several factors, including its design, insulation, chamber size, and the temperature difference between the furnace interior and the ambient environment. Muffle furnaces are designed to retain heat efficiently, which means they cool down relatively slowly compared to other types of furnaces. The cooling process can be natural (passive) or accelerated using external cooling systems. Natural cooling rates are influenced by the furnace's insulation quality and chamber size, while forced cooling methods, such as fans or water-cooling systems, can significantly reduce cooling times.
Key Points Explained:
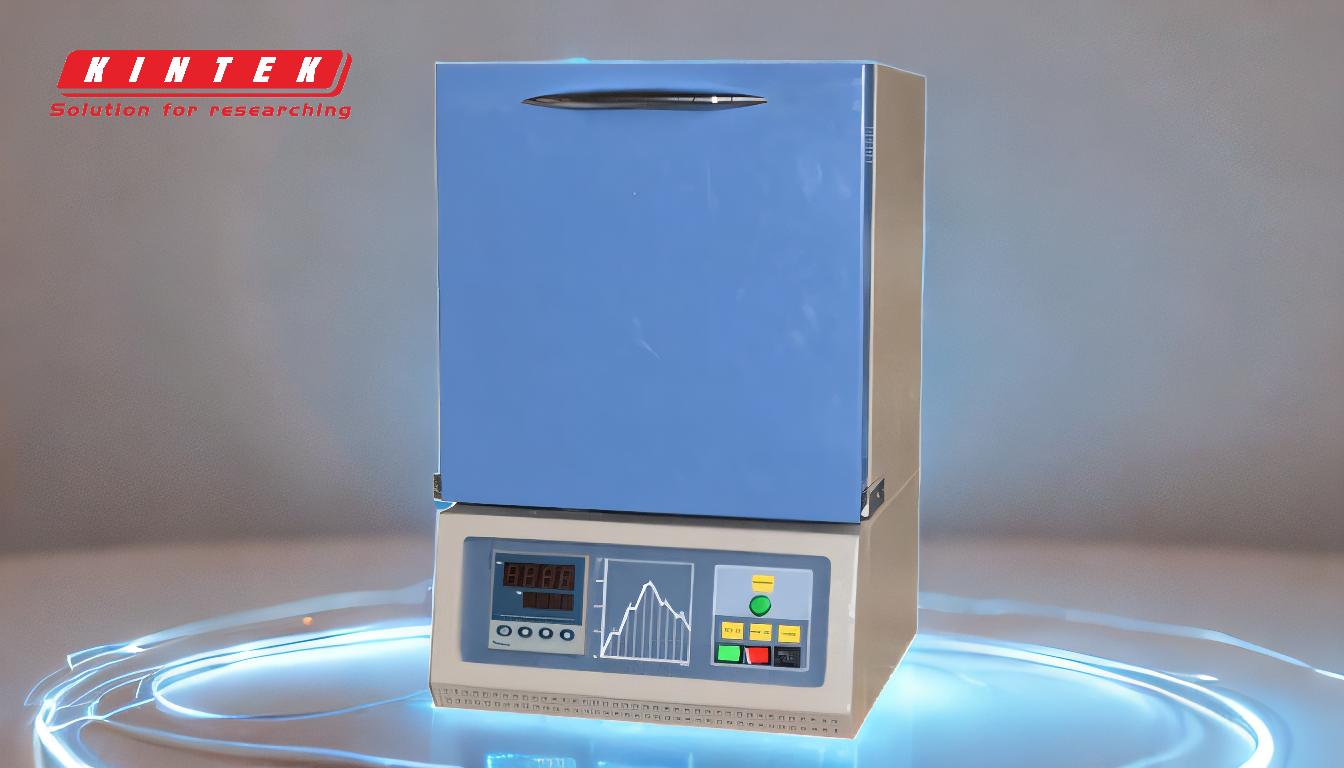
-
Factors Affecting Cooling Rate:
- Insulation: Muffle furnaces are built with thick, high-quality insulating materials to maintain high temperatures. This insulation also slows down the cooling process, as heat is retained within the chamber for longer periods.
- Chamber Size: Smaller chambers tend to cool faster than larger ones due to the reduced volume of air and materials that need to dissipate heat.
- Temperature Difference: The greater the difference between the furnace's internal temperature and the ambient temperature, the faster the initial cooling rate. However, as the temperature inside the furnace decreases, the cooling rate slows down.
- Material Load: The amount and type of material inside the furnace can affect cooling. Materials with high thermal mass will retain heat longer, slowing the cooling process.
-
Natural vs. Forced Cooling:
- Natural Cooling: This is the default cooling method for most muffle furnaces. It relies on the gradual dissipation of heat through the furnace walls and into the surrounding environment. Natural cooling can take several hours, especially for furnaces operating at very high temperatures (e.g., 1300°C or higher).
- Forced Cooling: Some muffle furnaces are equipped with cooling systems, such as fans or water-cooling jackets, to accelerate the cooling process. These systems can reduce cooling times significantly, making the furnace ready for reuse more quickly.
-
Typical Cooling Rates:
- For a standard muffle furnace operating at 1000°C, the natural cooling rate might be around 100-200°C per hour, depending on the factors mentioned above.
- At higher temperatures (e.g., 1300°C or above), the initial cooling rate might be faster (e.g., 200-300°C per hour) but will slow down as the temperature decreases.
- Forced cooling systems can increase the cooling rate to 500°C per hour or more, depending on the system's efficiency.
-
Importance of Cooling Rate in Applications:
- Material Properties: The cooling rate can affect the microstructure and properties of materials being processed. For example, metals may require controlled cooling to achieve desired hardness or toughness.
- Operational Efficiency: Faster cooling rates improve the furnace's operational efficiency by reducing downtime between cycles.
- Safety: Rapid cooling systems must be carefully managed to avoid thermal shock, which can damage the furnace or the materials being processed.
-
Design Considerations for Cooling:
- Insulation Thickness: Thicker insulation slows cooling but improves energy efficiency during operation.
- Ventilation: Some furnaces include ventilation ports to allow heat to escape more quickly during cooling.
- Cooling System Integration: Advanced models may integrate cooling systems directly into the furnace design for better control and efficiency.
In summary, the cooling rate of a muffle furnace is influenced by its design, insulation, and the cooling method employed. Natural cooling is slower but sufficient for many applications, while forced cooling systems offer faster turnaround times for high-throughput operations. Understanding these factors is essential for optimizing furnace performance and achieving desired material properties.
Summary Table:
Factor | Impact on Cooling Rate |
---|---|
Insulation | Thicker insulation retains heat longer, slowing cooling. |
Chamber Size | Smaller chambers cool faster due to reduced heat volume. |
Temperature Difference | Greater difference between furnace and ambient temperatures speeds up initial cooling. |
Material Load | High thermal mass materials retain heat longer, slowing cooling. |
Cooling Method | Natural cooling is slower; forced cooling (fans, water-cooling) significantly reduces time. |
Need help optimizing your muffle furnace's cooling rate? Contact our experts today for tailored solutions!