The density of sintered material is influenced by various factors, including the initial porosity of the green compact, sintering temperature, sintering time, particle size, and the application of pressure. The density is often measured as relative density, which is the ratio of the porous body's density to the non-porous material's density. Factors such as temperature and pressure enhance densification by promoting particle rearrangement and reducing porosity. Smaller particle sizes and homogeneous compositions also contribute to better densification. The final porosity and density of sintered materials are critical for determining properties like strength, conductivity, and durability.
Key Points Explained:
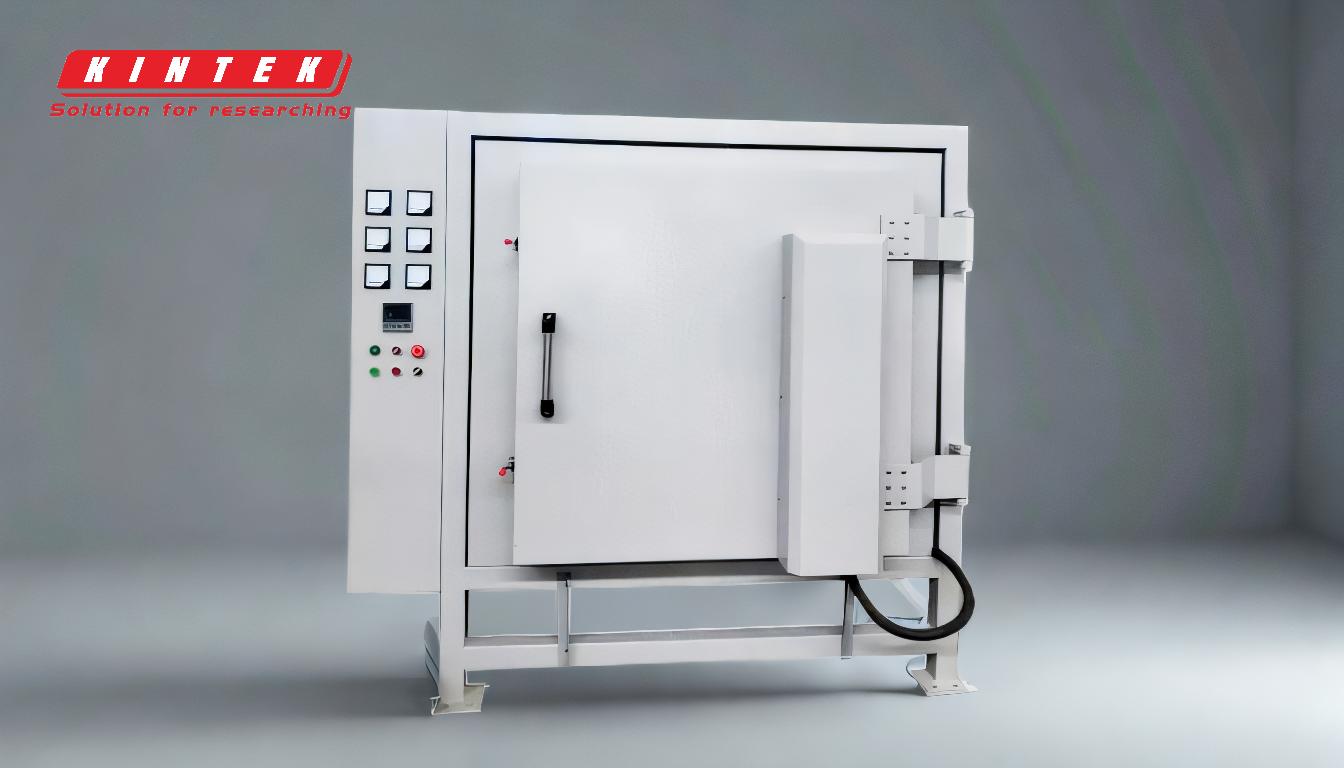
-
Definition of Sintered Material Density:
- Sintered material density refers to the mass per unit volume of the material after the sintering process. It is often expressed as relative density, which compares the density of the porous sintered body to the theoretical density of the non-porous material.
-
Factors Influencing Sintered Density:
- Initial Porosity of Green Compact: The starting porosity of the material before sintering significantly affects the final density. Higher initial porosity requires more extensive densification during sintering.
- Sintering Temperature: Higher temperatures generally increase the rate of particle diffusion, leading to better densification and lower porosity.
- Sintering Time: Longer sintering times allow more time for particle rearrangement and pore elimination, contributing to higher density.
- Particle Size: Smaller particles have a larger surface area to volume ratio, which enhances sintering kinetics and promotes densification.
- Pressure: Applying pressure during sintering can accelerate the densification process by forcing particles into closer contact and reducing porosity.
-
Measurement of Density:
- Relative Density: This is a common metric used to assess the density of sintered materials. It is calculated as the ratio of the porous body's density to the theoretical density of the non-porous material.
- Porosity: Porosity is the ratio of the pore volume to the total volume of the material. Lower porosity indicates higher density.
- Pore Size Distribution: The size and distribution of pores within the material can affect its overall density and mechanical properties.
-
Impact of Material Composition and Sintering Atmosphere:
- Material Composition: Homogeneous compositions with uniform particle sizes tend to sinter more uniformly, leading to better densification.
- Sintering Atmosphere: The environment in which sintering occurs (e.g., air, vacuum, or inert gases like argon or nitrogen) can influence the final density by affecting oxidation or reduction reactions.
-
Practical Implications for Equipment and Consumable Purchasers:
- Durability and Performance: Higher density sintered materials generally exhibit better mechanical properties, such as strength, hardness, and resistance to wear and environmental factors.
- Application-Specific Requirements: Purchasers should consider the specific requirements of their application, such as the need for high strength, thermal resistance, or conductivity, when selecting sintered materials.
- Cost Considerations: The sintering process parameters, such as temperature, time, and pressure, can affect the cost of production. Understanding these factors can help in making cost-effective purchasing decisions.
-
Advanced Considerations:
- High-Temperature Sintering: For materials requiring high tensile strength, bending fatigue strength, and impact energy, high-temperature sintering may be necessary.
- Pressure-Assisted Sintering: Techniques like hot pressing or spark plasma sintering can significantly reduce sintering time and porosity, leading to higher density materials.
In summary, the density of sintered materials is a complex property influenced by multiple factors, including initial porosity, sintering temperature, time, particle size, and pressure. Understanding these factors is crucial for optimizing the sintering process and selecting materials that meet specific application requirements.
Summary Table:
Factor | Impact on Sintered Density |
---|---|
Initial Porosity | Higher initial porosity requires more extensive densification during sintering. |
Sintering Temperature | Higher temperatures increase particle diffusion, enhancing densification and reducing porosity. |
Sintering Time | Longer sintering times allow for better particle rearrangement and pore elimination. |
Particle Size | Smaller particles enhance sintering kinetics, promoting densification. |
Pressure | Applied pressure accelerates densification by reducing porosity and forcing particle contact. |
Material Composition | Homogeneous compositions with uniform particle sizes improve densification. |
Sintering Atmosphere | Environment (e.g., air, vacuum, inert gases) affects oxidation/reduction, influencing density. |
Need help optimizing your sintering process? Contact our experts today for tailored solutions!