The cooling system of an induction furnace is a critical component that ensures the furnace operates efficiently and safely. It primarily uses water or air cooling to manage the heat generated during the melting process. Water cooling is commonly employed to keep the induction coils and other components at optimal temperatures, preventing overheating and ensuring precise temperature control. Air cooling systems are also used, particularly in environments where personnel safety and comfort are a concern. The cooling system's design and capacity are tailored to the furnace's size and operational requirements, ensuring stability and efficiency in the melting process.
Key Points Explained:
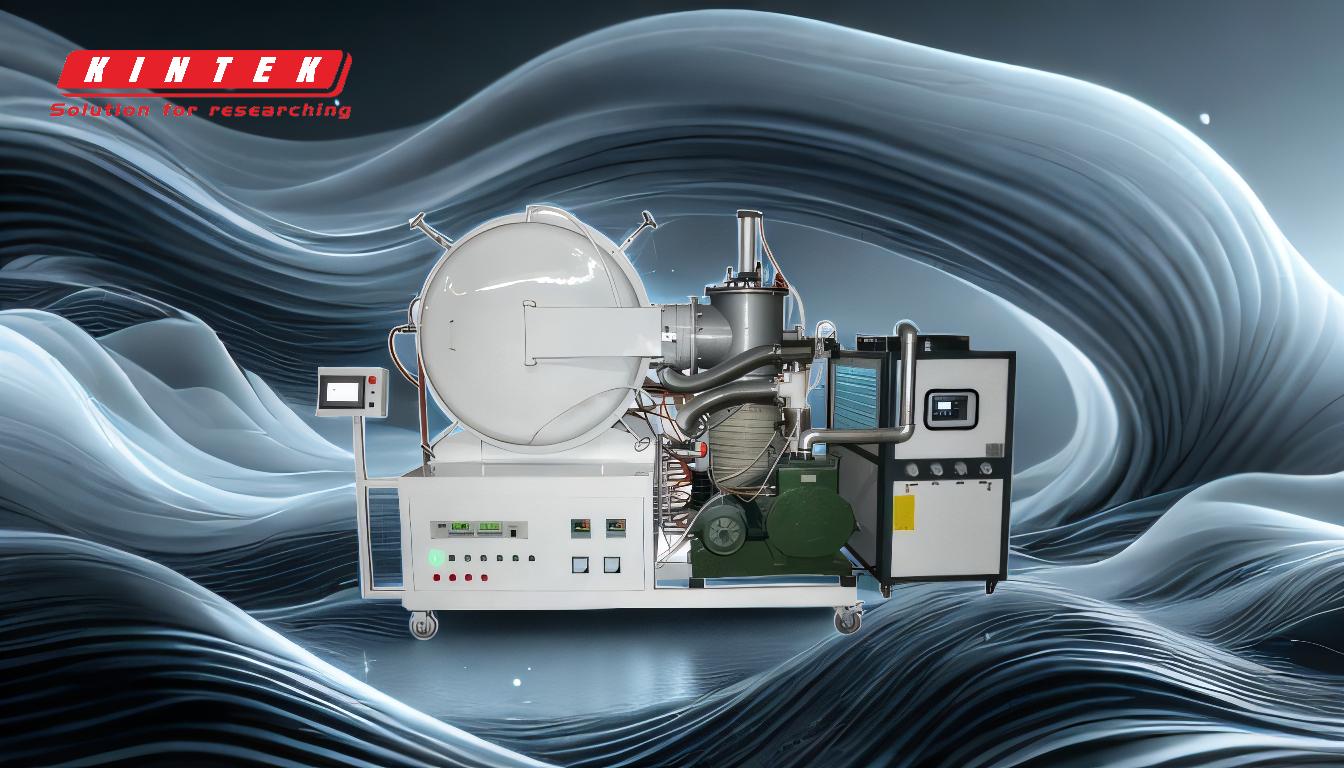
-
Purpose of the Cooling System:
- The cooling system in an induction furnace is designed to manage the heat generated during the melting process. This prevents overheating of critical components like the induction coils and ensures the furnace operates within safe temperature ranges.
- It also enables precise temperature control, which is essential for efficient melting and maintaining the quality of the melted metal.
-
Types of Cooling Systems:
- Water Cooling System: This is the most common type of cooling system in induction furnaces. It involves circulating cold water through channels or pipes around the induction coils and other heat-sensitive components. The water absorbs heat and carries it away, preventing overheating and maintaining optimal operating temperatures.
- Air Cooling System: In some cases, especially in environments where personnel safety and comfort are a concern, air cooling systems are used. These systems involve air conditioners or coolers that operate simultaneously with the furnace to dissipate heat and maintain a comfortable working environment.
-
Components of the Cooling System:
- Induction Coils: These are the primary components that require cooling. They generate significant heat during operation, and without proper cooling, they can overheat and fail.
- Flexible Cooling Cables: In water-cooled systems, flexible cables are used to supply cold water to the induction coils. These cables are designed to withstand the high temperatures and mechanical stresses of the furnace environment.
- Centralized Cooling Water and Discharge Device: In more advanced systems, such as those used in vacuum induction melting furnaces, a centralized cooling water system is employed. This system ensures a controlled flow of cooling water and efficient discharge of heated water, maintaining a stable melting temperature.
-
Importance of Cooling in Induction Furnaces:
- Preventing Overheating: The cooling system prevents the induction coils and other components from overheating, which could lead to equipment failure and safety hazards.
- Ensuring Efficiency: By maintaining optimal temperatures, the cooling system ensures the furnace operates efficiently, reducing energy consumption and improving melting speed.
- Safety and Comfort: In environments where personnel are present, cooling systems, particularly air cooling, help maintain a safe and comfortable working environment by dissipating excess heat.
-
Design Considerations:
- Matching Cooling Capacity to Furnace Size: The cooling system's size and capacity must be appropriately matched to the furnace's size and operational requirements. A system that is too small may not provide adequate cooling, while an oversized system may be inefficient and costly.
- Integration with Furnace Operation: The cooling system must be designed to operate seamlessly with the furnace. In many cases, the furnace and cooling system are designed to function simultaneously, ensuring continuous cooling during the melting process.
-
Applications of Cooling Systems:
- Vacuum Induction Melting Furnaces: In these specialized furnaces, cooling systems are crucial for maintaining a controlled melting temperature, especially in vacuum environments where heat dissipation can be challenging.
- General Induction Melting Furnaces: In standard induction melting furnaces, cooling systems are essential for preventing overheating and ensuring efficient operation, regardless of the specific application or metal being melted.
In summary, the cooling system is an integral part of an induction furnace, ensuring safe, efficient, and precise operation. Whether through water or air cooling, these systems play a vital role in maintaining the furnace's performance and longevity.
Summary Table:
Aspect | Details |
---|---|
Purpose | Prevents overheating, ensures precise temperature control, and maintains safety. |
Types | Water cooling (most common) and air cooling (for personnel safety). |
Key Components | Induction coils, flexible cooling cables, centralized cooling systems. |
Importance | Enhances efficiency, prevents equipment failure, and ensures operator comfort. |
Design Considerations | Matches cooling capacity to furnace size and integrates with furnace operation. |
Applications | Used in vacuum induction melting furnaces and general induction melting furnaces. |
Discover how the right cooling system can optimize your induction furnace—contact our experts today!