Chemical vapor deposition (CVD) is a manufacturing process where a solid material is deposited onto a substrate through chemical reactions occurring in the vapor phase. The process involves exposing a heated substrate to gaseous reactants, which undergo reactions such as decomposition, combination, hydrolysis, oxidation, or reduction. These reactions result in the formation of a thin film, powder, or single crystal on the substrate. CVD is widely used in industries like semiconductor manufacturing due to its ability to produce high-quality, uniform coatings. The process is conducted at elevated temperatures, typically around 1925°F (1051°C), in a controlled atmosphere to ensure precise deposition of the desired material.
Key Points Explained:
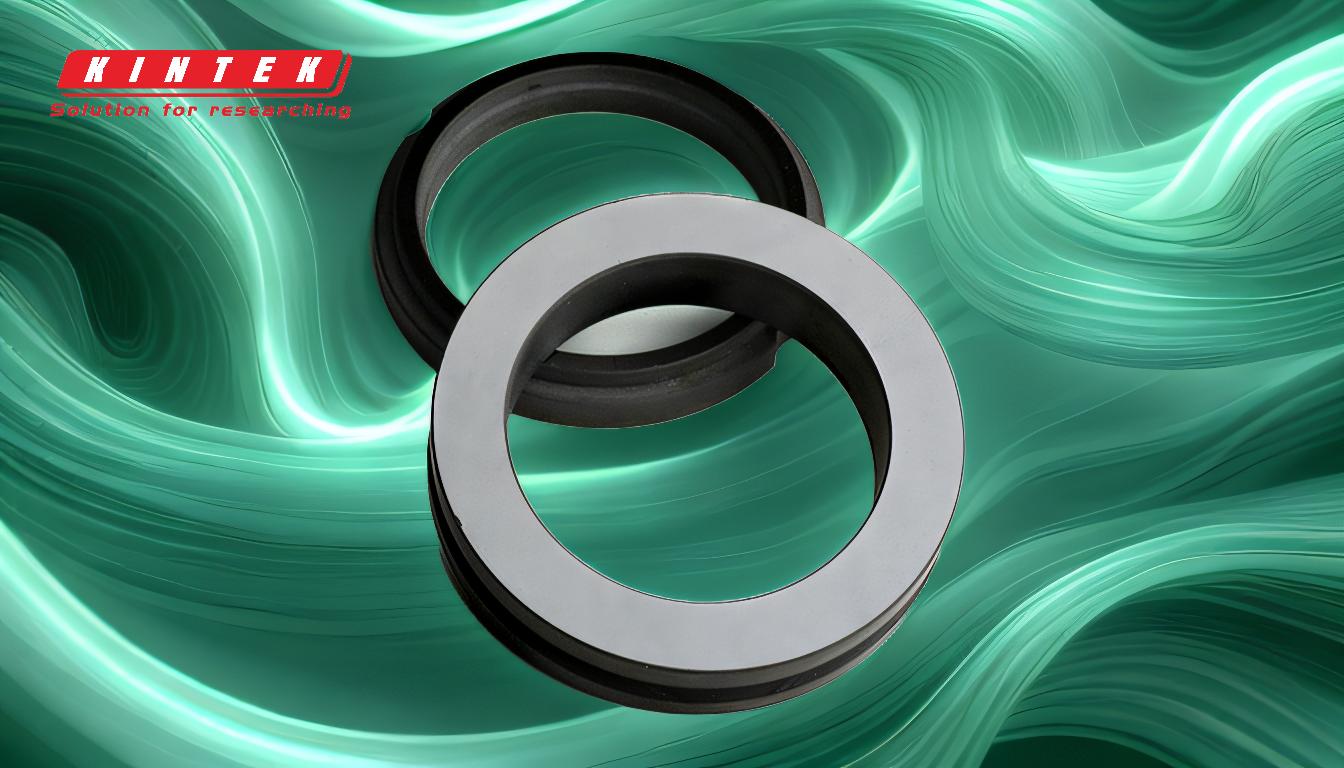
-
Definition and Purpose of CVD:
- CVD is a process where a solid material is deposited onto a substrate through chemical reactions in the vapor phase.
- The resulting material can be in the form of a thin film, powder, or single crystal, depending on the application.
- It is a fundamental technology used in industries like semiconductor manufacturing, where precise and high-quality coatings are required.
-
Chemical Reactions Involved in CVD:
- Decomposition of Reactive Gases: Gaseous reactants break down into simpler molecules or atoms, which then deposit onto the substrate.
- Combination of Gases: Two or more gaseous reactants combine to form a new compound that deposits onto the substrate.
- Hydrolysis of Gases: Gaseous reactants react with water vapor to form a solid deposit.
- Gas Oxidation: Gaseous reactants react with oxygen to form an oxide layer on the substrate.
- Reduction of Gases: Gaseous reactants are reduced, often by hydrogen, to deposit a pure element or compound onto the substrate.
-
Process Conditions:
- CVD is conducted at elevated temperatures, typically around 1925°F (1051°C), to facilitate the necessary chemical reactions.
- The process occurs in a controlled atmosphere, often within a CVD reactor, to ensure the purity and uniformity of the deposited material.
- The substrate is usually heated to promote the deposition of the material.
-
Applications of CVD:
- Semiconductor Manufacturing: CVD is used to deposit thin films of materials like silicon dioxide, silicon nitride, and polysilicon, which are essential for the fabrication of integrated circuits.
- Optical Coatings: CVD is used to create anti-reflective coatings on lenses and other optical components.
- Protective Coatings: CVD can be used to deposit hard, wear-resistant coatings on tools and other components to extend their lifespan.
- Powder Production: CVD is used to produce fine powders of materials like tungsten carbide, which are used in various industrial applications.
-
Advantages of CVD:
- High-Quality Deposits: CVD produces high-purity, uniform coatings with excellent adhesion to the substrate.
- Versatility: CVD can be used to deposit a wide range of materials, including metals, ceramics, and polymers.
- Scalability: CVD processes can be scaled up for industrial production, making it suitable for large-scale manufacturing.
- Complex Geometries: CVD can coat complex shapes and intricate geometries, making it ideal for applications where traditional coating methods may fail.
-
Challenges and Considerations:
- High Temperature Requirements: The elevated temperatures required for CVD can limit the types of substrates that can be used, as some materials may degrade or warp at high temperatures.
- Cost: CVD equipment and processes can be expensive, particularly for high-purity applications.
- Safety: The use of reactive gases and high temperatures requires strict safety protocols to prevent accidents and ensure the safety of operators.
In summary, the CVD process involves a series of chemical reactions that occur in the vapor phase, leading to the deposition of a solid material onto a substrate. The process is highly versatile and is used in a variety of industries to produce high-quality coatings and materials. However, it also comes with challenges, including high temperature requirements and cost considerations, which must be carefully managed to ensure successful outcomes.
Summary Table:
Aspect | Details |
---|---|
Definition | A process for depositing solid materials onto substrates via vapor-phase reactions. |
Key Reactions | Decomposition, combination, hydrolysis, oxidation, and reduction. |
Temperature | ~1925°F (1051°C) in a controlled atmosphere. |
Applications | Semiconductor manufacturing, optical coatings, protective coatings, powder production. |
Advantages | High-quality deposits, versatility, scalability, and ability to coat complex geometries. |
Challenges | High temperature requirements, cost, and safety considerations. |
Discover how CVD can enhance your manufacturing process—contact our experts today!